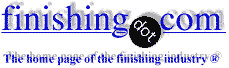
-----
Anodizing Racks: Titanium vs. Aluminum
Current question and answers:
Q. We are new to the anodizing process, and we need to build some rack for the first prototype run.
We are thinking about using titanium racks in the long term, but for the prototype run we want to use aluminum racks.
We have asked the chemistry supplier which alloy is to be used, but we did not get clear answer, they say 5000 or 6000 series.
But is there a aluminum alloy that is preferred to use?
- Vildbjerg Denamrk
March 9, 2021
A. Hi Poul, 2024 is the best material but the racks can be made out of the same material as you are anodizing. They must not rob the current by being of a material that anodizes at lower voltage than the parts. A 6000 series aluminum is "uh, okay", especially for a short-lived prototyping experiment as long as you are not anodizing 2000 series aluminum. Obviously, titanium is a better idea though.
But since you say you are new to the process and just starting, I should note that most shops don't build their own racks. They usually buy them from suppliers familiar with the needs of anodizing racks. Sometimes for small parts you can purchase a 'standard' titanium rack and save the expense of custom design.
Luck & Regards,
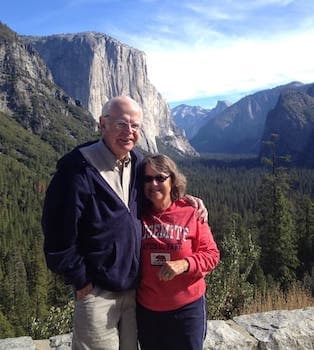
Ted Mooney, P.E. RET
Striving to live Aloha
(Ted can offer longterm or instant help)
finishing.com - Pine Beach, New Jersey
March 2021
⇩ Related postings, oldest first ⇩
Q. We send out one of our components for anodizing & bright dip finish. This component is round and quite thin (.014"). We have found through experience that we must supply a ring to put around part of the OD of the component to keep it from becoming distorted by the pressure of the racking device. The problem is that we make the ring out of aluminum and after about 3 or 4 uses the ID of the rings become too large and are no longer useable and must be replaced.
The question is: Can these rings be made out of some other material that would not be affected by the anodize process (they must also be able to withstand the heat of the process)?
Thanks for any input.
Stan Kmiecik- Addison, Illinois, USA
2000
A. Many of our anodize racks are made out of titanium.
Titanium conducts the electricity to the part which is necessary but the titanium does not anodize, like an aluminum rack would, and thus you don't have to strip it in between uses ... it lasts forever.
David A. Kraft- Long Island City, New York
A. For anodise jigging you are limited to aluminium or titanium if you are going to use metal or a non-conductive material that will withstand acid and heat.
Titanium would be best (also costs a lot).
Other options to try which may or may not work:
Thick (0.75 inch) polypropylene
Etch prime / prime the aluminium rings (try some old ones to allow for the paint thickness - also use up your waste).
Ask your finisher if the rack can be redesigned.
Redesign the part with a tag to hold when finishing which can be removed after.
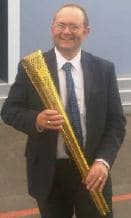
Martin Trigg-Hogarth
surface treatment shop - Stroud, Glos, England
A. Although it's expensive, I would recommend Titanium, as it won't have to be stripped after coating, like your Al rings.
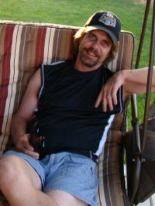
Marc Green
anodizer - Boise, Idaho
A. Are you using 2024 aluminum, which is the best alloy for this purpose? If so, and it's still not good enough, try titanium.
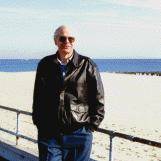
Ted Mooney, P.E.
Striving to live Aloha
(Ted can offer longterm or instant help)
finishing.com - Pine Beach, New Jersey
![]() |
Ted, Please take a minute to explain what the advantages of using 2024 Al would be? I'm just curious. Thanks, ![]() Marc Green anodizer - Boise, Idaho Quoting from AESF's Intensive Training Course: "2024 alloy ... requires the highest voltage to produce the desired current density but forms the thinnest film." For these reasons it steals the least current, is most easily stripped because of its thinness, and lasts the longest because the amount that has to be stripped on each cycle is the least. ![]() Ted Mooney, P.E. Striving to live Aloha (Ted can offer longterm or instant help) finishing.com - Pine Beach, New Jersey |
Multiple threads merged: please forgive chronology errors and repetition 🙂
Q. In the anodizing industry, some people are using titanium racks and some are using aluminum racks. Why? What is the main difference? On the surface, Ti racks cost more, (5-9x) but last a lot longer. Aluminum racks have to be stripped after each use.
How do anodizers decide which kind of rack to use?
supplier - San Diego, California
2007
2007
A. Your analysis of the situation is a good start, Ken. One situation which would favor aluminum racks is when they don't actually need to be stripped. For example, for architectural extrusions the parts can sometimes be attached to the racks with aluminum sheet metal screws which go into tapped holes in the rack. The current is conducted from the rack, through the screws, to the parts -- so anodizing can build up on the rack without causing a problem. And because the tapped holes in the rack have a screw in them, they don't anodize. Of course, sometimes the anodizing on the rack won't survive the pretreatment (especially if etching is involved).
Both aluminum and titanium are widely used because neither is superior for all situations.
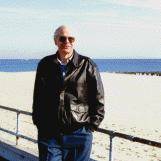
Ted Mooney, P.E.
Striving to live Aloha
(Ted can offer longterm or instant help)
finishing.com - Pine Beach, New Jersey
A. Jigs: the best results are always obtained using alloy jigs. Titanium by its nature is hard, leaving marks against work pieces, and does not pass current well.
humphrey sylvanus-peekanodizing - fleet hants uk
July 17, 2014
Must rack area be considered in calculating anodizing current?
April 12, 2014Q. I'm so happy I found threads like this.
I'm new to anodizing and I'm using an LCD (low current density anodizing) kit from a hobby plating supplier.
Regarding Paul's post on letter 30512 (which is very helpful), he mentioned something about surface area related to racking as follows:
"This assumes no voltage drops due to bad connections, and you haven't increased the actual surface area with racking."
My question here is does the racking area affect the calculation?
If the answer is yes, does this change with the material type of rack titanium/aluminum.
Thanks again for all this great information.
- Cairo , Egypt
A. With aluminum racking, yes, you have to account for the additional surface area of the rack. With titanium racking, you do not.
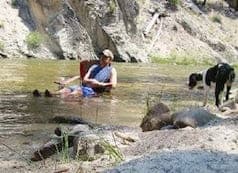
Marc Green
anodizer - Boise, Idaho
July 20, 2014
Why Not Copper Racks for Anodizing?
Q. Do you think copper jigs are fit for anodising and electrocolouring as they are very good conductors of electricity? Why are people are not using copper as material for jigs?
Sachin JindalJindal exports - Mandi gobindgarh, India
October 13, 2017
![]() |
October 15, 2017 Hi Jindal ![]() Geoff Smith Hampshire, England October 15, 2017 A. Because copper and sulfuric acid anodizing are not very compatible. The copper rack, or rack tips, would burn and dissolve into the anodizing solution once the current is applied to the work. ![]() Marc Green anodizer - Boise, Idaho |
Q. Will my 6061 part burn if I rack it using 7075 bolts?
Klay HoughAnodizer - Tucson, Arizona, U.S.A.
April 3, 2019
A. Hi Klay. The ideal material of construction is 2024 Aluminum because it requires the highest voltage and builds the thinnest film. But I would expect 7075 aluminum to be okay when the parts are 6061.
Regards,
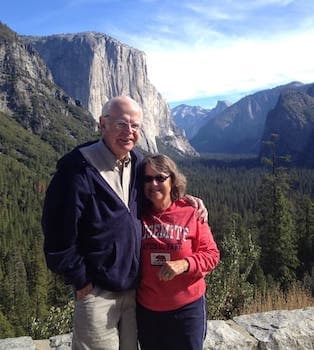
Ted Mooney, P.E. RET
Striving to live Aloha
(Ted can offer longterm or instant help)
finishing.com - Pine Beach, New Jersey
June 2019
Q. Hi, We are looking for jigs 1050 grade aluminium products. The problem with an aluminium jig is that it gets anodised & stops conducting current. The issue with titanium is that it is too hard & leaves marks on the product at the point of contact (1050 being a very soft grade). Please suggest suitable option.
SAMRAT CHANANAMANUFACTURER - Haryana, INDIA
September 26, 2019
September 27, 2019
A. Hello Samrat,
Aluminium jigs are fine as long as you wire brush the points of contact with the components before jigging.
They will get thinner with time, from repeated anodising, so you will need to replace them periodically.
If the titanium is leaving marks then that rules it out.
One other point I will make is, try not to mix alloys in the tank, as they all have different electrical conductivities. So that when anodising you can not be sure that you have the current density range on the components that you think you have. This being important to ensure consistent anodic films. This applies to the jigs as well.
Best regards
- an unseasonably warm rock in the irish sea
Q, A, or Comment on THIS thread -or- Start a NEW Thread