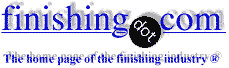
-----
Acid copper plating issue: Passive anodes
adv.: Supplier of Copper Anodes, Nickel Anodes, Bismuth Metal, & Other Metal Products for Industry & The Arts
Quickstart:
Acid Copper / Copper Sulfate plating solutions are popular with both hobbyists & professionals.
In a production environment though, a plating shop needs to be concerned not only that the first load of parts plates okay, but that the plating bath can be kept in equilibrium/balance so it will continue to plate okay for the next load and the thousand loads after that.
One issue the shop must battle is the tendency for the anodes
⇦ huh? to dissolve too readily, causing a build-up of copper concentration in the plating bath which can cause the anodes to go passive
⇦ huh?. One important way to battle this increased copper concentration is for the anodes to be made of "phosphorized copper" rather than pure copper: Read on ...
Q. I read that copper plating solutions should last for years with proper maintenance. In my solution which I used for about a month, I had about a 1/2 inch thick chunk of blue crystals in the bottom of my tank as well as on the sides and anodes. I assume this is copper sulphate. Is there any reason this would grow in there? Thanks, Rob
G. Touch1995
by N. Kanani
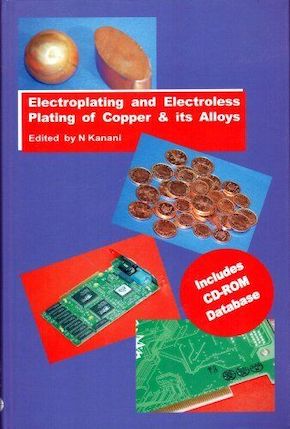
on eBay or Amazon
or AbeBooks
(affil link)
A. There is nothing wrong with the bath. The solution is just saturated. It has either been made up and used warm, then allowed to cool beyond solubility, or excess acid in the solution has continued to dissolve copper from the anodes which has pushed the copper sulphate ⇦ on eBay or Amazon [affil link] beyond the solubility limit. The latter is likely when vigorous air agitation ⇦ huh? is left on for long periods. The crystals are not a problem, unless they start salting out into the deposit. The best thing to do is analyze the solution, decant to remove excess copper sulphate, and replace any sulfuric acid and chloride necessary to return it to the vendor's recommended operating range (assuming use of a proprietary brightener ⇦ huh? ). Please dispose of all wastes according to applicable regulations.
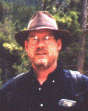
Bill Vins
microwave & cable assemblies - Mesa (what a place-a), Arizona
A. Hi.
Bill's answer is excellent, but I'll add one thing: are you using phosphorized copper anodes? Although probably not critical for a hobbyist, they would be important to a production plater ...
Plain copper anodes dissolve a little but faster than the copper plates out (i.e., the anode efficiency
⇦ huh? is greater than the cathode
⇦ huh? efficiency), so the copper concentration starts slowly building up. What happens after that gets a bit weird: the copper sulphate around the anode becomes so concentrated that it is non-conductive, slowing plating to a crawl, which exacerbates the build-up of the copper concentration.
Take Bill's advice, but make sure you are using phosphorized copper anodes 🙂
Luck & Regards,
Ted Mooney, P.E.
Striving to live Aloha
(Ted can offer longterm or instant help)
finishing.com - Pine Beach, New Jersey
Q. I'm doing some experiments with copper plating basically for breadboarding circuits with plated holes and learning the PCB manufacturing process.
I got a fairly functional copper sulphate
⇦ on
eBay or
Amazon [affil link] / sulfuric acid bath working from chemicals I got at the big orange home center and a constant current power supply. The solution is a basic copper sulphate/ battery acid
⇦ on
eBay
or
Amazon [affil link]
/ HCl and uses a copper anode made from a piece of copper grounding rod.
I got really bad results until I added citrate ions to the solution, after which I got excellent bonding and an unoxidized (but not smooth and shiny) finish that I can polish fairly easily. Since I was trying to do this without ordering any specialty chemicals, the citrate ions came from calcium citrate tablets that I dissolved in distilled water and decanted into the bath, leaving the sand/talc/whatever behind. The solution should have 0.1% citrate ions by mole count. I figured the small amount of calcium would plate out, and the microcrystaline cellulose doesn't seem to be hurting anything.
But that's not my question, just what I'm working with. I read that for electronics work that I should be using phosphorized copper anodes. In one article at this site someone had trouble with his phosphorised copper anode in that it was turning non-conductive.
So being really cheap I used a copper phosphorus brazing rod as an anode just to see what would happen, and sure enough, it turned black and non-conductive in less than a minute. Probably because it's 7%(!) phosphorus. I'm quite sure that using a copper-phosphorus brazing rod is the wrong material and I may have screwed up the solution, but it led to some questions.
My questions are
1) what is the purpose of a phosphorized anode?
2) what the heck is the black stuff that seems to evaporate when exposed to the air?
3) what is meant by the "polarized anode" and by what physical mechanism does it arise?
4) ignoring the phosphorus fiasco, what is the appropriate level of citric acid
⇦ on
eBay
or
Amazon [affil link] ?
SCHMITZ ENGINEERING, LLC. - Pinckney, Michigan
2005
A. Hi Dennis.
1. The purpose of the phosphorous is to slow down the anode corrosion so the copper does not spontaneously dissolve in the plating solution and cause a copper concentration which is too high. The black film from the phosphorous is good, not bad. However, the phosphorous should be about 1/20 of 1%, so your brazing rod has about 140X as much phosphorous as you want , and probably becomes totally non-conductive instead of slightly less conductive 🙂
2. The black stuff is the phosphorous.
3. A 'polarized anode' is an anode which is not conducting electricity properly --but it can have different causes. In the case of acid copper plating, it can perhaps be argued that it isn't actually the anode which is polarized but the solution around it. My understanding is that what happens is the anode dissolves too readily, causing the concentration of copper around it to be excessive, and this very highly concentrated solution does not conduct electricity well, causing the plating to slow down.
4. I'm not personally familiar with using citric acid in an acid copper plating bath.
Luck & Regards,
Ted Mooney, P.E.
Striving to live Aloha
(Ted can offer longterm or instant help)
finishing.com - Pine Beach, New Jersey
Q. Hello we have a problem with passive anodes in the copper acid bath.
We are copper plating on stainless steel.
Firstly we make Wood's Nickel strike
⇦ huh? , next we put copper layer on in the copper acid bath.
During electroplating of small parts we don't have any problems; but in the case of 3X bigger parts, the current in a few minutes decreases and the copper anodes are covered with a black coating. We tried to solve this problem by using additional anodes and increasing the sulfuric acid H2SO4 but it doesn't work. Anode to cathode ratio is 1:1. The test in the Hull Cell
⇦ huh?
goes correctly.
Composition of our copper plating bath:
Copper - Cu 60 g/l
Sulfuric acid - H2SO4 70 g/l
Temp 22 °C
Current at start 2 A/dm2
Mixed by air
Do you have any suggestions to correct this problem?
Plating shop employee - Cracow, Poland
2007
A. Waldemar,
For general purpose acid copper plating solutions: CuSO4 190-250 g/l, H2SO4 150-225 g/l, Chloride ion 30-80 ppm. You did not mention the chloride concentration in the bath, I hope you have one. It is quite natural to gradually build up a dark film on the anodes as long as the sulfuric acid concentration is where it should be. Two other things to check if the solution parameters are in range: Make sure you are getting good contact on your anode bar and cable connections. Check current on both the cathode and anode bar(s) with the high area (cathode) load in the tank. The readings should match current readings on your rectifier
⇦ huh? . Good Luck!
Process Engineer - Syracuse, New York
A. Hello Waldemar
As Mark said, in fact you haven't mentioned the chloride content, and also you need to make sure that the anodes have a phosphorus content.
- Aveiro - Portugal
A. Pull the anode bags
⇦ huh? , empty and clean the anodes of smut.
Then clean the baskets. Lastly, leach
⇦ huh? new bags and put the clean anodes in. Put them back on the anode bars. VERY easy problem. VERY easy cure. No chemical notions needed. Try it, you'll be thankful you did.
Warren, Michigan, USA
A. Dear Waldemar,
You have copper sulphate concentration too high. 60 g/L of copper in the bath means over 230 g/L of copper sulphate. Your bath cannot operate correctly at 22 °C because of thin layer of copper sulphate on the surface of anodes. The layer blocks current. You should reduce copper concentration or increase temperature up to 30 °C.
Best regards
- Poland
? Hello Waldemar,
which types of anodes are you using?
Regards,
- Mexico City, Mexico
A. Dear Waldemar,
The formation of dye scale is a common practice in bright acid copper bath, due to its brighteners and additives. You can go for cleaning of your phosphorised copper anodes twice or thrice a week, I hope this may not be a problem, if you are using less quantities of anodes. And however, please maintain chloride content of your bath as prescribed and see that the DM (demineralized) water you are using should not contribute chloride ion to your acid copper bath.
Good Luck!
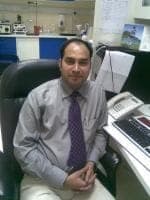
Shafiuddin A. Mohammed
metal coating shop - Dubai, United Arab Emirates
Q. Dear all,
We are also facing the same problem as my friend. While the anodes are not in use, we find that the white paste like formation over phosphorized copper ball anodes is causing decreasing current density in spite of maintaining the required chemical concentration. We have taken out the anodes and washed and put it back into the tank. Now it is okay but we have to check whether the same problem will repeat.
Regards,
- Chennai, TamilNadu, India
2007
A. SG,
I cannot stress enough - maintain the chloride level in the bath per supplier's specs. If the bath will be idle for more than three days, pull the anode baskets and soak in 5% sulfuric until they are ready for use. Rinse well, dummy plate
⇦ huh? at low CD for an hour or so. The sulfuric holding tank will etch a slight amount of Cu, but not enough to cause any harm. Good Luck!
Process Engineer - Syracuse, New York
Q. We are using acid copper plating bath for our printed wiring board copper plating process.
We are unable to maintain the copper sulphate concentration in plating bath and the concentration drops daily.
Control range :
CuSO4 = 9-12 oz/gal
H2SO4 = 24-26 oz/gal
After adjusting the CuSO4 concentration, it seems to drop to 8 oz/gal overnight.
There isn't any dilution on my bath.
There isn't leakage from the machine.
Ideally, the concentration should not drop as the process goes on daily.
Is this due to poor activation/anodizing of my copper anodes?
We've checked the copper anodes and they have a dark black film on the copper balls.
- Los Angeles, California
January 16, 2013
A. Hi Jake,
You may verify chloride content (usually ~50 ppm) in acid copper plating bath which does involve in copper anode dissolution. Also, please check if the copper anode you're using contains phosphorous (~0.04-0.06 wt%) and any abnormal high rectifier voltage observed. Copper anode without phosphorous and/or abnormal high rectifier voltage may result in poor anode dissolution.
Regards,
David
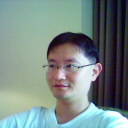
David Shiu
- Singapore
Q. Hi David,
Thank you for your response.
My bath contains 80 ppm chloride.
And we are using copper balls with 0.04-0.06 wt%.
Meanwhile, when you mentioned the voltage to be high, what would be the normal operating voltage for the anodes?
What would be considered as high voltage?
Thank you.
- Los Angeles, California
![]() |
A. Hi Jake, ![]() David Shiu - Singapore A. First, a black film on the anodes in your bath is normal. Second, acid copper baths I've run pretty much stayed below 3V. ![]() James Totter, CEF - Tallahassee, Florida |
Q. Hi David,
The voltage on my rectifiers are above 4V.
Is this considered high?
Meanwhile, there's only one contact point on my cathode bar to the rectifiers.
Will it be better to have both ends on the bar connected to the rectifier?
My plating current is only between 3 - 6 Amperes.
This is rather low compared to 100 A that you are doing right now.
Appreciate your comments and input.
Q. Hi James,
What do you suggest for the plating surface ratio between anode:cathode?
Is 1.5:1.0 good enough?
What will be the maximum ratio?
Thanks!
- Los Angeles, California
![]() |
A. Hi Jake, ![]() David Shiu - Singapore A. Try increasing the ratio to 2:1 anode to cathode, and the anodes should extend below the bottom of the cathode to some extent. 4V seems a little high, but increasing the anode area should bring that down some. ![]() James Totter, CEF - Tallahassee, Florida |
Q. Hello Sir/Madam,
bright acid copper anodes get gray instead of black and plating becoming very very slow. Rectifier voltage goes up while plating in ON ... normally it goes down (e.g., 1 volt goes 1.2 or 1.4). Before it was set to 1 V goes 0.9 or 0.8V
In my area no hull cell testing no lab for electroplating test. I did clean it was working fine mirror finish, but after few hours same problem.
Check attacked pictures. We use bags; they where normal from outside inside it was some black & gray. Using Phosphorized copper 0.04 to 0.08% anodes. Cu anodes are then put in Ti basket and then wear bags.
2nd picture was taken about 72 hours -- second time cleaning seems darker color than 1st picture.
Regards,
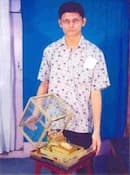
Dipen Pattni
jeweler/goldsmith - Dar-Es-Salaam, Tanzania
November 12, 2013
![]() |
A. Hello Dipen, Process Engineer - Mesa, Arizona, USA A. Hi Dipen, ![]() David Shiu - Singapore |
Dear Sir,
I did not reply until now because I had given Cu solution for test but seems they did mistake. Attached is analysis report.
I'm planning to do zinc dust
⇦ on
eBay or
Amazon [affil link]
, carbon treatment and then add 1st brightener and start working.
Thanks,
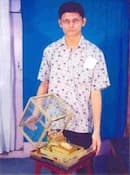
Dipen Pattni
jeweler/goldsmith - Dar-Es-Salaam, Tanzania
Ed. note: We cropped out the name of the test lab because they understandably wouldn''t want their name on copies they do not have control over or which could be altered.
Q. Hi,
Got new report from India for same Acid copper solution says:-
copper sulphate/229.59 (gm/lt)
sulfuric Acid/ 79.35 (ml/lt)
Chloride / (49.63 ppm)
Copper metal 58.42 (gm/lt)
Advised to make 30% dilution ... add 3 ml/lt hydrochloric acid (32 ml/lt), carbon treatment ... add 1st & 2nd brightener.
Regards,
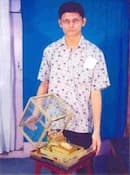
Dipen Pattni
jeweler/goldsmith - Dar-Es-Salaam, Tanzania
Current problem with acid copper
Q. Lately I have been having a problem with my acid copper. After I put in the pieces to copper plate, the amps go down to zero. It is like it loses contact. It resists for about five minutes then slowly lowers until zero. All contacts are clean but I noticed that the anodes blacken quickly.
John PerilliEmployee - Italy
October 25, 2018
(affil links)
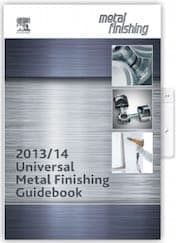
free pdf is currently available from academia.edu
A. Hi John. It certainly sounds like your anodes have gone passive. What type of copper are they, and are you monitoring your chloride level?
Regards,
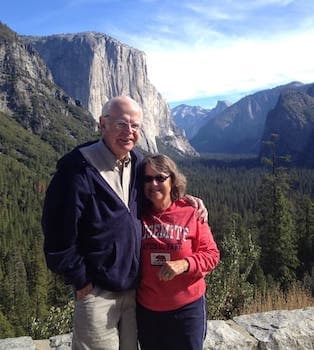
Ted Mooney, P.E. RET
Striving to live Aloha
(Ted can offer longterm or instant help)
finishing.com - Pine Beach, New Jersey
A. PASSIVE ANODE PROBLEM IN YOUR ACID COPPER BATH.
YOU ARE RUNNING LOW CONC.OF copper sulphate NEEDS TO BE 190-250 G/L, CHECK YOUR RECTIFIER AND CONTACT WORKING RIGHT, CHECK YOUR CHLORIDE CONCENTRATION IN ACID COPPER BATH.
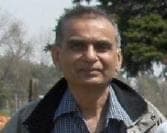
Popatbhai B. Patel
electroplating consultant - Roseville, Michigan
by Terrance H Irvine
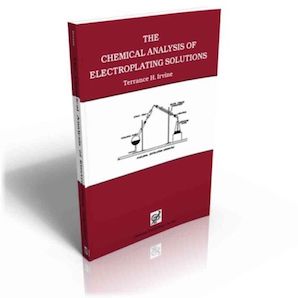
on eBay or Amazon
or AbeBooks
(affil link)
by Langford & Parker
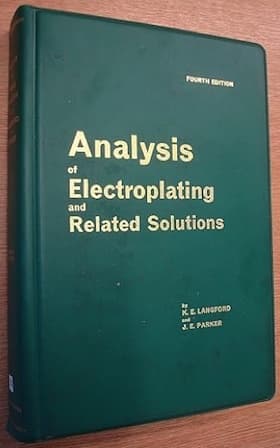
on Amazon
or AbeBooks
(affil link)
Q. Sorry to ask another question, but I would like to know how to check chloride content and what it is. I have little experience in acid copper plating.
John Perilli [returning]- Rome, Italy
A. Hi John. There is an excellent discussion of chloride analysis in acid copper plating baths on thread 0885.
If you have little experience in acid copper plating, the Metal Finishing Guidebook provides a good introduction, and there are specialized texts available. For more info about analysis of plating baths, Irvine and Langford & Parker⇨
are the "go-to" references. Best of luck.
Regards,
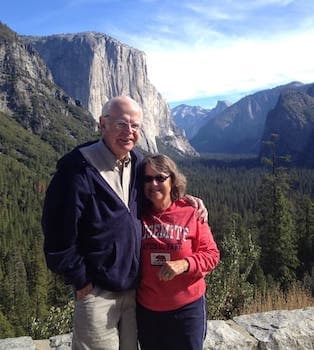
Ted Mooney, P.E. RET
Striving to live Aloha
(Ted can offer longterm or instant help)
finishing.com - Pine Beach, New Jersey
Thank you for your reply!
- Rome, Italy
Q. Dear all experts,
I am performing copper plating on stainless steel wire with usual acid based copper plating solution with copper anodes in the basket. What I have observed yesterday that the copper anodes, part which are immersed in the electrolyte solution, is turning into black. It seems that it is a black film of something, unknown, is being deposited. That film can be removed by water rinsing or by rubbing on the surface. Does anybody has any idea what is that film and why it is being built? The concentration of H2SO4 is fine. Chlorine content is not measured yet.
Kind Regards,
Ridwaan
- Karachi, Pakistan
July 2, 2020
Ed. note: As you will read on this page, that blackness on the anodes is normal and desirable and the result of the phosphorous in the anode.
Q. My copper sulphate content is continuously decreasing in acid copper bath. I have also monitored the drain valve, there is no leakage or wastage of the solution. Kindly suggest me a solution to overcome this issue.
Annie Tahir- Lahore, Pakistan
July 6, 2020
A. Hello Annie. You are electroplating copper out of the solution -- it is going onto the parts. But what is supposed to be happening is that the copper anodes should be dissolving into the solution in proper proportion to keep the copper concentration stable. It seems that your anodes have gone passive. Please study this thread and threads 31751 and 44771.
Luck & Regards,
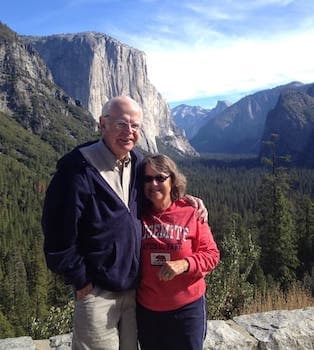
Ted Mooney, P.E. RET
Striving to live Aloha
(Ted can offer longterm or instant help)
finishing.com - Pine Beach, New Jersey
Hello there,
We have the same problem with black film on the copper anodes. I just got the chemical analysis result which says that:
Cu = 53 g/L
H2SO4 = 128 g/L
Chloride = 48 mg/L.
It seems that the sulfuric acid amount is more than double of the suggested amount (60 g/L). I am going to take out some amount the copper bath and will dilute the rest with water to reduce the sulfuric acid value.
I will let you know guys.
Thanks for the wonderful thread on this issue.
Kind Regards
Ridwaan
- Karachi, Pakistan
Ed. note -- Readers: As you have read on this page, blackness on the anodes is normal and desirable and the result of the phosphorous in the anode.
adv.: Supplier of Copper Anodes, Nickel Anodes, Bismuth Metal, & Other Metal Products for Industry & The Arts
Q, A, or Comment on THIS thread -or- Start a NEW Thread