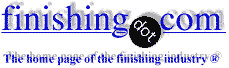
-----
White rust on galvanized pipes -- cause?
Readers: This particular thread focuses on operations within the factory or in shipment which may lead to white rust, or ideas which may be implemented to reduce it. Consumers who are interested in dealing with or removing white rust may find letter 46161 "Removing white spots / storage stain on galvanized metal" more interesting.
Q. Sir,
We see that after 5-6 months the galvanized pipes get white rust on areas of contact with other pipes in a bundle. How we could finish this White rust.
Muhammad YousufIIL Pakistan - Karachi, Sind., Pakistan
2003
2003
A. Do you chromate them and dry them, Muhammad Yousuf? Are the pipes touching during the chromating quench? It sounds like they are either not chromated properly or were not dry in the areas where they are touching (capillary action tries to keep that area wet) -- but please tell us what you've tried :-)
Thanks.
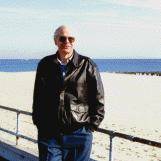
Ted Mooney, P.E.
Striving to live Aloha
(Ted can offer longterm or instant help)
finishing.com - Pine Beach, New Jersey
by Kuklik & Kudlacek
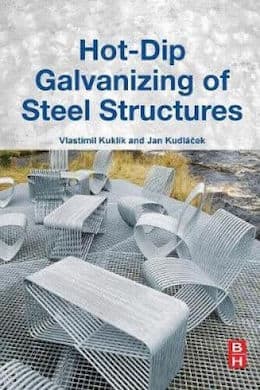
on eBay or Amazon
or AbeBooks
(affil link)
by NACE
[only rarely available]
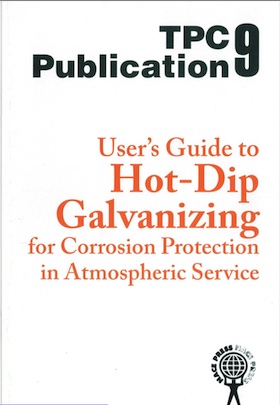
on eBay or Amazon
or AbeBooks
(affil link)
Q. We are pipe galvanizers we are facing a problem of white spot inside the pipe after galvanizing (outer surface is clean and of best finish). Inside we use superheated steam for blow-off, and after blow-off we quench the pipe in water.
Please guide us how to overcome this fault.
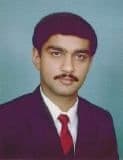
Qaiser Majid
Lahore, Pakistan
A. It could be that this is "white rust", and the steam might be causing it, or the water quench.
Do you have any passivating agent (like weak Chromic acid) in the water? This might help this problem.
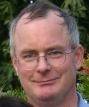
Geoff Crowley
Crithwood Ltd.
Westfield, Scotland, UK
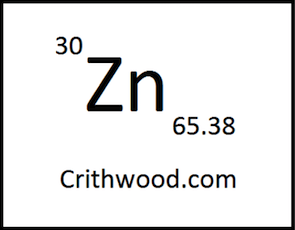
2007
A. Sir,
Do you use hex chrome (sodium dichromate) in your quench? What is the conductivity of your quench water (in micro Siemens)? Is this quench recycled and do you periodically dump and refill? What is the aluminum content of your zinc?
I enjoyed my UNIDO work in Lahore for PECO.
Regards,
Galvanizing Consultant - Hot Springs, South Dakota, USA
Q. Dear Crowley / Dr. Cook,
We use Water for quench and change the water (once a Week) we consume about two tons of Zinc every day.
There is little information on pipe Galvanizing in our country, please guide me to get max. knowledge on this subject.
I appreciate you keeping us posted on your suggestions Wherever you can.
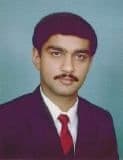
Qaiser Majid
Lahore, Pakistan
2007
2007
A. Quenching in plain water will surely cause white rust, and a dull finish on the galvanized finish.
You need some form of passivation. This might be a chromate type, but there are others. You should be able to purchase a proprietary brand, but there's one thing to be wary of.
Often the instructions are for a passivation chemical concentration designed for treatment at ambient temperature. Quenching hot steel straight from the zinc bath requires a much lower concentration, perhaps a tenth of that for ambient temp. Otherwise you will get severe discolouration using a strong solution. (Brown like chocolate at high strength, yellow - light brown at medium, and no visible colour at the right strength).
You might need to do a little experimentation to get the right strength.
This chemical gets consumed. You'll know when its under strength, as the visible symptoms you describe as your problem now will return. Top up the strength, and they go away.
With this system you will not need to change the water so often, perhaps every 6 months, maybe even annually. But you will need to top up evaporative losses.
Incidentally, that tank removes a lot of heat from the steel. The contents will get hot, nearly boiling. Its a low grade source of heat, but heat isn't cheap these days, you could consider capturing it and using it for something. Just pipe is somewhere and pump circulate it to something that needs some heat.
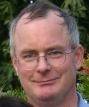
Geoff Crowley
Crithwood Ltd.
Westfield, Scotland, UK
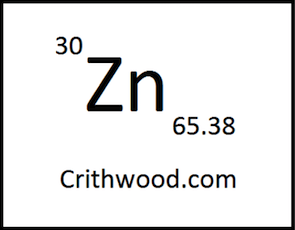
2007
A. Sir:
Please answer the following questions. If you do not know the answer just say so.
(1) What is the aluminum content (percent) in your zinc?
(2) How many tons of pipes do you galvanize each day?
(3) Are you allowed to use hex chrome in your quench?
(4) Is your blow head manual or mechanical-automatic?
(5) What is your angle (from horizontal) of withdrawal from the zinc?
(6) What is the temperature of the super heated steam?
(7) Do you have a steam accumulator near the blow head?
(8) Do you use straight-through, focused, or spiral steam blow?
(9) How are pipes pushed into the zinc?
(10) What is the baumé (density) of your flux solution?
(11) Are you "wet" or "dry" kettle?
(12) What is the temperature of your flux solution?
(13) What is the power of your boiler as a percent of the power of the kettle?
(14) Do you have a wet season, and if so do you have fires in your zinc dust
⇦ on
eBay or
Amazon [affil link]
blowings?
(15) How many microns of zinc are on the outside of pipes and on the inside of pipes (the inside must be profiled)?
Regards,
Galvanizing Consultant - Hot Springs, South Dakota, USA
2007
Q. Dear Mr.Cook,
Sorry for late reply
1- We use very little Aluminium which is about 0.005% of Zinc (What is recommended?)
2- We galvanize about 20 tons to 35 tons per day.
3- We are allowed to use Hex Chrome but we are not using.
4- Our Blow head is mechanical Automatic.
5- Withdrawal angle is about 20 degrees.
6- Super Heated steam is at 450 degrees at Boiler but blower is 145 feet away from head.
7- Yes Steam accumulator is near the blow head, but we have few drops of water falling at every blow.
8- We use straight steam blowing head no spiral.
9- The pipe are feed into Kettle by spiral screws.
10-Flux density is 12~15 degrees.
11-We use Wet Kettle. (Please explain wet & dry Kettle).
12-Flux is not heated.
13- -So-
14-We have July~Sep. wet season but no fires (Explain it?)
15-40~50 microns only out side, not able to record inside thickness (which meter should be used to measure Zn).
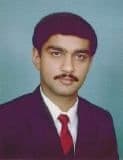
Qaiser Majid
Lahore, Pakistan
2007
A. Sir:
1)30 years ago I thought 0.003% aluminum was good (for bright product). However, there was much white rust. With quadraflux and IQM, I now recommend 0.0005% to 0.001% Al and the product is very bright and almost never white rust. IQM would likely give too thin of zinc on pipes.
2)You said you "consume about 2 tons of zinc every day." Thus your GZU is 7.3%. e.g. ((2/27.5) times 100 = 7.3%) Unless your pipe wall thicknesses are very thin you should be able to do better. I think you have too much zinc inside your pipes.
3)Hex chrome (in quench) at a few hundred ppm and the correct pH normally prevents white rust. Hex chrome causes cancer and is given off if the solution is hot.
4)Is the blow head like a vice grip and air operated? Is it heated?
5)Withdrawal angle is excellent.
6)A little hotter steam would likely be better.
7)Steam accumulator is excellent if it is big enough.
8)Spiral or focused blow head works well on larger diameter pipes.
9)Best pipe zinc entry for smaller pipes is ventilated, progressive, small diameter screws. Ventilated means the screws are spiral rail twisted around the drive core and the rail is connected via spokes. Progressive means the pitch is greater at the zinc entry and less in the zinc. Small diameter means a foot or less and the pipes do not pass under the screws.
10)This flux density is on the low side.
11)"Wet" kettle has black bubbly layer of top flux on zinc. "Dry" kettle is just zinc surface. Usually "dry" kettle gives better zinc usage. Proper equipment is required for "dry" kettle.
12)Most pipes flux solutions are gently heated. Do you dry the flux on the pipes in a drying oven? What temperature?
13)For the boiler to supply 400 pipe volumes of steam per blow it must have about the same power as the kettle.
15)Cut pipes lengthwise and use permanent magnet "banana" gauge or cut pipes crosswise with 10 cm segments every meter of length. Weigh 10 cm segments and then tape with two layers of electrical tape on outside. Strip inside zinc with cold, conc. HCl. Take off tape, rinse, dry and reweigh. Calc. zinc thickness and profile along the length of the pipes. Least thickness will be at the bottom of the pipes and greatest thickness will be about 1/3 from the top. Roughness of zinc indicates thicker zinc.
Regards, Dr. Thomas H. Cook
Galvanizing Consultant - Hot Springs, South Dakota, USA
Need alternative to hexavalent chromate quench
Q. What alternatives are there to sodium dichromate?
We are being pushed by some clients to install quenching agent, but are reluctant to introduce cancerous agent to factory. There has been no quenching done at this factory for 10-15 years now.
galvanizers - Stratford, Taranaki, New Zealand
2007
A. Sir:
Quenching in plain water is much more likely to cause white rust than not quenching. There seems to be trivalent chrome for quenching which is said to be much safer than hex chrome. The worst case is HOT hex chrome, which emits hex chrome from a boiling solution far above USA EPA standards. I did many, many lab tests years ago and made a 1 hour video during the tests.
The main problems in not quenching is that the steel retains the heat and the outer pure zinc layer continues to alloy with reactive
(silicon semi killed) steels and thus turns gray. Also the steel is hot and difficult to unrack. The turning gray problem does have solutions.
Regards,
Galvanizing Consultant - Hot Springs, South Dakota, USA
2007
A. It is possible to use a chrome based quench at high temperatures (like 90 °C) and stay well within the UK exposure limits. (I do not know how USA compares with UK limits).
Its all a matter of concentration, but then wrong concentration produces wrong results anyway. Too strong = brown staining. Too weak, and you might as well use water and suffer the resultant white rust.
The chromic acid is consumed, so it must be tested and concentration adjusted about twice a week. (dependent on production level).
In the Taranaki boondocks, maybe weekly would do! (Cheekiness from a Kiwi of the migratory sort)
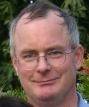
Geoff Crowley
Crithwood Ltd.
Westfield, Scotland, UK
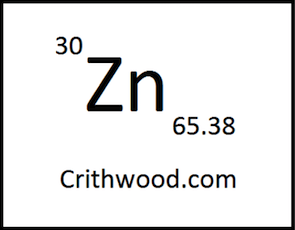
2007
Can we quench first in plain water?
Q. Dear Goeff/Thomas,
Thanks for all your replies which guided us a lot.
As far as for the hex-chrome environmental issue please let us know that if we quench the pipe in plain water first and then in Chromic tank would it be better option for health and safety of our workers who are actually working on the Galvanizing plant, by doing this can we achieve the actual results of prevention of white rust.
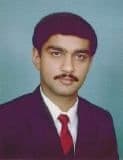
Qaiser Majid
Lahore, Pakistan
February 22, 2008
A. We are presently galvanizing pipes from 3".Firstly the gross zinc consumption should be in between 3% to 4%. Secondly you can use sodium dichromate for quenching along with some sulfuric acid. Are you sure these are not rubbing marks because of the internal die. The pressure of the air should always be checked as because it will cause oxidation and drying up of zinc fast.
Nitesh agarwal- kolkata, India
July 12, 2008
Q. Sir,
How important is it to do quenching in water after galvanizing. It we don't quench in water, the article becomes very dull. How to achieve bright finish without quenching in water.
corrosion controls - Ludhiana, Punjab
September 11, 2012
A. Dear Aman;
Actually, quenching in water would have dull finish. I don't really understand how your pieces become brighter with water quenching.
I can think of one possibility; you might have very "thick" pieces like 20-30 mm. Then heat content of the material will result in gray finish. There is nothing to do for that but just using high Ni content on bath ( 0.6% ^0.06%). But then you will face reduction of coating thickness (maybe under any given standards).
If you give more detail about your production then we can help you more efficiently.
- Ankara, TURKEY
September 12, 2012
Sir:
To suggest using 0.6% Nickel in a zinc galvanizing bath is not realistic. Perhaps you mean 0.06% nickel? I believe you mentioned excessive floating dross in a different finishing.com thread. Likely if you use high nickel in your zinc you will indeed get excessive floating dross.
Regards,
Galvanizing Consultant - Hot Springs, South Dakota, USA
September 14, 2012
Sir;
You are right, I meant 0.06%. I don't use nickel in my bath (it is below 0.01). And floating dross in not due to "after vacation phenomena", because we work 7 days a week. Every worker has different off days, so there is no "non-working" day.
I am still thinking it is because of flux, because after I increase the wetting agent, it is reduced. Anyway, I have ordered some "zinc purifier" which will react with iron in bath and reduce floating dross.
- Ankara, TURKEY
September 15, 2012
Sir:
What is the composition of your kettle zinc? Especially regarding lead, nickel, tin, bismuth, and aluminum. ICP is a very good method to determine these elements in your zinc.
What is the construction of your kettle furnace? Do you have several inches of high strength castable insulation under the kettle? Are the sides near the bottom of the kettle insulated about 9 to 12 inches up from the bottom? Do you apply any heat whatsoever to the bottom of the kettle? From what country did you obtain your kettle furnace?
I do not like what you have said about floating dross and I am trying to find out what is causing it in your case.
Galvanizing Consultant - Hot Springs, South Dakota, USA
September 18, 2012
Dear Sir;
Some of the recent analyses of the kettle are:
Al % Pb % Ni % Sn % Fe % Cu % Cd %
0.005 0.391 0.01 0.001 0.036 0.027 0.0031
0.005 0.65 0.01 0.002 0.026 0.03 0.0035
0.005 0.64 0.01 0.002 0.128 0.029 0.0035
0.005 0.474 0.01 0.002 0.019 0.029 0.004
As you can see, the Fe content is very unstable. And I still can't understand the reason.
About the furnace:
Kettle sits on a kind of heat refractory concrete floor with the thickness of 12 cm, and below it there is normal C20 type concrete. Walls are made of refractory and insulation concrete. Also ceramic fiber blankets are used between layers. There is no extra insulation for the bottom sides. Furnace is heated with 2 high velocity burners, diagonally opposed on the kettle sides. Kettle is a Chinese product, I have no experience on this brand, and I always used German kettles. Maybe that can be the reason.
- Ankara, TURKEY
September 19, 2012
A. Sir:
The dross must have a protected "cool zone" at the bottom of the kettle AND another protected zone at the zinc/air interface to prevent "wash line" erosion. The lower zone is from 9 inches to 12 inches vertically and the upper zone is 6 inches vertically. Without the lower cool zone the dross is heated and travels upward to the zinc/air interface. Normal kettle life is 10 years and I am now trying for 20 years. These and other items are discussed in my article "Burning Issues Impact Kettle Purchases" in the magazine METAL FINISHING at:
Metal Finishing, April, 2005, Volume 103 No.4, pages 46-50.
Metal Finishing, May, 2005, Volume 103 No.5, pages 50-54.
These two halves of my article can be obtained via inter-library loan or directly from the magazine.
Regards,
Galvanizing Consultant - Hot Springs, South Dakota, USA
Q. We are an ERW Pipe manufacturer & Galvanizer in UAE. One of our customers from the US is complaining that the pipes supplied by us in thickness of 1.6 mm are getting white rust after approx. 6 months; and the rest, other thickness pipes, are not getting white rust. While on investigation we came to know HR coils used for manufacturing; all the pipes are of same batch No; our manufacturing process for all the pipes are same as for 1.6 mm material, all the material stored in similar area. We unable to understand what is the problem and how to cure.
Umesh DalelaGalvanizer - Abu Dhabi, UAE
July 5, 2014

Q, A, or Comment on THIS thread -or- Start a NEW Thread