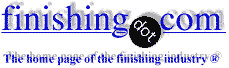
-----
Microcracking of electroless nickel over kovar substrate when exposed to 320 C
Q. Hello,
I have kovar (ASTM F15) parts that are plated with high phosphorus electroless nickel (ASTM B733 -97 type V) at ~250 micro-inches thick. When the substrates are placed into a hydrogen/nitrogen belt furnace for soldering, at any temperature over 320 °C the nickel gets small microcracks in the surface that cause hermeticity failures.
Is the cracking due the high phosphorus content, the temperature, the substrate material?
Any insight would be helpful.
Manufacturing engineer - New Bedford, Massachusetts
2007
![]() |
A. EN deposits have a very low ductility (1-3%). They also suffer a volume shrinkage derived form the formation of a crystal structure at that temperature range which is dependent on the P level. Even though, thin deposits like yours shouldn't be a problem. A high initial stress in the plating due to improper chemistry and/or operating parameters of the bath will definitely change the situation. Try with a freshly made EN bath at its optimum recommended parameters. Monterrey, NL, Mexico A. We regularly precipitation harden via 400C baking electroless nickel without noting the microcracks you've noted. This is especially noteworthy given the fact that you're seeing this on high phosphorus electroless nickel with is the least crystalline in nature, has the highest ductility, and, in general, exhibits the lower stress. This indicates that it's not likely the temperature and shouldn't be the EN coating. This would then suggest the substrate - what happens when you bake an uncoated part? ![]() Milt Stevenson, Jr. Plating shop technical manager - Syracuse, New York |
The substrate material is in perfect condition.
There are no adhesion issues, except for the cracking.
Our company has found a direct correlation between the temperature and the thickness of the plating deposit, but we have yet to find the root cause of the cracks.
I have a table (in excel) showing the correlation (please request if it would help)
- New Bedford, Massachusetts
A. Again, please note that EN (specially high P deposits) will always shrink when exposed to temperatures over 200-250 °C. This is a result of a change in its internal structure that goes from amorphous (no crystalline structure) to a crystalline face centered structure where P goes out of solution and forms nickel phosphides that precipitate in the matrix. This effect varies directly with the P content (higher P = higher shrinkage, no P = no shrinkage). Also, please remember its ductility is very low and greatly affected by contaminants, operating parameters, chemical balance and age of solution (which builds up by-products that also act as contaminants).
Guillermo MarrufoMonterrey, NL, Mexico

Q, A, or Comment on THIS thread -or- Start a NEW Thread