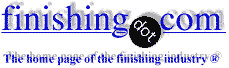
-----
Need Alternatives to Galvanizing for Power Line Bolts, Nuts, Lock Washers
Q. I work for a company which designs and manufactures connectors for power electricity application. I am looking for coatings to apply on our hardware to use for our tap connector on high voltage power lines.
Our issue is finding a suitable coating / plating to apply on a 3/8 x 3" long bolt with the appropriate nut and lock washer which will:
1) give us a reasonable corrosion resistance (at least 500 hours of Salt Spray).
2) reduce the coefficient of friction of the hardware so that the torque required to mate the connector can be reduced.
3) give consistent results for multiple assemblies.
We have previously tried Hot Dip Galvanize but the results were unsatisfactory - there is horrible consistency of torque for assembly because it is difficult to control the plating thickness.
We are aware of two possible technical solutions - the DACROMET and the GEOMET technologies.
However, DACROMET plating is part Chrome and is not accepted by RoHS, GEOMET has no Chrome and is accepted by RoHs.
We do not have a material engineer on our team so I'm left to research this from scratch.
Can anyone please suggest any other alternatives for plating that can be suitable for our function?
All input is greatly appreciated.
Thanks in advance,
Product Development - Markham, Ontario, Canada
2007
A. Hi, Yivgeni, welcome to finishing.com. An important thing to remember is that "500 hours of salt spray" is not a proper qualification for a project of this nature, i.e., selecting between potential coatings. The purpose of salt spray testing is to insure that the coating process is under control and consistent from batch to batch, not to anticipate real world life.
The mechanism of corrosion in a salt spray chamber is so different from the mechanism of corrosion in the real world that it is fair to say that there is no correlation at all. Some coatings like galvanizing derive their good real-world corrosion resistance primarily from the formation of stable corrosion products containing small amounts of compounds that cannot form in short-term salt spray chamber tests. In the real world, galvanizing outperforms (by decades & decades!) coatings that may beat it in a salt spray test. I'm not sure that you should give up on galvanizing (which has proved itself from the very beginning as the ideal coating for pole-lines & towers) before making sure that the thickness consistency issue cannot be solved. Despite salt spray ratings, I doubt that anything else at all will even approach the real-world corrosion resistance -- but you won't know for at least 25 years :-)
Geomet and Dacromet are proprietary zinc-rich dip-spin coatings. There are competitive brands but let's restrict the discussion to generic types of coating rather than claims that one brand is better or worse.
Another generic type of coating which would be thinner than hot-dip is mechanical plating / mechanical galvanizing. And still another along the same idea would be zinc diffusion coatings similar to Sherardizing.
Finally we have electroplated coatings. These are usually much thinner, and plain zinc electroplating probably would not do. But zinc alloy platings like zinc-cobalt, zinc nickel, and tin-zinc might. Of these, tin-zinc offers good lubricity (I believe it would be better than anything else mentioned here). You would need to find a good RoHS-compatible hex-chrome-free conversion coating, but I think this could end up a good solution. It is possible to add thread lubricant to other coatings, but when the service truck has been out in the mud on the fire road for 14 hours you'd like to not have specified an overly dainty repair protocol.
After looking into these, and ideas that may be offered by other readers, please come back with specific questions as they arise. Good luck!
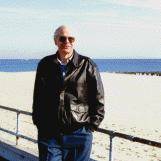
Ted Mooney, P.E.
Striving to live Aloha
(Ted can offer longterm or instant help)
finishing.com - Pine Beach, New Jersey
A. Silver plated stainless steel fasteners will provide everything you want and more.
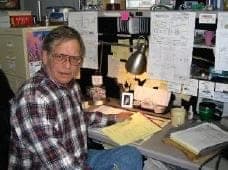
Jeffrey Holmes, CEF
Spartanburg, South Carolina
A. The problems encountered with galvanizing perhaps stem from a lack of process specifics.
Get ASTM A394, 'Standard Specification for Steel Transmission Tower Bolts, Zinc-Coated and Bare.'
Bolts, before zinc coating, shall have coarse threads with Class 2A tolerances per ASME B1.1. The zinc coating may be either hot dip galvanizing per ASTM A153
Class C or mechanical plating per ASTM B695 Class 50, except with minimum coating weights as per Paragraph 4.4.6 of ASTM A394.
Suitable nuts for Type 1 bolts are Grade DH per ASTM A563 with zinc coating specified. Nuts are to be coated together with the bolts by the same process. After coating, nuts shall be tapped oversize per Table 5. ASTM A563 allows specifying a dry film lubricant when ordering nuts.
Suitable flat washers are zinc-coated Type 1 hardened steel per ASTM F436. Split ring lock washers are ~obsolete (proper bolt pre-loading is preferred); you may wish to use load indicating washers per ASTM F959, 'Standard Specification for Compressible-Washer-Type Direct Tension Indicators for Use with Structural Fasteners.' These can be ordered with mechanically plated zinc per ASTM B695, Class 50.
- Goleta, California

Rest in peace, Ken. Thank you for your hard work which the finishing world, and we at finishing.com, continue to benefit from.
Thanks Jeffrey, that sounds like a great idea.
Thanks Ken -- what an extraordinarily great posting. We've missed you lately, friend!
Regards,
Ted Mooney, P.E.
Striving to live Aloha
(Ted can offer longterm or instant help)
finishing.com - Pine Beach, New Jersey
A. Dear sir,
I noticed your post from August and wondered how you are doing with your search. We have just finalized a process that is now being used by Centerpoint Energy in Houston. We coated thousands of fasteners for them over the past weeks as Houston rebuilt.
I would love to tell you more, as this process has been tested for over 5 years.
- Lynden, Washington
Hi, Robert. Please give us ASTM or ANSI specs for the finish you're speaking of, or describe it in generic terms: Zinc based or a different cathodically protective metal; applied by plating, PVD, hot-dipping, dip-spin, metal spray; organic or inorganic; typical thickness; etc. Or advertise it here or elsewhere. Thanks! Regards,
Private matchmaking and comment spam may seem fine for the vendor and the potential customer at the time, but it has proven to be the kiss of death to countless public forums. Apologies :-)
Ted Mooney, P.E.
Striving to live Aloha
(Ted can offer longterm or instant help)
finishing.com - Pine Beach, New Jersey

Q, A, or Comment on THIS thread -or- Start a NEW Thread