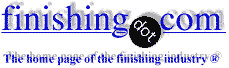
-----
Oxidation of silver nickel electrical contact
Q. Need your advice on the following:
In the area of Silver plating of contactors (say for Switchgear products), how many years of life one can expect without tarnishing? Plating thickness is in the range of 5-25 microns on copper. How do I protect the silver coating without formation of silver sulfide and without loosing the electrical conductivity. Organic coatings or Rhodium plating has one or other disadvantages. Do you suggest any alloy plating?
Crompton Greaves
1998
A. I do not know what is your substrate material. I assume it is copper. There are two choices I could think of. For low frequency contact use, low temperature applications, your better bet would be cadmium plating. This material is also better for applications in humid environments. That is why it is used for connector plating. Be careful about the use of cadmium though because cadmium, being toxic, is not accepted in many countries. The other method would be gold plating.
Mandar.
- Fort Collins, Colorado
1998
A. LIFE OF SILVER CONTACTS measured in the terms you use - without tarnish -is virtually nil. But why worry about tarnish? It is generally very conductive and for most electrical contacts where applied voltage is generally quite high(in excess of 10 volts) the tarnish will not be electrically noticed. For electronic contacts, where very low contact resistances may be required, you probably cannot use silver - depends upon the application. Very low contact resistances have to come usually from gold or even unpolished rhodium (very expensive) but for general purpose switchgear tarnished silver is excellent. It is also one of the best finishes for switches in a marine environment.
Peter Vivian1998
Silver plating on electrical contact springs
Q. I have been cycle testing spring probes used in circuit board testers to determine the best and longest lasting type of plating to be used on the spring itself.
So far, silver plate over a copper strike, on a spring wound from music wire ASTM 228 seems to give the best results. The silver springs even outlast raw unplated ones. I believe this is due to the lubricating properties of the silver, and it's malleability. Previously, we were plating gold over electroless and/or sulfamate nickel, and having problems with premature spring failure. I have two questions. One: does anyone know what the conductivity of silver sulfide (tarnish) is? And secondly: can anyone give any reason why not to plate these springs with silver.
Thanks to all for your input.
Test Connections Inc. - Upland, Ca U.S.A.
2000
A. Hey Brian,
Silver should be fine to use as the plate and if you are getting the spring cycles you may not need to bake the parts after electroplating. Silver will form a very light chromate film (will pass current) if you just want more protection or if you need to bake and then need to snap the surface back.
Sorry, don't know the conductivity of the sulfide, but its not much of a conductor. 3M makes some protective papers that can be placed along with the parts in good packaging (sealed plastic bag 4 mils thick or more) and will increase the shelf life. Gold over the silver would also work (silver will, with time, come to the surface of the gold so you may need more than a flash).
Regards,
Wendt Dunnington - Royersford, Pennsylvania
2000
Maximum-Minimum Current for Silver-Cadmium Oxide & Gold Electrical Contacts.
Q. Gentlemen,
I am wondering if you could please help me by answering the following questions:
What is the working voltage and current range for AgCdO 10% contacts (90% Silver, 10% Cadmium oxide) and at what kind of electrical load (if AC load, please specify whether is resistive, inductive or capacitive)?
I would appreciate your help if you could tell me the same for gold contacts (electrical current and voltage working range, i.e. maximum and minimum).
Thanks
Francisco Castaneda
Controles de PresiÛn de Cd. Ju·rez - Ju·rez, Chihuahua, MÈxico
2001
Sliding electrical contacts suffer silver to silver galling
Q. I am having problems with galling on a silver to silver sliding electrical contact. The problem is manifesting itself after assembly and before any current is applied. The galling is causing a gritchy sliding surface which is interfering with smooth motion of the contact (the contacts are under only a few grams of load). Only a few % of the contacts produced have this problem, I am puzzled as to what is causing phenomenon. Under close inspection both surfaces display distinctive galling characteristics (not very pretty).
Has anyone ever experienced silver to silver galling?
electrical components - Springfield, Massachusetts
2003
![]() |
A. Pure Silver is a very soft metal and is a great lubricant when running against a harder metal, but will gall very easily against another soft silver surface. Try using a harder silver (alloy) on one of the surfaces. James Watts- Navarre, Florida 2003 A. Hi, - Atlanta, Georgia, USA 2003 |
A. We solved this problem of galling Silver contacts by wiping them with a damp cloth. Wiping with Alcohol or acetone ⇦ on eBay or Amazon [affil links] Warning! Flammable! has the same effect. We don't quite understand the process (it seems to clean off the brightener additives or create a thin oxide layer (?)) but it works great. Aging the plating helps too, either oven cure at 150 to 200 °C or just letting it sit for 2 weeks.
Holger Schultelectronic mfg. - Montoursville, Pennsylvania, USA
2005
Q. Dear Sir/Madam,
I would like to know how could you confirm if the silver nickel cladding area of an electrical contact has been oxidized? Recently, we have encountered problem of motor failure & we suspect it is due to the electrical contact plated with silver nickel. We reckon that an insulating oxide film has built up causing low or no electrical conductivity. Unfortunately, we do not have any strong evidence to prove it. In addition, under what circumstances will the silver nickel oxidise or corrode?
Thanks With best regards,
Engineer - Singapore
2004
A. Please give the composition of the silver nickel. The metals nickel and silver have almost no solubility in each other, and "nickel silver" commonly refers to alloys such as C75400 (65Cu-20Zn-15Ni) and C97600 (64Cu-4Sn-4Pb-8Zn-20Ni), which have the appearance of silver but only 5-7% of its conductivity.
Heating can cause oxidation. Corrosion usually leaves obvious corrosion products. A surface oxide can be detected with a volt-ohm meter and some judicious scraping.
- Goleta, California

Rest in peace, Ken. Thank you for your hard work which the finishing world, and we at finishing.com, continue to benefit from.
2004
A. Maung,
Silver don't oxidation, silver can build a sulfurization. You can protect silver from this by passivation.
Regards,
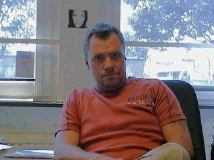
Anders Sundman
4th Generation Surface Engineering
Consultant - Arvika,
Sweden
2004
October 12, 2009
A. Anders is absolutely correct, its not oxidation.
Also the blackening of silver caused by sulfurization is conductive and does not normally need to be cleaned.
This is one of the reasons that silver plating is used.
It is highly unlikely to be the cause of problems with your motor.
Whatever you do, DO NOT attempt to clean silver plating using any abrasive means. This will do more harm than good.
Hope this helps
Henry
Electrical engineer > 25 years experience with electrical contacts - Shenzhen China
Q. We have a problem with heavy tarnish on silver-plated spring contacts which are difficult to reach and impossible to abrade. Is there a chemical treatment which will reduce the silver sulfide to metallic silver? Would heating work?
Help?
- Elliot Lake, ON, Canada
2006
Silver plated brass electrical contacts are fouling
December 16, 2011Q. Dear,
My brake fluid tank on vehicle has a mechanical contact between electrical terminal and disc. It is connected with combimeter.
So when brake fluid leaks, warning lamp can light due to direct contact between electrical terminal and disc.
Electrical terminal and disc are brass plated with silver.
And circuit current is max. 6 mA to min. 4mA.
But, I have problem: no warning light on when electrical terminal contacts disc.
So I heard that low current may cause no light on even though terminal and disc are contacted.
First, we suspect silver plated may cause no warning light on but even though passivation is applied, it still has problem.
Second, is it possible to make small current on circuit no warning light on?
Third, when we compare silver plated, tin plated or gold plated, what is better with small current?
Normally automotive industry prefer Tin plated or Gold plated.
But, could you explain that silver plated is normal use for electric terminals?
Could you explain what silver plated has advantage and disadvantage compared to Tin plated?
Thank you in advance.
- Korea
A. BARRIER PLATE IS A MUST for BRASS
Before Bright Silver or Tin Plating on connecting LUGS/TERMINALS a BARRIER PLATE of Bright Nickel is RECOMMENDED to prevent ZINC in BRASS migrating with Silver or TIN, which gives intermittent problematic connection.
surface finishing chemicals - Bangalore, India
December 21, 2011
Q. Thank you for your comment.
I have one more question.
I heard that barrier Nickel is must for gold plating on silver.
Do you mean that it is a must for silver plating on brass?
- Korea
December 22, 2011
Bi-Metallic contact Rivet AgNi15
Q. Dear All,
I am a switch gear designer. Now I am designing a switch which will be used in Elevator Industries, so the price component is an important thing.
I am using 2 bi-metallic Rivet AgNi15. I have to reduce the cost of the rivet. What are possibilities of reducing the cost or any other method to change Ag Ni15
Regards
Manoj
- India
January 17, 2020
A. Hi. I know very little about this subject, but quick googling indicates that AgNi is already the lowest cost of the silver-based contact materials. It is possible perhaps that you could use plated copper-based rivets, but that substitution is an electrical engineering project, not simple equivalence.
opinion! Earlier in my career I did a stint with a well-known manufacturing technology consulting firm working on cost-reduction programs, and came to decide that my own philosophy is that there is no such thing as a successful cost reduction program. By their nature they imply that the design & quality of the product is already good enough and it's okay to not improve upon it and maybe even safe to let the quality slide by a measured amount. The premise is doomed to failure :-(
Focus on how to make that switch better in some way and you might well find that it leads to lower cost :-)
Regards,
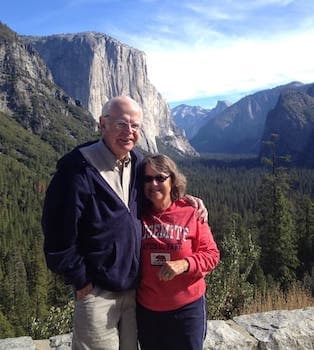
Ted Mooney, P.E. RET
Striving to live Aloha
finishing.com - Pine Beach, New Jersey
January 2020
Thermally conductive and salt-water resistant finish
Q. Hello, I'm trying to find choose best material that will be salt water resistant, and have good thermal conductivity. In my head I have two choices [for substrate], copper and aluminium -- but both are easy corroded in salt water so I think about protecting it from oxidation, without much lowering its thermal conductive properties. So any powder coating in not good. That's why I think about plating it, or anodizing, so maybe someone knows the answer, what will be most corrosion resistant, copper electroplated with nickel, or maybe aluminium anodized or aluminium electroplated with nickel? it will be in salt water (sea water)
Mat Froehobbyist - Canada
February 25, 2020
A. Hi Mat. Assuming gold plating is too expensive for the application, electroless nickel plating on copper would be my choice.
Regards,
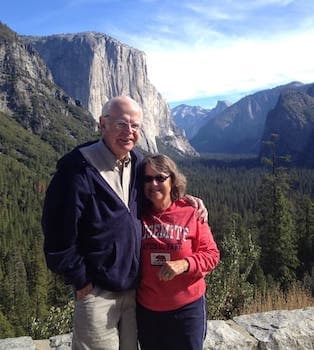
Ted Mooney, P.E. RET
Striving to live Aloha
finishing.com - Pine Beach, New Jersey
February 2020
A. Hi Mat
What is the purpose of the coating?
Wooden ships were commonly plated with copper sheets. The phrase "copper bottomed" is still used to describe reliability and marine archeologists recover copper and brass fittings from wrecks in excellent condition.
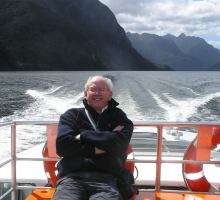
Geoff Smith
Hampshire, England
February 26, 2020
A. They don't use pure copper, but cupronickel; normal pure copper is not resistant to salt water.
Mat Froe [returning]- Canada
February 27, 2020
February 27, 2020
A. Nelson's Navy and the East India Company used plain copper.
I have seen no evidence for the use of cupronickel and it is unlikely to be sufficiently ductile to be rolled into the sheets used.
Between 1829 and 1833, Percival Norton Johnson was the first person to refine cupronickel in Britain.The Royal Navy had started coppering the entire fleet from 1788.
Geoff Smith
Hampshire, England
Q, A, or Comment on THIS thread -or- Start a NEW Thread