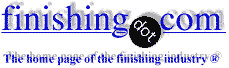
-----
Electroless Nickel on Sulfamate Nickel?
2007
Hi,
We need to repair an undersize steel component that has worn 0.004" down. The repair manual calls for an Electroless Nickel finish but Electroless nickel can only be deposited usefully to a depth of 0.0025-0.003". Our plater has recommended doing a Sulfamate Nickel deposit & grind to an even 0.002" surface, followed by a 0.0025" Electroless Nickel deposit. Followed by machining to the correct dimensions.
I've never heard of using an electroless nickel on top of a sulfamate nickel before, so I'm reluctant to sign-off on this. Has anyone heard of this being done before? Or can suggest a better technique for building up the part to the correct depth?
Thanks,
Design Engineer - Melbourne, Victoria, Australia
Dear Leigh,
I suggest brush plating.
Kind regards,
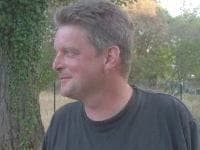
Sjamp van Esch
- Eindhoven, The Netherlands
2007
First of two simultaneous responses -- 2007
Sulfamate nickel of at least 0.003 per side after post plate machining can be followed by 0.001 of EN and should not require post EN grind, unless the tolerances are very tight or the post sulfamate machining is bad or the EN plater is marginal.
I am not in love with brush plating unless it is a one or two part run.
Have you considered using Chrome?
- Navarre, Florida
Second of two simultaneous responses -- 2007
Perhaps the plater is just trying to make his life easier. Answering your questions.
1- Fact. EN can be deposited to 0.005" and more.
2- Sulfamate nickel is suitable to plate EN on top.
3- Other alternatives include metal spraying, low energy welding, spark welding. Then machining/grinding and EN plating. In any case, validation by the writer of the specs would be required.
About brush plating which was suggested, it might be an economically attractive and perhaps valid alternative from the engineering point of view, but it would be somewhat limited by the part's geometry. Also it is not what your specs call for.
Monterrey, NL, Mexico

Q, A, or Comment on THIS thread -or- Start a NEW Thread