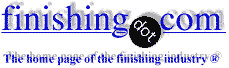
-----
Rust removal from firetube boilers with zero loss of good metal
2007
I own a textile processing industry which undertakes dyeing, printing and finishing of woven fabrics. I have a couple of used 1996 fire-tube Babcock Omnical boilers, which I bought early last year. One of them is a 12 tons per hour steam generating boiler and the other one is a 6 tons per hour boiler. They both are accompanied by economizers and have a working pressure of 10 bars. I am faced with a dilemma these days concerning these boilers. The backdrop of this confusion will emerge as we proceed further.
Following are the details of the boilers and economizers:
- 12 tons per hour boiler
- Total shell diameter (10 feet)
Total shell length (20 feet)
Burner furnace tube diameter (4.6 feet)
Burner furnace tube length (18 feet)
81 tubes (3 inches inner diameter, 0.13 inches tube thickness and 18 feet tube length)
68 tubes (2 inches inner diameter, 0.13 inches tube thickness and 18 feet tube length)
42 tubes (2 inches inner diameter, 0.16 inches tube thickness and 18 feet tube length)
Economizer (118 L water holding capacity) -
- 6 tons per hour boiler
- Total shell diameter (8.6 feet)
Total shell length (17.7 feet)
Burner furnace tube diameter (3.4 feet)
Burner furnace tube length (15 feet)
180 tubes (2 inches inner diameter, 0.13 inches tube thickness and 15.2 feet tube length)
Economizer (54 L water holding capacity) -
- The metallurgical composition of the boilers is as follows:
- 12 inches shell casing (H II ¿ DIN 50049-3. 1B)
0.63 inches furnace tube, plain-corrugated (17Mn4 ¿ DIN 50049-3.1A)
12 inches boiler end plates (H II ¿ DIN 50049-3. 1B)
12 inches gusset stays (H II ¿ DIN 50049-3. 1B)
12 inches manhole (H II ¿ DIN 50049-3. 1B)
Bar stays (15Mo3 ¿ DIN 50049-3. 1A)
Tubes (DIN 50049-3. 1B
DIN 50049-3. 1B)
Flanges (DIN 2527
DIN 2633
DIN 2635) - C22.8
Nuts (DIN-EN 24032
DIN-EN 28673)
Bolts (DIN-EN 24014
DIN-EN 20898)
Weld factor = v = 0.8
In the aforementioned details, I have tried to put in all that I could find and which I thought was pertinent.
A careful analysis of the surfaces reveals that there is little or almost no scale on the inner surface of the shells of these boilers and the outer surface of the tubes. However, corrosion is evident on these surfaces, and I have taken pictures of the inside vividly showing its existence.
I wonder if an alkaline boil-out will suffice or if there is a need for an inhibited mineral acid at a certain PH, concentration, temperature and pressure to remove the rust from the surfaces with 'zero or negligible loss of the useful live metal'. These boilers have remained parked at my factory and out of service for almost a year and a half now. During all this time, no precautionary measures like the use of nitrogen were taken. Now that rust has apparently developed, I would like to have it chemically cleaned before the boilers are brought back into operation. I have consulted a number of companies claiming to have expertise in this chemical cleaning field and they have come up with different proposals.
Some have deemed it enough to go ahead with the alkaline recipe of the chemical solution:
- trisodium phosphate
⇦ on
eBay
or
Amazon [affil link]
(5.5 kg per ton)
Soda Ash (10 kg per ton)
caustic soda ⇦liquid caustic soda in bulk on Amazon [affil link] 45% (2.5 kg per ton)
Phosphonate Detergent (0.5-1 kg or L per ton) or Nonylphenyl Ethoxylate np9 (surfactant agent)
Sodium Sulphite (0.5 kg per ton)
Half, among the ones that have advised an alkaline route, have suggested the use of the first three ingredients while the other half have gone for the complete aforementioned recipe.
The other set of companies have recommended an acid-based cleaning program which is to be followed by neutralization and passivation. They talk of connecting the water circuit of each boiler and its economizer and then employing the soaking, circulating and flushing sequence. During this exercise, the acidic medium will come in contact with the inner surface of the shells of the two boilers, outer surface of the tubes contained within these shells and with the inner surface of the tubes of the economizers. While undertaking this cleaning job, they also talk about minimizing the risk of thinning and bagging of tubes to ensure reliable functioning of the boilers subsequent to the cleaning process. One of the companies also refers to the formation of a desired something called 'magnetite' post the cleaning job and during the operation of the boilers if their guidelines are adhered to.
The problem here is this that we are looking at two ends of the spectrum here, both of which claim to have the customized key to the problem at hand. Which one of them is a safer and more efficient way forward? Do both the above mentioned regimens appeal to you folks out there or do you have a more nifty solution to my problem? I am keenly looking forward to receiving your take on this.
Director Operations - Gujranwala, Punjab, Pakistan
2007
Without examination of your system, a definite answer isn't possible, merely a suggestion: Use inhibited hydrochloric to remove the bulk of the corrosion, rust and scale, then follow an ammoniated citric acid
⇦ on
eBay
or
Amazon [affil link] procedure including a final passivation to form magnetite. An outline of the procedure:
1) Use inhibited hydrochloric acid at room temperature to remove ~95% of the corrosion/rust. Pump the solution through and occasionally sample to determine progress. Rinse.
2) Prepare a warm (70 °C) citric acid solution and raise its pH to 3.8-4.0 using ammonium hydroxide. Pump this through the system for 1 hour to remove any remaining rust.
3) Increase the pH to 9 with additional ammonium hydroxide. Raise the oxidation potential to about 900 millivolts (ORP value) by adding hydrogen peroxide (or sodium nitrite, an equally effective oxidizer but a possible pollutant). Pump this warm solution through the system for 1 hour, adding oxidizer as needed. This will passivate the surface by creating a very thin gray film of magnetite.
4) Rapidly drain, rinse and refill with properly treated feedwater.
References
'THE PASSIVATION OF STEEL' for pH & oxidation potential diagrams for processing, plus before & after photos:
http://www.vecom.nl/english/documentation/tb/TB-2005-17-eng.pdf
Some additional diagrams and photos:
www.vecom.nl/english/documentation/tb/VecomTechnicalBulletin-2007-05-ENG.pdf'
Another description of the ammoniated citric process, along with some alternatives.
http://www.angelfire.com/mt/chemicalcleaning/webboiler.html
To avoid further boiler corrosion, contact either NALCO Co. or GE Water & Process Technologies. Both offer professional boiler water treatment services in Pakistan.
- Goleta, California

Rest in peace, Ken. Thank you for your hard work which the finishing world, and we at finishing.com, continue to benefit from.
April 7, 2009
Gentlemen,
1st. I would NOT use Hydrochloric Acid on theses to Chemically clean the water wetted surfaces. There is entirely too much rust present. Rust will convert from Ferrous to Ferric in an oxidized acidic solution such as Hydrochloric Acid.
2nd. Alkaline degreasers will NOT do the trick either. There seems to be NO Hydrocarbons "Oils" in this system, if there were, they would not be rusting!
3rd. This system needs a Fe Chelant such as Di-ammonium EDTA chemical cleaning. This is a three stage cleaning that will need to be performed at 140-150 degrees F. for 8 to 10 hours, followed by Neutralization and followed by Passivation.
This is VERY effective for the water wetted surfaces.
The Air or Fire side of the units "in the Fire Box" is a different story considering the refractory and the dangers of getting chemical soaked into it.
PS I noticed after looking at the pictures more closely, you have some plated Cu (Copper ) in theses units as well. That means you will need to run a Cu removal stage. This is another reason for NOT using Hydrochloric Acid! Chelant Cleaning with a Cu removal stage, the metal loss will not be greater that .0002 Mils per year. This is a acceptable amount. You are loosing more metal by just letting them sit and corrode. If you are going to store them , Store them wet. Full of water containing corrosion inhibitors and Biocides at around pH 10.
A.L.M
chemical cleaning - Houston, Texas
Q, A, or Comment on THIS thread -or- Start a NEW Thread