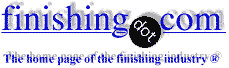
-----
Electroless Nickel Plating of Thin Parts
2000
One of our contractors has inquired about the feasibility of plating a brass ring (having a thickness of 0.021-inch) with electroless nickel per MIL-C-26074 [⇦ this spec on DLA]. This is the engineering drawing requirement, but they feel the part is too thin to plate with a thickness of 0.0005-inch on each side. Has anyone plated something this thin to a thickness of 0.0005-inch before? Is it feasible?
Thank you,
Marc PepiUS Army Research Lab - APG, MD 21005-5069
First of two simultaneous responses--
Part thickness is only applicable from its ability to cary electricity if it is being electrocleaned or electroetched or electrostruck. Brass is a good conductor of electricity, so it should not pose a problem. This assumes that the part is substantial enough to withstand racking if any of the first paragraph apply.
I used razor blades for thickness checks (plate rate) and took them a lot higher than 0.0005
James Watts- Navarre, Florida
2000
Second of two simultaneous responses--
Marc, I'm not sure if I understood your question, but 0,0005 inch is x25,4x1000 = 12.7 microns. In our shop we plate typically 4-7 microns with EN. So actually you have to immerse the detail longer than normal to achieve your desired thickness. Sven
Sven- Sweden
2000
2000
Hi Marc:
Have you considered CVD as the solution?
Plating a piece of the dimensions you describe should be no problem. We have experience of coating with pure nickel a variety of complex shapes and sizes with a thickness from 0.5 microns to one inch. The ring can be heated to our deposition temperature (about 360deg.F) inside the deposition chamber and the nickel will deposit in a few minutes. The economics of this process are best achieved by depositing a similar thickness of nickel on several pieces simultaneously, if possible.
The process we use is chemical vapour deposition, which is not a "line of sight" process, so we can deposit inside cans or complex shapes uniformly. We deposit pure nickel and a brass substrate will bond very well with nickel in our process. Our process deposits nickel at the rate of 0.010" per hour and the resultant nickel coating is very uniform.
Sincerely
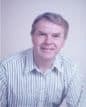
Mick O'Meara
- Toronto, Canada
Q, A, or Comment on THIS thread -or- Start a NEW Thread