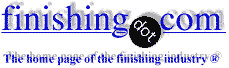
-----
Touching up anodizing with Alodine/Iridite/Chem-film/Chromate

for Shops, Specifiers & Engineers
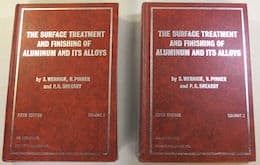
avail from eBay, AbeBooks, or Amazon
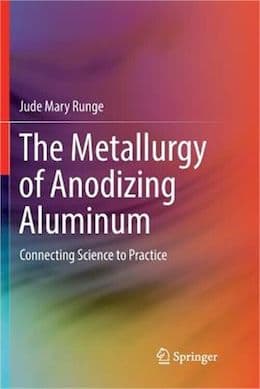
avail from eBay, AbeBooks, or Amazon
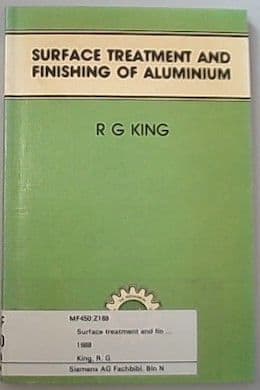
avail from eBay, AbeBooks, or Amazon
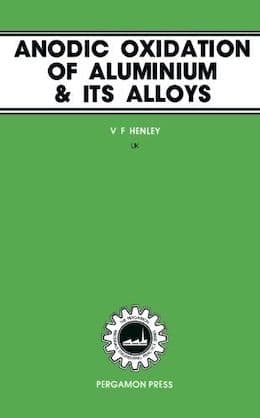
avail from eBay, AbeBooks, or Amazon
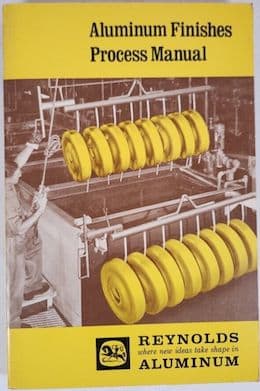
avail from eBay or Amazon
(as an Amazon Associate & eBay Partner, we earn from qualifying purchases)
Q. I'm a chemical engineer, we are building some large aluminum tanks that are welded in sections. The bulk material is anodized aluminum, the area around the welds are bare. These will need to be CCC'd. We intend to mask, but if there is some small amount of overlap between the newly applied CCC and the anodize, will this be deleterious to the anodize finish? Mostly concerned from a corrosion control perspective, but any negative affects are concerning. I know MIL-A-8625 / MIL-PRF-8625 [⇦ this spec on DLA] allows CCC to touch-up anodize, so some overlap has to be OK. Also, it seems the chemical reaction in a CCC process is with Aluminum, so I would expect an aluminum oxide coating would be less reactive?
Daniel Ricciardo- Piscataway, New Jersey
December 8, 2021
Q. Hi Daniel,
Did you obtain the information to answer your question?
We are facing a similar problem where we need to treat 5000 series aluminium with hexavalent chromium (Alodine 1201
⇦ on
eBay
or
Amazon [affil link] ). The aluminium has spot corrosion from mechanical abrasion scattered in anodised aluminium in very good condition.
We posed this question to Henkel several times during a 4 week period with no response.
- Florida
April 3, 2023
A. Hello Daniel and JC
Alodine/Iridite etc. is acidic in nature and it works at a pH of 1.7-2.0, which is below the recommended pH for anodizing, however, it is also a conversion coating for aluminium, and we have masked parts in the past, etched them and then treated them with yellow alodine on the entire surface, anodized and raw substrate alike. It'll usually leave a matt finish, but having measured the layer thickness as well as done an abrasion test with glass paper, it hasn't shown to be degraded, of course, if you expose the part to yellow alodine for a significant amount of time and do not rinse it off properly afterwards, you might get yourself into trouble. However, I am a little worried that you are mentioning tanks? It would also depend what these tanks need to contain? Hopefully nothing that comes into contact with foodstuff or medical liquids, as Alodine contains Cr+6 and causes cancer.
As such, please, for your own sake, remember you PPE and make sure the area is ventilated -away- from you.
- Horsens, Denmark
April 5, 2023
Q. Thanks M.S for providing your test results.
Our application is 5000 series aluminium installed outdoors and subject to sea spray.
We need to mechanically remove aluminium oxide pitting - what material composition of burr/bit should be used to avoid contaminating the aluminium from:
1) future corrosion via deposition of burr contaminants (e.g. iron, chlorine etc) deep into the surface
2) burr contaminants interfering with the etching and chromate conversion?
- Florida
April 24, 2023
Depending on the size of the spot you are intended to grind, small Dremel
⇦ on
eBay or
Amazon [affil link] bits are effective. Usually we'd use a small flap-rotary bit (Similar to a flap-disc used for cleaning up welds etc.), or if we really need to get into the material, a High Speed Steel (HSS) bit with a follow up with the flap-rotary bit, would do the trick. Of course, if it needs to look nice as well, you can go from there and all the way to a fine polish, using a more fine grit size until you use a small polishing bit with a fine polishing compound.
A. Though, regardless of the intensity of the repair, always clean everything off with alcohol or a degreaser, this will help remove residue like the fine powder you'd get from a very fine grind, the type that turns your fingers grey! As well as helping in picking up larger "chips".
By following up with the flap style tools, you help ensure that you don't have a rogue piece of metal stuck into the aluminium.
As always, when working with grinding tools. Wear ear protection, protective glasses, slim-fit sleeves (the ugliness of getting your sleeve pulled into a grinder is not recommendable) and a dust-mask, as well as any PPE your safety organizations recommend.
- Horsens, Denmark
April 27, 2023
⇩ Related postings, oldest first ⇩
(to provide context, hopefully helping readers more quickly understand the Q&A's)
Anodizing is an electrochemical process which is performed on aluminum for many purposes including corrosion resistance, hardness, wear resistance, electrical insulation, so that it can be easily dyed for appearance, and other reasons. Please see our FAQ "Intro to Anodizing".
Anodizing can leave small areas under contact clamps, etc. with no or improper anodizing or dyeing, and it is usually impractical to 'spot anodize' those areas to correct the issue. Therefore, many anodizing specifications, including MIL-PRF-8625, will allow a certain amount of 'touch up' of those and similar areas with a chromate conversion coating. "Alodine" and "Iridite" are trade names of product lines of chromate conversion coating chemistry, and "Chem-film" is a synonym sometimes used in the USA. You can search the site for numerous threads about "chromate conversion coatings for aluminum" and "aluminum anodizing".
Q. I am looking for a simple touch-up Material, Process, etc., compatible with the black anodize per Mil-A-8625, Type III, Class 2, Dyed Black.
Boris BayevskyMechanical Engineer (Not finishing industry) - Tallahassee, Florida, USA
2007
A. MIL-A-8625
[⇦ this spec on DLA] F allows touch-up with Alodine.
"3.3.4 Touch UP (mechanical damage and contact marks). Unless otherwise specified (see 6.2), mechanically damaged areas from which the anodic coating has been removed without damage to the part may be touched up using chemical conversion materials approved on QPL-81706 for Class 1A coatings and the applicable method of application. Touch up shall apply only to inadvertent mechanical damage such as scratch marks. For Type III coatings, touch UP shall only be allowed in areas which will not be subjected to abrasion (see 6.1.1). The mechanically damaged area(s) shall not exceed 5 percent of the total anodized area of the item or touch up shall not be permitted. When specified in the contract or purchase order (see 6.2), contact marks shall be touched up using the above method required for mechanical damage."
- Seattle, Washington
A. Christopher is right for specification requirement. Check with your customer to see if this will be acceptable as to any appearance issues. I had second-tier anodizer (aerospace) ship parts where pits on black anodize filled in with black felt-tip marker. I was "not happy".
Douglas Hahnaerospace - Saint Charles, Missouri
Looking for some way to touch-up Olive Drab Green Anodize?
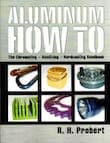
Aluminum How-To
"Chromating - Anodizing - Hardcoating"
by Robert Probert
Also available in Spanish
You'll love this book. Finishing.com has sold almost a thousand copies without a single return request :-)
Q. I need to find a way to touch up Anodized Aluminum parts with a Olive Drab Green Colored finish. MIL-A-8625 [⇦ this spec on DLA] Type II or III, Class 2 dyed Olive Drab? Is there a technique or a way without stripping and re-anodizing?
James BlackProduct Designer - La Mirada, California, USA
2007
![]() |
A. You can use chromating solutions on bare surfaces and if you add NaF in the solution you can better activity on the surface Shapour Abd Sharif Abadi- Tehran, Iran A. Good luck finding one! Actually the timing of this inquiry is quite interesting as I have on my desk a Winsor & Newton olive green acrylic paint, a Zig "Painty" paint maker in guacamole color and a fine point olive Sharpie marker for this very purpose. All resulted in some degree of mismatch that neither myself or our customer (or their customer: US Army) would buy off. My suggestion would be go to a good art store, where the art students shop, and purchase a myriad of marker, inks, paints and such. Again, there is no magic pen BUT if you come up with one, please let me know. My firm and the US Army would greatly appreciate it! ![]() Milt Stevenson, Jr. Plating shop technical manager - Syracuse, New York |
Multiple threads merged: please forgive chronology errors and repetition 🙂
Is touch-up allowed in Mil-A-8625?
Q. Does the mil-spec allow "touch-up" rack marks, scratches, Masking mistakes with paint?
BUYER - Lancaster, Pennsylvania, USA
September 29, 2010
A. Yes, unless otherwise specified. MIL-A-8625 [⇦ this spec on DLA] F states that,
SK Cheah
- Penang, Malaysia
October 18, 2010
Multiple threads merged: please forgive chronology errors and repetition 🙂
Conversion Coating Allowed For Rework of Anodized Parts?
Q. Hello. I am a Quality Engineer for an aerospace company and much of our product base consists of aluminum alloy components that are Sulfuric anodized per Mil-A-8625. The question has just been raised about the acceptability of applying a chemical conversion coating (such as Alodine 1201
⇦ on
eBay
or
Amazon [affil link] or 1132) following rework of an anodized part. For example, if we have an anodized component at Rev B that is subsequently reworked to a new Rev C (we'll assume that a chamfer is added along an edge), is it permissible per Mil-A-8625 to apply a conversion coating to the newly machined surface? Mil-8625, paragraph 3.3.4, says in part "Touch up shall apply only to inadvertent mechanical damage such as scratch marks". Our rework certainly does not fall into the category of "inadvertent damage", and thus the reason for our question. Should this statement be taken at true face value, is there some general industry practice, or is my interpretation of this statement incorrect or too strictly interpreted?
Thanks to all for your input.
Mike
Sr. Quality Engineer - Goldsboro, North Carolina
June 6, 2014
A. Hi Mike,
To me your interpretation is correct, but there is nothing to stop you having some sort of repair/update drawing that could show machining where required followed by chromate conversion coating in accordance with MIL-DTL-5541.
If these are your company design authority you have the right to do what you wish, if you are not the design authority then you need to ask the design authority for permission to carry out the operation.
Aerospace - Yeovil, Somerset, UK
June 11, 2014
Hi Brian. Thanks for the feedback. We are the design authority for these parts and I suppose that we could address this practice procedurally, without a need to revise the actual part drawings. Perhaps that is the course to take. We have just always used the CCC on minor rework areas, avoiding the need to strip and re-anodize. Then the question was posed, and we started scratching our heads, realizing that our practice didn't appear to be fully compliant with the wording of the spec.
Thanks,
Mike
Sr. Quality Engineer - Goldsboro, North Carolina
Q. I found the same reference in MIL-A-8625 [⇦ this spec on DLA] to use Alodine as touch-up for hard anodize. The issue, of course, is appearance. Is there any reason why it would not be acceptable to use black paint or even marker over the alodine touch-up to make the appearance more uniform?
Yossi DavidRugged computers - Herzliya, Israel
November 6, 2018
Q. can type IIB class 2 anodize be touched up with Alodine? If so, what document would allow it? Anodized per MIL-A-8625.
Fouzi Diab- Fort Collins, Colorado USA
January 20, 2020
A. Hi Fouzi. As you can see from the thread we added your inquiry to, yes, touch-up is allowed under the terms listed in section 3.3.4 of MIL-A-8625 [⇦ this spec on DLA] itself.
Regards,
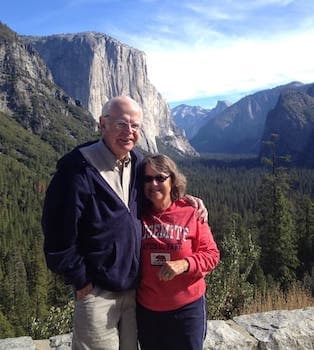
Ted Mooney, P.E. RET
Striving to live Aloha
(Ted can offer longterm or instant help)
finishing.com - Pine Beach, New Jersey
January 2020
Q. Fouzi, I have the same question about Type II. I see that 3.3.4 talks about Type I & III, but not II. Did you find any additional information?
Ryan- Lincoln [Nebraska]
August 18, 2021
Tip: This forum was created to help build camaraderie through sharing tips, opinions, pics & personalities.
The operator & those readers who want that might not engage with anonymous posters.
A. Hi Ryan.
I don't read that section of that document as applying only to Type I & III.
Luck & Regards,
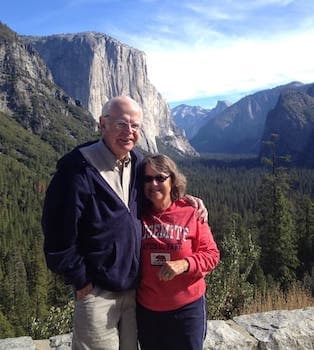
Ted Mooney, P.E. RET
Striving to live Aloha
(Ted can offer longterm or instant help)
finishing.com - Pine Beach, New Jersey
Q. Can Anodized parts be touched up? If so is it the same process as chem film?
Richard De Los Reyes- Felton California
May 16, 2021
A. Hi Richard. Yes, please see the earlier entries on this thread.
Luck & Regards,
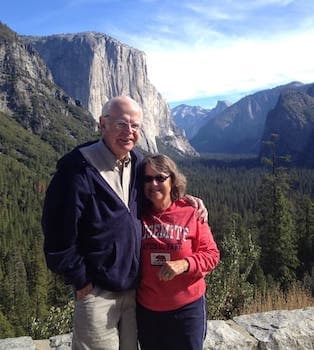
Ted Mooney, P.E. RET
Striving to live Aloha
(Ted can offer longterm or instant help)
finishing.com - Pine Beach, New Jersey
WANTED TO GIVE A HEADS UP THAT AS OF NOV. 23, 2020 MIL-A-8625
[⇦ this spec on DLA] HAS BEEN CHANGED TO MIL-A-8625 / MIL-PRF-8625
[⇦ this spec on DLA].
supervisor - Cicero, Illinois
Saporito Finishing Co.

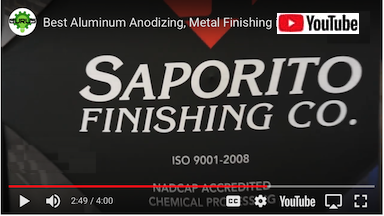
August 14, 2021
Q, A, or Comment on THIS thread -or- Start a NEW Thread