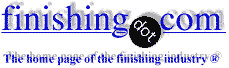
-----
Pressure Vessel Jacket - Degreasing rinse water won't come clean
2007
Hi Folks,
We have encountered a problem during the degreasing of a new vessel jacket internals, using a 10% caustic solution. The vessel is of 316L and the degreasing took place over an hour at 70 degC. Following 6 or
7 water rinses, the pH and conductivity remain stubbornly high at 12 and 9000 micro Siemens respectively (these would usually approach normal levels after just 2 - 3 rinses). The rinse water also has a slightly yellow tinge to it. Our (very experienced) Passivation Engineer has never come across this and has gone home to think about it! Does anyone have any ideas? Things that come to mind are:
* We have EPDM gaskets & seals. However shouldn't these be ok in a 10% caustic solution? In addition, the chemical should be long gone after 6-7 rinses.
* If the vessel vendor had applied pickling paste to the internal welds, would this explain the high pH of 12 that we're continually getting in the return water?
Are there any other factory-applied surface or weld treatments (or contaminants) that would cause the symptoms described above?
Thanks for your help in advance.
Project Engineer - Pharmaceuticals - Cork, Ireland
2007
My guess is that in addition to the main passageways, you have side passageways or pockets that are retaining your caustic solution. pH of 12 would be a bit high, but your original solution was over 14.
You might try rinsing it with a dilute citric acid
⇦ on
eBay
or
Amazon [affil link] solution and then with DI and see what happens.
I think that if you analyze some of the "yellow" solution that you will find it to be dilute rust or ferrous chloride.
- Navarre, Florida
I agree with James.
This is due to the caustic soda ⇦liquid caustic soda in bulk on
Amazon [affil link]
strongly adsorbed at the surface. Then, the solution is used a super-light acid concentration (mild acid) in order to get rid of the caustic soda (during less than 1 min). Rinse it with Hot Water. And effectively, after 3 rinses you will get your claimed requirements.
- Minneapolis, Minnesota, USA
2007
Q, A, or Comment on THIS thread -or- Start a NEW Thread