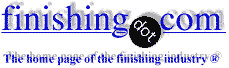
-----
Hard chrome plating thickness required for different applications?
Q. We are having brown spots show up on the outside of our parts after a thin dense chrome is applied (.0002" - .0003" thick). The parts are glass bead using GB10 before the coating is done. Base material is 17-4PH H900 condition.
I'm looking for ideas on what to investigate and if anyone else has come across a similar issue.
Jim Hoff- Pittsburgh, Pennsylvania
February 11, 2022
A. Hi Jim. Colors can be deceptive in photos, but it looks to me like the chrome is chipped off in that area. Is it possible to get a more detailed close-up view, or some other way to know if the chrome is missing there?
The glass bead blasting is the only prep (no cleaning or activation)? Do you send the parts out for plating or do it in house?
Luck & Regards,
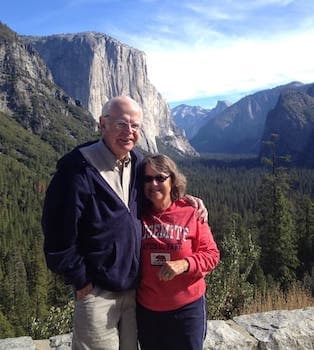
Ted Mooney, P.E. RET
Striving to live Aloha
(Ted can offer longterm or instant help)
finishing.com - Pine Beach, New Jersey
Q. We glass bead the parts with GB13 then wash in a Mirachem solution prior to send out to a vendor in the Midwest. Here are more photos.
What is odd is that when our vendor glass beads the parts, these discolorations do not appear.
Two items we are working on -
- Verify our GB media does not have any contaminants
- Citric passivate after GB operation then send to vendor
- Pittsburgh, Pennsylvania
A. Hi again. The issue of course is that the problem might be on your end or it might be on the plater's end. The plating shop surely has to re-clean and activate the parts after their travels by truck, and we have no information at all about what they are doing for inspection, cleaning, activation, etching, plating, and re-inspection.
Based only on the pictures I continue to believe that the plating is chipped/flaked away. The hints that lead me to think that are the color and the shape. Shapes which have something to do with wet processing will generally have somewhat rounded shapes because liquids have surface tension. Due to surface tension & viscosity, drips and stains don't have sharp knife-edge points like this defect. Chips and flakes may have sharp edges.
0.0002" to 0.003" might be enough just to catch a fingernail on, or a close-up photo at 90° to this photo might verify the absence of plating.
Luck & Regards,
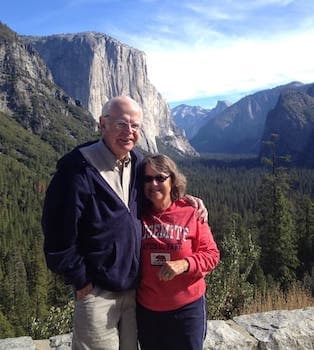
Ted Mooney, P.E. RET
Striving to live Aloha
(Ted can offer longterm or instant help)
finishing.com - Pine Beach, New Jersey
Q. Can anyone tell me the specs on the hard chrome thickness for a standard Waukesha H24GL crankshaft "natural gas engine"
Moony Anaru- Fort Collins, Colorado
July 13, 2024
A. Hi.
A. Manufacturers rarely release such info, but it should be possible to find an unworn spot on the crankshaft and measure the thickness.
Luck & Regards,
Ted Mooney, P.E. RET
Striving to live Aloha
(Ted can offer longterm or instant help)
finishing.com - Pine Beach, New Jersey
⇩ Related postings, oldest first ⇩
Q. Hello,
I would like to understand why someone would specify a flash chrome vs. thick plated chrome. Does thicker chrome improve life vs a flash chrome and is their a point of diminishing return as you get thicker. I would also like to understand the relationship of hardness to wear resistance as it pertains between thin dense chrome and hard chrome. I realize that thin dense chrome is harder than hard chrome but has a much thinner coating.
How does this relate to my problem. I compression mold PTFE. We are looking at fabricating new dies and I think my old drawings have an over-specified chrome thickness. We are specifying 0.006 to 0.01 inches thick on each side. What am I sacrificing if I decrease my chrome thickness to 0.001 to 0.0015 inches thick on each side of hard chrome or would thin dense chrome possible be a better alternative.
Things to consider in my process. We pull our billet out of our mold so lubricity is important. Corrosion would be problematic - so if I chipped our dented the chrome. It would create brown spots in my final product. Depending on how well my supplier cleans their PTFE I can have trace amounts of HF which results in pitting of my dies.
Thanks for your help
customer/engineer - Hoosick Falls, New York
2007
A. Hi, Michael. "Flash" just means a very thin or very quick coating and has no real quantitative meaning. Thin Dense Chrome is a trade name for a proprietary; some experts think quite highly of it while others are less impressed. You should talk to the purveyors and ask what the quantitative differences are, then talk to the doubters and decide for yourself how significant the technology is for your particular needs.
While the thickness of chrome has some effect on its corrosion resistance, the reason you specify a particular thickness usually doesn't have much to do with corrosion resistance but with wear life and providing enough thickness to develop hardness on the substrate in question if necessary. On a very hard substrate, a couple of ten thousandths of an inch may provide good wear resistance; but on a soft substrate you may need several thousandths before you have anything truly useable. If your molds are copper for example, your 0.006 to 0.01 inch is probably not excessive. But if they are hard steel (which I suppose they are because you worry about rust), I suspect that the 0.001 to 0.0015 might well do it.
Hopefully we'll hear from an experienced mold plater. Good luck.
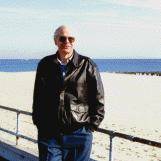
Ted Mooney, P.E.
Striving to live Aloha
(Ted can offer longterm or instant help)
finishing.com - Pine Beach, New Jersey
2007
A. I also think your specified thickness is excessive. Some tool designers tend to think that a thicker coating is better, but this is not always right. Besides what Ted pointed out, there's another issue with heavy electroplated coatings when applied to molds or tools: profile distortion. Thin dense chrome, due to its very low thickness, would not appreciably alter critical dimensions while conventional thick chrome will, thus requiring risky, expensive, and tedious post-grind or manual bench work to keep tolerances, eliminate negatives, sharp edges, etc. Now, if your resins are not blended with abrasive particles I think you should also consider high phos electroless nickel. More uniform, highly resistant to corrosion & fluorides and hard enough.
Guillermo MarrufoMonterrey, NL, Mexico
2007
Q, A, or Comment on THIS thread -or- Start a NEW Thread