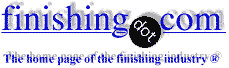
-----
Stripping Electroless Nickel From Heavy Metal Sinter
I have some spindle bodies that have been electroless nickel plated with a medium phosphorus solution to a thickness of
0.0003-0.0005". The base material is GEC heavy metal, a sinter consisting of 90% tungsten with 10% copper-nickel binder.
Due to a processing error I now need to strip the nickel but am worried about damage to the base material, especially as the sinter could be up to 7% nickel.
Does anyone have any ideas?
There was a suggestion that a nitric/sulfuric mixture may be the answer, but without knowing the ratios I am reluctant to risk production parts. Any help would be greatly appreciated.
Aerospace - Yeovil, Somerset, UK
2007
For any of you out there interested I have been playing, and in some cases scrapping, with various heavy metal bits in an attempt to find a satisfactory method to strip the nickel coating.
So far I have tried Nitric acid:sulfuric acid mixtures in the ratios of 1:1, 2:1, 3:1, 1:2, all of which successfully strip the nickel coating but also successfully strip the nickel/copper binder out of the base, making the surface look like the surface of the moon, more craters than flat areas! I tried concentrated nitric acid (70%), which stripped the nickel pretty fast yet still managed to strip quite a proportion of the binder out.
Out of desperation, and for want of a better idea, I even tried 50% dilution on the nitric. To my amazement it whipped the nickel off in next to no time and, if I was quick enough, with little damage to the base material. Any areas that are bare need to be protected as this solution aggressively attacks the nickel and will destroy the sinter.
My next step is to try an alkaline solution based on sodium cyanide, sodium hydroxide and a suitable organonitrate compound. It's not something I really want to play with, but I need to find something that will do less damage to the base than the nitric.
So if anyone has any ideas throw them at me and I will give it a go.
Aerospace - Yeovil, Somerset, UK
2007
The problem seems to be that the Ni-P alloy is tougher to dissolve than the basis Ni alloy sinter. Tough.
In my 5 minute instant expert Google search (heh), I saw that most of these nickel strippers, whether based on cyanide, or ethylene diamine, are specifically not recommended for Ni or Ni alloy substrates. Commercial products contain inhibitors, you might be well advised to try one of those.
Though you likely know, the commonly used nitro compound is meta-nitro benzene sulfonic acid, if memory serves. Possibly, a slightly more powerful oxidizing agent? I gather the oxidation state of the P in the deposit is less than it is in the phosphate ion; the phosphorus is the only differentiating property.
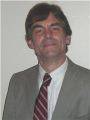
Dave Wichern
Consultant - The Bronx, New York
2007
2007
Dave,
Thanks for the advice. Like you, I tried the instant expert approach and came to the same conclusions. It seems to come down to the fact that the stripper needs to be able to strip the coating rapidly and evenly so that damage to the sinter can be minimised.
I am almost of the opinion that this is a one-hit process, get the plating wrong and you're up the proverbial creek. My attempts to rescue the parts I have is now starting to cost some serious money, so I am weighing up the cost of research against the cost of just starting again with new parts. Bit of a tough call, especially if things were to go wrong again.
Anyway, I still have a little room to manouvre so I will try a couple of other methods, including m-nitrobenzene sulphonic acid in cyanide solution. As they say "Live in hopes".
Aerospace - Yeovil, Somerset, UK
Q, A, or Comment on THIS thread -or- Start a NEW Thread