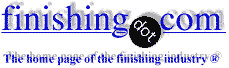
-----
Bad finish on stainless parts after passivation
Q. I work for a small medical device company and we are having a problem with the appearance of some of our passivated parts. The parts are 416 steel and some(not all) of the parts from the same lot come back from the passivator (which we outsource) looking almost like they were galvanized(dull and rough). They were beadblasted prior to being sent out and had a satisfactory finish before passivation. The blasting media is glass oxide. Any suggestions or remedies will be greatly appreciated.
Mike CarusoQ.E. Medical device manufacturer - Islandia, New York, USA
2007
![]() |
A. What does your passivator have to say? - Navarre, Florida 2007 2007 A. It sounds like the passivation bath may have etched your parts, but it is hard to tell without looking at them. ![]() ![]() Lee Kremer Stellar Solutions, Inc. ![]() McHenry, Illinois ![]() |
November 14, 2019
Q. Hi, good day I have the same issue
I am experiencing issues with the passivation process, the parts (steel S41600) are coming out of the Process with a dark gray finish, brown and blue/purple spots.
I have tried processed parts and raw bar stock with the same results.
The process steps are:
Step 1 Soak cleaner: New dimension supreme from MacDermid at 60 °C for 10 minutes, concentration 25 %, tank volume 51 liters
Step 2 Rinse DI water
Step 3 Emerald Acid : concentration is 5.6% citric acid ; the temperature is 35 °C, tank volume 51 liters
1. 45 minutes (standard time used previously) = the parts turn out dark grey almost black.
2. 35 minutes and parts still turn dark grey (According with AMS2700 the minimum time its 30 minutes)
3. 25 minutes the parts it not clean enough, they still have little shavings (according ASTM A967 the minimum it 20 minutes )
In each of the above times besides the dark/darker coloration spots are visible.
Step 4 Rinse DI water
Step 5 sodium dichromate at 5% at 65 °C, tank volume 51 Liters
a) 60 minutes according to AMS2700
b) 35 minutes according to ASTM A967
Neither of the above times makes a difference.
Step 6 Rinse DI water.
I've been reading that I need to hot alkaline clean. How hot the solution must be? Because if I raise the temperature the pH down; over 10 currently. I have it on 45 °C
Someone have other advice to fix this problem?
How can I re-work the pieces? Have been passivated but need to re-work ?
The pieces were passivated with citric acid and sodium dichromate.
MEFASA - Sonora Mexico
November 19, 2019
A. Aaron,
If the parts are etched, they would need to be refinished, via tumbling, electropolishing, or some other method.
416 is a free machining martensitic grade. This means the parts need to be:
1) Heat treated to full hardness, or they are likely to be etched severely and turned black.
2) Pretreated in an alkaline cleaner, or the sulfur will build up in the acid bath and on the surface of the parts, creating brown stains.
3) Passivated in citric acid buffered to a pH of 3 or 4, or light surface etching/discoloration may occur.
4) Rinsed and dried quickly to avoid flash rusting.
Sodium dichromate is not necessary to use with citric passivation.
Adv.
Let us know if we can help you with this.
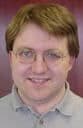
Ray Kremer
Stellar Solutions, Inc.

McHenry, Illinois
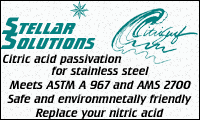
Q. Thanks Ray to your answer
1.- What do you mean with 'Heat treated'? the pieces need to be in oven? -- or a hot degreasing bath could work?
2- I am using the New Dimension Supreme from Macdermid, and that is an alkaline cleaner, how alkaline must it be?
3- The pH of citric acid bath is 2.09; can I rinse with sodium hydroxide?
- Sonora Mexico
November 20, 2019
A. Aaron,
Yes, heat treating means in an oven.
If you start to smell rotten eggs (sulfur) from your acid bath, then your alkaline cleaner isn't sufficient.
With citric acid , a water rinse is fine, but you can use sodium hydroxide solution followed by a water rinse if you prefer. Leaving it in the water too long might still create flash rust.
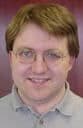
Ray Kremer
Stellar Solutions, Inc.

McHenry, Illinois
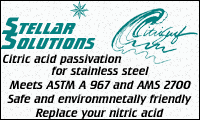
December 5, 2019

this text gets replaced with bannerText
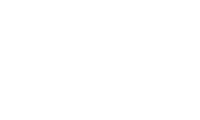
Q, A, or Comment on THIS thread -or- Start a NEW Thread