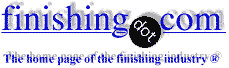
-----
White spots left by mineral oil on galvanized steel
Quickstart:
"White rust" spots on galvanized steel are sometimes called "wet storage stain", which is probably more indicative of what usually causes it.
Q. Hello sir, we have a similar kind of problem. A couple of years ago the coolant we use was discontinued by the company, and since then we have tried many coolants for our roll forming operation of galvanized steel ... but nothing really worked.
The problem is we store them outside, tightly packed, just after manufacturing and after afew days they develop white rust or storage stains. We continued this practice from our successful coolant as well but then there was no issue at all.
Coolant manufacturer recommended us to maintain pH of 9 and we are doing that as well. Despite that the problem persists. We even tried to store them inside and they still have the white spots. Looks like the issue is with the coolant, so if you have any suggestion for good coolant that works for roll forming of galvanized when products are stored outside in aqueous environment. we're having lots of rejected pieces. If anybody else is facing same issue please help.
Ed. note: Sorry pics not added until 8/18/24
kuldip singh
shop employee - abbotsford, british columbia, canada
July 31, 2024
A. White storage stains, sometimes called white rust form when water (even if contained in a forming lubricant), gets on galvanized steel that is stored touching other galvanized steel. There are several ways to minimise it, or even eliminate it.
Keep water away. Dry stored galv; even touching, doesn't form white rust if it's dry.
Keep the items separated: If wet but not touching other galv steel, minimises the problem.
Passivation: Using Chrome solutions after galvanizing passivates the surface of the coating and this usually gives a few weeks protection (not forever) in storage, even when wet and touching.
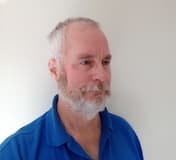
Geoff Crowley, galvanizing consultant
Crithwood Ltd.

Bathgate, Scotland, UK
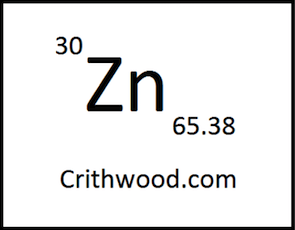
Q. Thank you sir for your suggestions. we can dry them before packing and stacking on each others, but the problem is we have to store them outside afterwards and when the rain comes, they are going to get wet again. we cannot store them inside as we are space restricted. with our previous coolants, we used to store them outside as well without any of this issue. Is there any suitable coolant for roll forming of galvanized steel that can provide rust protection in the outside environment or any recommended rust preventative that we can apply as secondary process, or we can mix that in our existing coolants to make them robust for white rust protection. your help in this regard will be highly appreciated.
thank you.
shop employee - abbotsford, BC, Canada
A. Hi
Please remember that galvanizing is a corrosion-resistant finish. It should not / does not require protection from the environment. What it requires is an environment / situation where it can display that corrosion resistance.
Start dry, and make sure the pieces don't nest in a way which encourages capillary moisture retention while discouraging good air flow and things may be alright. Exposure to good air flow allows the formation of a corrosion-resistant glassy zinc carbonate surface.
Luck & Regards,
Ted Mooney, P.E. RET
Striving to live Aloha
(Ted can offer longterm or instant help)
finishing.com - Pine Beach, New Jersey
Multiple threads merged: please forgive chronology errors and repetition 🙂
for Engineers, Shops, Specifiers
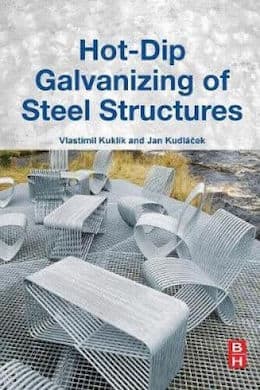
avail from eBay, AbeBooks, or Amazon
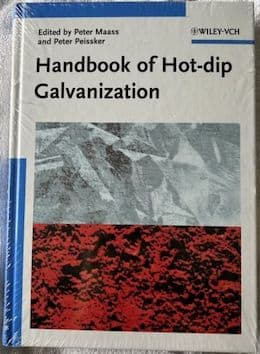
avail from eBay, AbeBooks, or Amazon
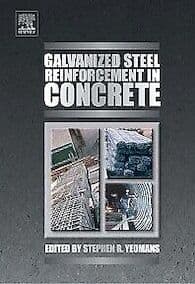
avail from eBay, AbeBooks, or Amazon
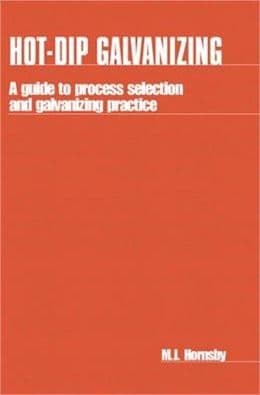
avail from eBay, AbeBooks, or Amazon
avail from Amazon
"User's Guide to Hot Dip Galvanizing for Corrosion Protection in Atmospheric Service" by NACE (1997 only rarely avail.)
avail from AbeBooks, or Amazon
(as an Amazon Associate & eBay Partner, we earn from qualifying purchases)
My company produces pallet rackings. Our profiles (beams and uprights) are produced in-house from galvanized steel coils. I am a civil engineer, so please forgive me if my questions seem too vague or trivial to you.
During the last year, it happened for a couple of times that the lubricant we use in our production lines did not wash away and left white spots on the finished products.
A diffractometry shows higher values of C and O corresponding to the spots. Most likely the spots are given by the solidification of one of the components of the lubricant. The lubricant is mixed with potable water.
My questions are:
1. Did anyone have a similar problem?
2. What are, if existing, the possible reactions involving Zn producing white solid matter? How can I test if this is the case?
3. What are, if existing, the possible reactions involving Cr(III) producing white solid matter? How can I test if this is the case?
I know these are very vague questions, my hope is that someone could at least give me some advice about how to circumstantiate them (as far as I can).
Thank you.
- Rovereto, ITALY
2007
Q. Dear Thomas and Ken,
thank you for your quick reply.
I'll try to answer your question as thoroughly as I can, please consider that at this moment I have only second hand informations. I'm setting up a series of tests to try to reproduce the problem.
@Thomas:
The mineral oil is basic (pH 9.6 - 10.1 at 3% distilled water). I have four pH measurements, probably made too late with respect to the moment the problem showed (6.75, 6.89, and 7.14), only one is basic (8.60). The measurement taken from the circuit serving the line which had problems is one of the neutral ones. Anyway, during the next week, while trying to reproduce the problem, I will record a time-history of pH.
As far as I know, there's no Cr+3 in the lubricant, I was thinking to the chemical passivation used by our suppliers, which are switching to Cr+6-free processes.
@Ken:
Can white rust form in a few seconds?
Let me tell you that I've been reported that the problem showed up one day with a few coils from the same source. It appeared both wetting them with the emulsion and with water. Some days later, the same coil had no problem at all. I do not have any evidence about it, only word of mouth (it happened before my arrival and none kept the samples).
White rust appears when the zinc coating is young and has not yet oxidized on the surface, so maybe when the coil has been first used the pure zinc on the surface, maybe not sufficiently protected by the passivation layer, reacted with water, while 5 days later nothing happened because meanwhile the zinc oxides layer fully developed. Could it be the case?
Summary:
- spots appearing under water and emulsion drops in few seconds, before evaporation;
- young coil (used two days after arrival, so possibly very few days after production) showed the problem;
- same coil, 5 days after, did not show the problem.
Obviously if the white spots are zinc carbonate monohydrate, trying to reproduce the problem on the same year's old sample will be a waste of time.
Is there a lab test I could do or ask for in order to identify white rust?
Thanks again for your help.
- Rovereto, ITALY
A. Sir:
My experience (perhaps 20 cases) is with hex chrome, a pH of 4.2, and special additives which work very nicely. I have no experience with trivalent chrome but the fact that a low pH is usually used makes me think it can work.
I have only two experiences with high pH quenches. In one case it was a dulling solution and it did dull, but also caused a white coating on the zinc coating. The other experience also produced a white coating on the zinc. In both cases the white coating was not expected or desired. Likely I cannot help you additionally.
Regards,
Galvanizing Consultant - Hot Springs, South Dakota, USA

Q, A, or Comment on THIS thread -or- Start a NEW Thread