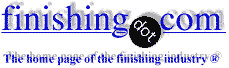
-----
7075-T6 Chromate Conversion
We are processing 7075-t6 impacted parts. On the machied surface we are seeing a growth. White spots will appear after cleaning. THese areas can be wiped off only to leave a very dark spot on the part. We have tried 3 different cleaners. Alkaline NON Etch, Alkaline Etch, and a solvent based cleaner. We are still seeing this problem. The parts are all from the same batch and heat lot, but one part may run fine while the next exibits the measels. any thoughts
Robert DavisJob SHop - Texarkana, Texas
2007
First of three simultaneous responses --
When 7075 is very old and/or when 7075 has been heated, the zinc goes to the grain boundaries, then when you anodize the zinc plates away and leaves a pit. There is nothing can can do about the particular batch of 7075 your client is using. In the case of the zinc laying just under the surface, which surface has been completely converted to aluminum oxide, then you may save a few pits by ramping up slower.
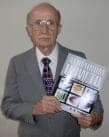
Robert H Probert
Robert H Probert Technical Services

Garner, North Carolina
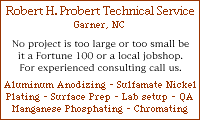
2007
Second of three simultaneous responses --
Alkalinity brings out the worst in 7075. It removes aluminum and leaves a surface enriched in Cu, Fe, Mg, Zn, etc. Acid etch if necessary, use a nitric acid-based deox/desmut and rinse in DI water. See also letter 45714.
Ken Vlach [deceased]- Goleta, California

Rest in peace, Ken. Thank you for your hard work which the finishing world, and we at finishing.com, continue to benefit from.
2007
Third of three simultaneous responses --
You do not say anything about a smut remover or a deoxidizer. What do you use?
James Watts- Navarre, Florida
2007
2007
Our process is as follows:
Clean
Rinse
Rinse
Deox
Rinse
Chromate Conversion
Rinse
Rinse
THe cleaner is heated to 160 degrees. Also the Deox is a Proprietary blend of nitric and sulfuric acid. When viewed under magnification. The parts almost appear to have craters in the metal.
Commercial Manufacturing Company - Texarkana, Texas
Q, A, or Comment on THIS thread -or- Start a NEW Thread