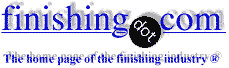
-----
Theory of zincate and adhesion of electrodeposits on aluminum
2007
Q. We are a R&D company with a multidisciplinary employee group , but our exposure to plating is minimal. We have been using outside contractors to produce electrodeposits on aluminum. The testing procedures we use give us very poor adhesion results.
Our criteria require impact adhesion and masking of articles in most cases limit total encapsulation of prototypes.
We are aware of the method of electroless nickel strike over zincate pretreatment of the aluminum but have not tried this as yet.
We are aware of the problems in zincating aluminum to be alloy specific.
To date the processing has been the normal cleaning , etching and double zincate process.
Next step is Sulfamate nickel electrolytic plating about 15 microns, and acid copper up to 25 microns over the nickel
The literature shows that a standard method was to follow zincate with cyanide copper , but that seems out of favour now with the EPA restrictions on cyanide plating processes.
As far as we are aware the zincated aluminum goes live into the sulfamate tank , but we only have the word of the sub contractor that this is so.
All our testing failures have been at the aluminum zinc interface and in most cases there is no evidence of any zinc present. In some there are traces of zinc.
We would appreciate some explanation of the theory involved in the zincating of aluminum.
We understand that the zinc is an immersion deposit and the weakest link in the chain.
Our question and supposition is if the zinc were to be completely dissolved chemically in the low pH of the sulfamate should there be an atomic bond between the aluminum and the nickel?
This could occur if there were a delay in the application of current of more than a few seconds.
If the zinc is chemically dissolved in the nickel solution does the aluminum still oxidize although not exposed to air?
Would any dissolved oxygen oxidize the aluminum?
One of the zincate process vendors has claimed that their process produces a 20% ionic bond and 80% immersion/chemical bond of zinc to aluminum.
We hope that a better understanding of the theory governing this process will clarify some of the divergent opinions we have gleaned from various sources.
prototyping technologist - Carlsbad, California
A. More than anything, you need a vendor that can produce high quality plating. Half of the time, this is from black magic as much as from science.
The EN strike will make a big difference.
The main problem with zincate is that it does not have any GOOD visual cues as to quality.
Start talking to other shops about your job with the quantity and turn around. Ask for plating on samples that you provide as a pre-contract requirement and the ongoing quality that you need. It may cost a bit more, but rejects cost a lot more.
- Navarre, Florida
A. 1) Follow the pretreatment procedure given by the electroless nickel (EN) chemistry vendor. Proprietary, alloyed zincates are better than generic, and the second zincating should be short in duration (15-30 seconds).
2) Most opiners on this forum favor an alkaline EN strike following zincating. Zincate is relatively unaffected by this pH 9 solution, unlike acidic plating baths.
3) Zincating is the creation of a barrier to avoid oxidation of the aluminum by air and water. Dissolved oxygen isn't necessary; aluminum reacts with water.
4) Why claim "a 20% ionic bond and 80% immersion/chemical bond of zinc to aluminum?" Ideally, metallic bonding (zero-valence) is desired.
5) Buy and read Electroless Plating by Mallory and Hadju [on
eBay ,
Amazon, or
AbeBooks affil links]
.
6) See also ASTM B253, 'Standard Guide for Preparation of Aluminum Alloys for Electroplating.' For an electrolytic nickel strike following zincating, neutral & near-neutral solutions are given.
- Goleta, California

Rest in peace, Ken. Thank you for your hard work which the finishing world, and we at finishing.com, continue to benefit from.
A. Try Single zincate, rinse, 4 oz/gal baking soda, rinse, ALKALINE electroless nickel strike, rinse, then anything.
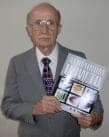
Robert H Probert
Robert H Probert Technical Services

Garner, North Carolina
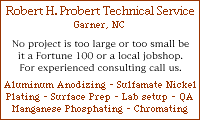
Q, A, or Comment on THIS thread -or- Start a NEW Thread