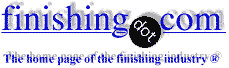
-----
Demineralization (Water Treatment) Problems
DMF = dual media filter
SAC = strong acid cation
DGT = diffusive gradients in thin film?
SBA = strong base anion
MB = mixed bed
OBR = output between regenerations
Q. In our Dm plant having DMF, SAC, DGT, SBA and MB plant OBR is 140 m3/hr, but we are getting 90 m3/hr due to SBA conductivity raising fast. At the same time MB also increases. Our SBA pH is 6 to 7 is maintaining, and conductivity is 1.0 microsiemens per cm.
What is the issue? We are not getting full OBR. Maybe degasser tower having the or SBA resin life is 4 months (new resin) SAC and MB resin is one and half year life only. But we have OBR issue. Can you please suggest what is the reason behind this? If this data is not enough, I will share more with you.
Thanks
Ravi babu
Operation - Salem
November 19, 2022
⇩ Related postings, oldest first ⇩
Q. I have a problem with a demineralization system. The conductivity of our pure water increase almost 6 times its value. We have tried to recycle the process several times, but the conductivity still higher. Other than regenerated the anion and cation exchanger, we can not find the problem.
My question is:
Do you think that CO2 can be also the problem or what else you recommend me to look for?
Lorena Ramos
Tampa, Florida
2000
A. DI tanks start out at 8-12 meg ohm for tanks that platers use, up to 18 MOhm for lab use.
With use, they rapidly lose their ability to give that quality. As they get to loser and lower quality, the rate of decrease in quality slows down. This is just the nature of the beast.
If you think that you have a CO2 problem, take a reading on a beaker full and boil it for 5 minutes. Cover it and let it cool to original temp. If you have a CO2 problem, you will have better quality water when you take the second readings as you have eliminated the ion.
James Watts
- Navarre, Florida
A. What is the inlet/outlet conductivity of your water?
Is it possible your demineralizer is mechanically malfunctioning? Valves, flappers or chemical delivery system may not be working. Are you drawing the proper volume of chemicals during regen?
How old is your resin? The Anion could become organically fouled or silica fouled over time and may need to be cleaned or replaced.
If the pH of the water is down around 4 you may be seeing CO2 leakage. If it is above 8 you may be seeing Sodium leakage.
John Ring
- Whaton, Illinois, USA
A. Please check your degasifier equipment. If you don't have a degasifier then please to purchase one and fit it at the end after the anion exchanger.This would solve your problem of CO2. Then even if the problem persists use the modern resin conductivity sensor which gives you an output in digital format based on the resin exchange capability and the conductivity of the water.
Please respond about my suggestion.
Atmakury Harish
- Hyderabad, A,P, INDIA
2005
Q. I would like to know the average, minimum and maximum service life of an ion exchanger resin (in general).
What's the frequency in replacing the resin? Annually?
How would you evaluate a resin if it's still functional or not by just merely looking at it? Or is it possible?
Dax Bracero
- Philippines
2002
A. If your influent is normal quality water, resin may function efficiently +15 years. However, the life of resin depends upon many factors, oxidizing agents in influent may cause very short life.
You don't need to replace the resin if it is functioning properly. You may need to add some quantity if the resin is lost during backwash.
Mazhar Shah
- Karachi, Sindh, Pakistan
2005
Q. Is there any effect if I put degassifier before and after the anion exchanger?
I often see some article that they put degassifier between cation exchanger and anion exchanger. Because degasifier can reduce anion exchanger load to exchange the anion content in the water.
I wish some suggestion for this question.
Thank you.
Lelywaty
- Indonesia
September 24, 2008
Q. Sir, ours is a dm plant of 600 m3/hr capacity with 6 streams (cation, anion, mb).
Recently we faced a problem in one of our anion exchangers, i.e., after regeneration silica is not coming down, whereas pH and conductivity are normal (8.5 & 20 micro mho/cm)
Our CO2 inlet to anion exchanger is 17ppm. sodium from cation exchanger is 0.9 ppm?
What could be the reason?
azhagarasan veeraiyan
employee - India
April 29, 2009
Q. Recently While I have change my input feed to DM Plant I am facing issue of high turbidity, reddish brown water from Heat Recovery Steam Generator (300 °C, 16 kg/cm2).
My DM plant is designed with High Pressure Sand Filter, SBA, SAC and MB.
Input feed parameter are
Parameter Inlet Feed
pH 6.8-7.5
Turbidity <10 NTU
M.O Alkalinity as CaCO3 mg/l 80 mg/l
Total Cation/Anion as CaCO3 150 mg/l
(Na + K) as CaCO3 60 mg/l
Calcium hardness as CaCO3 60 mg/l
Total hardness as CaCO3 90 mg/l
Chlorides as Cl 25 mg/l
Sulphates as SO4 35 mg/l
Reactive silica as SiO2 45 mg/l
Colloidal silica as SiO2 Nil mg/l
Total iron + Mn 03-.05 mg/l
Total dissolved solids 150 mg/l
Other heavy metals <0.1 mg/l
Output DM water parameters like pH, Conductivity, silica are same as for previous source.
Kindly suggest the probable cause and/or specific parameters to be checked in system.
Sugat Mittal
- DIGBOI, Assam India
October 3, 2019
----
Folks: This isn't a consulting service, but a mutual-help public forum! Please try to comment on one of the open questions before posting your own question lest the thread devolve into just a long list of unanswered questions :-)
MB outlet water total residues is very high 15 and conductivity in 0.3
Q. MB outlet water total residues is very high 15 and conductivity is 0.3
Total residues value less than 0.4
Please help.
damodharan thangamani
- Sankarapuram, India
March 17, 2020
? Hi Damodharan. I haven't heard that phrase "total residues". Is it the same thing as TDS/total dissolved solids? What are the units? What do you mean the "value" is less than 0.4? Is 0,.4 your target? What are the units of your conductivity, micro mho/cm?
Regards,
Ted Mooney, P.E. RET
Striving to live Aloha
(Ted can offer longterm or instant help)
finishing.com - Pine Beach, New Jersey
Q, A, or Comment on THIS thread -or- Start a NEW Thread