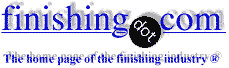
-----
2024 Burning Problems
I work for a small ma' and pa' plating shop that processes a great deal of work for various local commercial and aircraft companys. I am looking for any input that may aid me in successfully applying .002"
± .0004". My setup is a 3 ft wide, 4 ft deep, 8 ft long poly tank with a lead liner. 1/4" sheets of pvc further line the sides of the tank perforated with 1" holes to control cathode area. Basic copper bar and saddle setup with current be applied through only one saddle
(is this enough? or is it any different from running power to both ends of the bar?) No more than a 10 ft run of cables to a 700 amp rectifier. We run the tank temp at 38 to 42 degrees with air agitation. After a few surface area calculations I set my load amperage per a 36 amps/sqft current density with a 30 minute ramp time. In the past, I left the volts to climb freely at their own pace. Frequent problem with parts "burning" before 30 minute ramp time is even reached. I have just recently been using a different approach hittting my parts at half power for the first half of the ramp time, using smaller increments on the last half while letting the volts generally run up to about 20 by the time the full current density has been reached. At that point I set my dial to hold the volts in place, setting my timer for five minute intervals at which point I increase the volts by two until thickness specifications have been met. Using this, I can reach a thickness of .0014-.0015" with a
50 minute total load time.
Of course the load time will need to increase to obtain .002". Is that the answer though? Babysitting the load for an unefficient amount of time? Any thoughts are appreciated. Thanks
anodizer - Wichita, KS, USA
2007
First of two simultaneous responses --
First, I would get rid of the lead and probably the plastic.There are a number of articles on the use 0f 6063 for cathodes. This also allows you to add or remove as required to maintain a proper anode-cathode relationship and it is more efficient use of your electricity. Yes, even with only a 700 amp powersupply, you should apply power to both ends of the bus bar. You can either saddle it, or you could run a flex lead(s) to the other end with a bolt into the end of the bar.
I think that you are making life tough on yourself. Go to constant current with a ramp to the 36ASF.If a 30 min ramp still burns, switch to a 40 min ramp and even 50 if required. It takes a lot of voltage to build 0.002". If what you were doing causes burns, first check for how rigid your fixturing is. Second, use only aluminum and change fingers as required to keep a rigid mounting.
- Navarre, Florida
2007
Second of two simultaneous responses --
You did not say what the acid strength is. 2024 requires higher acid for hard coat. Also 36 ASF is very difficult if anthing else is marginal. I recommend you get the acid to 200-225 gm/L,the dissolved aluminum down under 8, spend 15 minutes ramping up to 24 ASF, then hold 24 ASF for about another 60 minutes. It sholud take a total of close to 75 minutes to get 0.0025. 36 ASF works in the lab, but is extremely difficult to hold in job shop conditions.
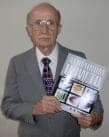
Robert H Probert
Robert H Probert Technical Services

Garner, North Carolina
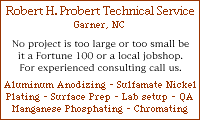
2007
Q, A, or Comment on THIS thread -or- Start a NEW Thread