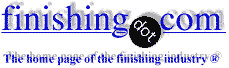
-----
Bubbling problem when plating on Zamac
Q. Hi;
we are doing white bronze and black nickel-free on ZAMMAC material...and facing a huge problem, that after 10-15 days of plating bubbles are coming out on our material. The important thing is that if we are doing the same process on brass material(instead of zammac) then these bubbles are not coming.
Please let us know why these bubbles coming on surface ?
What is the solution of this problem ?
chemist - Lahore, Pakistan
2007
2007
Q. Previously I had discussed about bubbles problem (blister problem) in our plating finishes but I didn't get any answer about this I have giving some more information about the process may it help you..
Now these bubbles are coming even after alkaline copper; the composition of the alkaline bath is:
CuCN 44.4 g/l
NaCN free 15 g/l
On Hull Cell
⇦ huh?
it gives good results and our bath parameters are in range.
Let me know does it depend on composition of zamac and parameters during casting and molding?
thanks,
chemist - Lahore, Pakistan
A. The plating process for brass is quite different than that of zamak.
Please send info regarding the whole plating process that you use so we can try to detect the cause of the problem.
The alkaline cleaner should be only slightly alkaline otherwise you get have adhesion problems.
Do you use an acidic activator with fluorides?
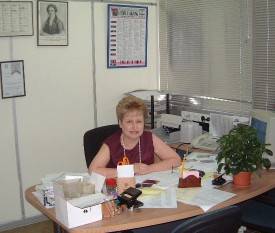

Sara Michaeli
Tel-Aviv-Yafo, Israel
2007
Q. Dear Sara:
thanks for your cooperation! In this I have mentioned all of my plating process and hope that I will get solution of my problem
The process on zamac is chemical degreasing at 50 °C, electrolytic degreasing at normal temp., dipping (ammonium bifluoride and HCl) at room temp.
Then alkaline copper at 55 °c, neutralize, copper acid at 21 °C, electrolytic activation, white bronze at 50 °C, then black nickel-free at 50 °C.
NOTE:after each step we have done through rinsing.
Thanks
chemist - Lahore, Pakistan
2007
Is the electrolytic degreaser high in alkalinity? It should be low.
The HCl should be changed to H2SO4. The fluoride/sulfuric acid dip has to be recharged often.
How long do you plate in the cyanide copper? At least 30 min.
The most important - what do you use for the neutralization between the two copper solutions? This should be fresh and it should contain an ingredient that removes the oxides from the first layer of cyanide copper.
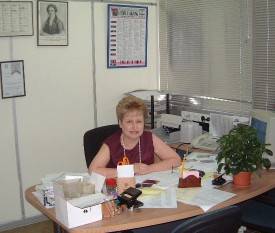

Sara Michaeli
Tel-Aviv-Yafo, Israel
2007
2007
Can any body help me?
Ref. letter no. 45177.
b/w two coppers we are using H2SO4 about 5% concentrated.
In alkaline copper we've given 45 minutes
About dipping: we are using this composition from one year and never face problem like this ... our supplier is situated in Italy and a lot of industries there are using the same composition successfully.
One thing I would like to discuss is that when I scratch the bubble I didn't get copper inside but white spot ..or the zamac
The second thing is that if my casting is porous than what is the chance of bubble formation?
Thanks,
chemist - Lahore, Pakistan
August 2013
Hi Uroj. You won't successfully plate castings that have porosity or cold shuts. Many shops do 100% inspection of zamac castings before plating. If you cannot get castings free of porosity, you could try vacuum impregnation. Good luck.
Regards,
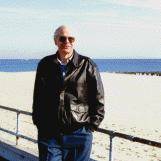
Ted Mooney, P.E.
Striving to live Aloha
(Ted can offer longterm or instant help)
finishing.com - Pine Beach, New Jersey

Q, A, or Comment on THIS thread -or- Start a NEW Thread