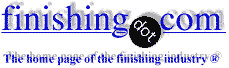
-----
Clear Iridite turned parts white
We had some machined and sand blasted 6061-T6 aluminum parts that had a clear Iridite finish applied by our vendor after which the parts turned white. Could this have led to the painting problem for our customer. Can you tell me what the problem is? Why would the parts be white colored? I thought that the parts should basically remain the same machined color after a clear Iridite finish is applied.
Thank you.
Buyer - Olathe, Kansas, USA
2007
Several thoughts on your problem and a little more description on the actual state of your parts might help resolve root cause investigation. First off, term "sand blast" is very vague: were they blasted wet or dry? was the media used spherical glass beads or jagged aluminum oxide or silicon carbide? what was pressure, distance, angle of blasting? All of these will have a pronounced affect on the results following "clear Iridite." Next, did the processing house actually have a true clear chromate conversion coating bath or do they use a yellow formulation and then bleach that back using hot water? The later is likely to leave a chalky powder as it basically dehydrates the otherwise hydrated chromate film. Lastly, white appearance could be attributed to blasting leaving an embedded abrasive in the part which had to be etched out using an aggressive acid (HF) or hot caustic. The acid would "whiten out" the aluminum's appearance, however, I wouldn't expect an impact on the ability to adhere to paint. Using hot caustic to get a uniform appearance, followed by poor rinsing might cause it to be chalky and negatively impact subsequent paint adhesion. My guess would be the yellow chromate, bleached out with hot water scenario - that too would create a chalky, perhaps white appearance, that would impeded a painter's ability to get good adhesion. Send me a before and after sample and I'll confirm.

Milt Stevenson, Jr.
Plating shop technical manager - Syracuse, New York
2007
2007
Parts are dry blasted with 100 grit aluminum oxide.
The parts are hand held during blasting and hence blasted at a multitude of angles with 20 PSI.
I have been told that we had these parts done in 4 batches and we did not vary our process. The first 3 batches of parts done by our chemical treater were ok but the fourth was not.
Buyer - Olathe, Kansas, USA
Q, A, or Comment on THIS thread -or- Start a NEW Thread