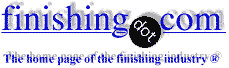
-----
Electro Nickel Plating Adhesion Problem; nickel plating keeps coming off!
Doing business with a roll-to-roll electronickel plating on stainless steel (STS301), we encountered a plating adhesion problem. The substrate is STS301, 0.075 x 200, and we give the substrate a
0.25um-thick nickel plating. We have done this for the past four months but had not such a serious plating peel-off problem until a recent date, when this peeling-off problem began to break out ; besides, it occurred on the shinny side only, sometimes whole of the shinny side but mostly the middle part only. We could see the nickel plating noticeably coming off from the substrate through a tape-pull test.
We could not find any change in production conditions or in any factors but the weather conditions. Actually by the time we face this problem the temperature suddenly went down and we are not yet keeping the line as warm as before.
We are already struggling for days but haven't even a clue. Could it be just because of the cold weather?
Plating shop employee - Korea
2007
Plating on stainless steel requires a Wood's Nickel strike, Hunchim. If you have not been doing that, you have just been very lucky to be working with fresh enough stainless steel previously that you got marginal adhesion. Or maybe unlucky enough because it may all have to be recalled.
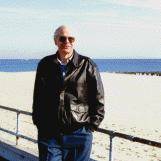
Ted Mooney, P.E.
Striving to live Aloha
(Ted can offer longterm or instant help)
finishing.com - Pine Beach, New Jersey
2007
2007
Which would cost less between nickel plating and nickel removal? Doing roll-to-roll nickel plating on stainless steel strip (0.07x
200mm), it's always such a pain to see too much scrap, most of which were these days caused by plating adhesion problem. As it is a roll-to-roll plating that requires high standard quality, sometimes even a partial problem forces us to scrap the whole roll. Whenever I see them scraped, I think if I could revive them by a re-plating after removing the plating from the substrate and with regard to that let me have some questions:
1. Is there any good system that can perfectly remove the plating from the substrate?
2. The plating removal will take another cost anyway, would it cost less than plating, or more?
Thank you.
Product Designer - Korea
First of three simultaneous responses -- 2007
The tape test is not a very stringent test for nickel plate.
Nickel can be removed from SS by machining, by grinding and by chemical stripping, normally with diluted nitric acid.
Stripping is not cheap. Counting labor and chemicals, equipment, exhaust/ scrubber and disposal costs, My thought is that it is nearly the same price as plating. It has been my experience that there is a much higher failed adhesion on SS after it has been stripped than original plate (with the same activation process).
- Navarre, Florida
Second of three simultaneous responses --
If it worked for several months then I will assume you DID have a Nickel chloride Strike, then with time, the metal built up in the strike and it quit being a low efficiency hydrogen evolving "strike" and became a high efficiency plating solution which will not bond to stainless steel.
Do not use S-rounds in the strike. Use Rolled Depolarized Nickel anodes and take them out when not in use.
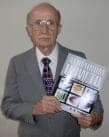
Robert H Probert
Robert H Probert Technical Services

Garner, North Carolina
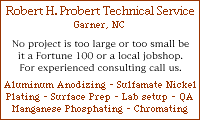
2007
Third of three simultaneous responses --
You can strip Nickel from Stainless steel by dipping in nitric acid.
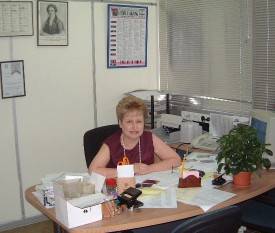

Sara Michaeli
Tel-Aviv-Yafo, Israel
2007
2007
Dear Sirs,
Thank you very much for the valuable replies.
I have a question of you Mr. Probert with regard to the part saying that the metal built up in the strike and it quit being a low efficiency hydrogen evolving "strike" and became a high efficiency plating solution which will not bond to SS and I'd like you to give me more detailed explanation about this. Thank you.
Just for your reference, we are using R-Round nickel and while not in use, we keep the nickel anodes away from the solution by draining.
And I have another question of you all and could the sludge or residue, which forms in the anode bag as the nickel dissolves, be any cause of the peel-off so that anode bag cleaning would help?
Best regards,
Hunchim Choi
- Korea
2007
Mr. Choi,
Your adhesion problem is most likely due to inadequate cleaning and activating of base metal (stainless steel in this case), not relating to changing in weather condition. It worked OK in the past four months because you probably had new cleaners, new acid, and new nickel strike. You now have adhesion problem because your cleaners and acid are getting old and contaminated. Your nickel strike may also contaminated with other metallic impurities from dragging-in or from nickel anodes itself. I suggest the following recommendations,
1. Slow down the speed of plating line to increase cleaning time.
2. Make new cleaners and acid, or make chemical additions to boost up their strength.
3. Increase the temperature of cleaners (keep between 160-190F). Heating acid solution between 100-130F will be helpful.
4. Make new nickel strike solution or at least dummy and make chemical adjustment. Keep nickel chloride about 30-32 oz/gal and hydrochloric acid about 16-20% by volume,
Hope these information may help you to solve your adhesion problem.
Regards,
- Chicago, Illinois
Dear Sirs,
Thank you very much for all the valuable replies that helped me to provide some sources for our engineers. Since this month, our line has been working normally. I wish I could, but to be honest it's too much for me so I will jsut give you a short explanation about major two actions:
Fistly, we have kept the live roller closer to the electrodes. Before it was located away from the electrodes because, while being kept close previously, it caused frequent electric sparks that used to ruin the substrate (SS) but we found out, while they are kept away, the electric resistance rises and it deteriorates the current flow, though it helps to decrease the spark problem, so we replaced the live roller close to the electrodes for better current efficiency.
Secondly, our plating line is a horizontal type, not the common vertical type, so it has a weak point that the substrate is likely to be exposed to the air longer. Particularly, the nickel plating bath that comes following pure water cleaning bath was kept far away - about 2 meters - from the pure water bath so that the substrate had to be exposed to the air for much longer time (about 10 sec). We didn't know what chemical reaction might happen on the surface while it's exposed (even at this cold weather) so we set up some pure water cleaning baths in between to shorten the exposing time. We are not sure if this action was effective but anyway the result tells us it might be.
Besides, there have been lots of trial and error that I can hardly enumerate but we did make every solutions all new before the above two major actions.
Thank you.
- Korea
2007
adv.: Supplier of Copper Anodes, Nickel Anodes, Bismuth Metal, & Other Metal Products for Industry & The Arts
Q, A, or Comment on THIS thread -or- Start a NEW Thread