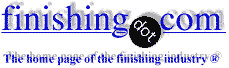
-----
Powdercoating stainless steel Q&A's, Problems and Solutions
October 7, 2021
Q. Please forgive my ignorance on matters of finishing included in this post. Powdercoating is not an area we generally deal with.
I am currently working on a design of a prototype concrete deck repair in a commercial (Condo) setting, the property is beach front in South Carolina, hence it is subject to high heat, humidity, and sea spray.
The client requested a cable rail system to go back in place of the original rail system.
Our main goal is to prevent a recurrence of the deck damage we are repairing, followed by the long-term durability of the aesthetic of the railing posts.
From my understanding of powder coating, bubbling, chipping or other surface imperfections that may arise are generally caused by imperfections in the substrate, not removed during the preparation and pretreatment phase.
We have selected a design and a vendor for the cable rail system, and specified stainless steel to be used for rail posts. The vendor uses 316 Stainless Steel and will powder coat the posts to the client's preferred color. The vendor uses Tiger Drylac Super Durable coatings and has explained that their process for coating Stainless Steel is as follows:
- Sandblasting all parts
- 5 stage cleaning process:
o Alkaline cleaner
o Hot water rinse
o Iron phosphate wash
o Cold water rinse
o Application of non-chrome sealer (followed by baking to remove any residual moisture)
- Priming with the additional step of Zinc rich primer applied for outdoor applications
- Topcoat application (colour)
As we are less familiar with powder coatings vs Kynar we are looking for advice on whether the process stated above is the best method, or if there are any modifications?
Is the zinc-rich primer as stated allowed to be used with stainless steel? Or is there any aspect of the process listed that would allow it or is it simply not needed with stainless steel. I have only this morning when looking at product data sheets that this may not be best practice.
Thanks in advance.
- Charleston, South Carolina
⇩ Related postings, oldest first ⇩
Q. I don't really understand why anyone would want to powdercoat on top of stainless steel, but we recently received an enquiry. The material is very smooth almost polished, and adhesion will not be easy to achieve. Any suggestions? Was considering shotblasting to reprofile the surface for mechanical adhesion.
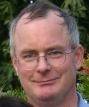
Geoff Crowley
Crithwood Ltd.
Westfield, Scotland, UK
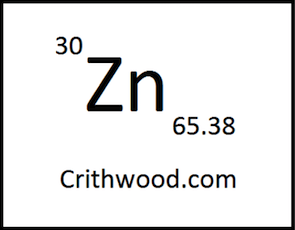
2007
A. Painting stainless is purely cosmetic and won't be resistant to chipping and other adhesion problems. You'll need to CYA if you paint it by making the customer sign something saying that he understands and agrees with the terms. Reprofiling the surface is like taking away the reason the product is made from stainless. Don't do it without his permission unless you want to buy it all back some day.
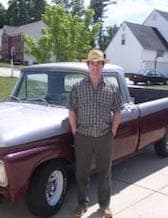
Sheldon Taylor
supply chain electronics
Wake Forest, North Carolina
2007
Q. The customer is quite happy to have the SS shotblasted. Like me, he thinks its crazy to powdercoat SS. If PC is the desired finish, then PC over galv mild steel will be adequate. If SS is the desired finish then why PC? (Colour = silver).
Its as crazy as some requests we get to PC over galv steel in "a colour like galvanizing".
Its an interesting point of discussion how far a coater should go in telling a customer that what they want to do is not sensible. We declined a job recently where customer wanted PC on mild steel (not galv) for an indoor swimming pool area. This after long discussions about corrosion.
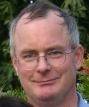
Geoff Crowley
Crithwood Ltd.
Westfield, Scotland, UK
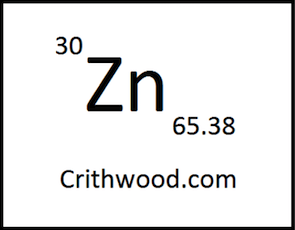
2007
A. Powder coating SS is more common than most would think, powder coating SS gives you many advantages over coating CRS or HRS or all of the pre plated materials out there. The main advantage is that corrosion is at a very small percentage, and SS if prepped correctly it will hold up to adhesion as well as many other destruct test.
DOD/AERO/SPACE
Aero space - Longmont, Colorado
2007
A. Hello
I tried to coat over stainless steel sheets using Polyester powder electrostatic spraying & baking.
The stainless steel was brushed finish
We etched the surface with ANTOX
The powder coating was successful.
- Abu Dhabi, UAE
2007
If you have not been able to obtain Antox material try a sample of Anoprime from the UK
Terry HicklingBirmingham, United Kingdom
2007
----
Ed. note: Chemical names or descriptions of the types of etchants, please, readers -- not proprietary names!
Blisters between stainless steel substrate and powder coating
February 24, 2016Q. Hi everyone,
We are a painting company from the UK coating mainly automotive parts (interior+exterior). I'm currently trying to figure out the cause of blistering under our paint system on an exterior stainless steel (grade 304) rejected car part from Taiwan.
To put you in context, the process of the part was the following:
- The stainless steel parts were vapour degreased with methylene chloride (no prep before)
- Then degrease wipe
- Powder coating
- Primer
- Basecoat and lacquer
The whole part is covered with blisters. After analysis of the part under the microscope we can see the blisters are coming from the interface substrate/powder (see photos attached).
What do you think caused the blisters ? Is stainless steel porous enough to catch contaminants that couldn't be removed with our cleaning process? (see "holes" in picture)
Thank you very much for your help, please let me know if you need further information to reply to my questions,
Kind Regards,
Audrey GenayProject engineer - UK
A. Sir,
Methylene Chloride is a paint stripper not a solvent degreaser.
That is possibly the beginning of your woes?
Trainer - Salamander Bay
February 27, 2016
A. Hi Audrey. William is deliberately being very gentle :-)
First, as he says, methylene chloride is not a proper degreaser. It sounds quite unusual to me to use it in a vapor degreaser, and I'm not sure whether it is even legal in your jurisdiction. Wiping with a better solvent is sometimes done in unusual situations, but it is not a proper pretreatment.
I would suggest alkaline cleaning or sandblasting, followed by a self-etching primer. Good luck.
Regards,
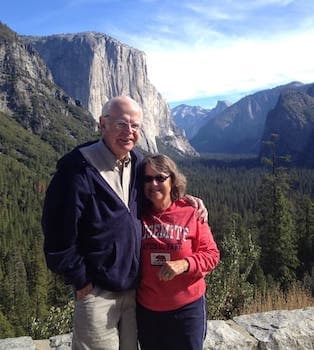
Ted Mooney, P.E. RET
Striving to live Aloha
(Ted can offer longterm or instant help)
finishing.com - Pine Beach, New Jersey
February 2016
Durable (Scratch & Chip Resistant) Coatings for Stainless Food Service
Q. How are you? I am the Purchasing Manager at a Holloware Manufacturing Co in Bronx, NY. My question is regarding the best fit powder coat solutions for some product line parts. Specifically I have stainless steel food pans that we powdercoat in white. We know for sure that our current supplier is not sandblasting these parts prior to spray coating. That aside we are looking for a more durable coating that is food safe (or that we can certify as such).
We have stumbled upon nylon (Corvel) but don't know enough about it, as well as a "rubber" e-coating that we have heard could possibly be better.
I would like to know your opinions and thoughts regarding.
Thanks in advance for your support.
Purchasing Manager - Bronx, New York, US
March 9, 2016
Q. Is there is any problem in Powder coating on polished stainless steel?
Thanks
Akshay
Bison Pumps - Conway, Arkansas, USA
December 20, 2017
A. Hi Akshay. I don't think there's any problem in powder coating onto polished stainless steel which has been properly pretreated. But if you are talking about simply powder coating directly onto polished steel, I think I'd expect terrible adhesion problems.
Regards,
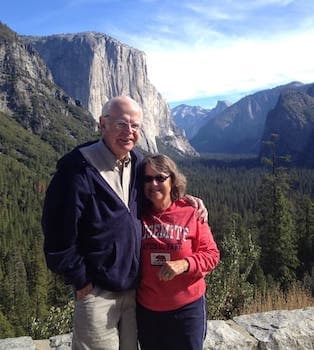
Ted Mooney, P.E. RET
Striving to live Aloha
(Ted can offer longterm or instant help)
finishing.com - Pine Beach, New Jersey
December 2017
A. Akshay,
I don't think there's any problem per se, but keep in mind you are:
1. Paying extra for stainless steel and then covering it over, making your choice of alloy a moot point.
2. Paying extra for a polished surface which, if anything, probably reduces the adhesion of the powder.
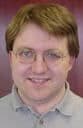
Ray Kremer
Stellar Solutions, Inc.

McHenry, Illinois
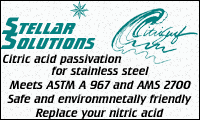
January 3, 2018
January 9, 2018
A. It seems to me that this is an ill defined question.
The metal finishing industry in the western world can and has overcome very many challenges over the centuries.
We always come back to the points that:
(1) you must fully define the substrate and it's condition.
(2) you must assess what facilities are available to the artisan.
(3) you must quantify the performance factors required of the finished article.
In this instance it is highly unlikely that organic coating wet or powder is going to provide any mechanical properties, i.e., Adhesion, impact resistance or abrasion resistance.
On the other hand if a purely aesthetic appearance is the key performance criterion then that is achievable.
Drink deep or taste not the pierian spring.
There, shallow draughts intoxicate the brain and drinking deeply sobers us again"
In other words fully define the problem and the desired outcome before you can hope for a result.
Hope this helps.
Regards,
Bill
trainer. - salamander bay nsw australia
Q. Hello.
I had some work done by a well renowned powder coating company on a stainless steel radar arch.
Now it's gone a year and I can see rust coming on edges and on a few small cracks here and there.
The company says to me that the work he's done is impossible to get that rust.
I've had a other company sandblast it and it had white powder coating on before.
So my question to you is what do you think has happened?
- Gothenburg Vastragotaland Sweden
February 8, 2018
A. Hi Alex. Sounds to me like the stainless wasn't passivated before powder coating. If iron from previously used sand contacts stainless steel it will rust. The powder coating probably protected it for a year and that's all.
Regards,
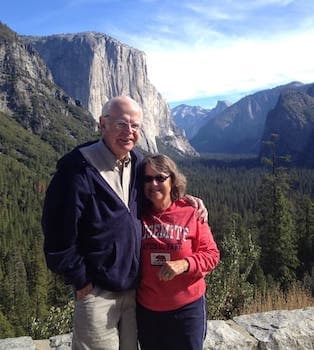
Ted Mooney, P.E. RET
Striving to live Aloha
(Ted can offer longterm or instant help)
finishing.com - Pine Beach, New Jersey
February 2018
A. It also sounds like there are microcracks in the stainless. Look at the coating carefully. Good luck.
Harry Hudson- Durham, North Carolina
March 15, 2018
Q. My question is:
Is there a method other than sand blasting to configure a stainless steel surface for powder coating?
El Sewedy electric industries co - Cairo , Egypt
April 23, 2018
A. I live/work in Florida and we Powder coat all of out exterior 304 stainless steel enclosures to reduce heat. A stainless steel enclosure, unpainted,in the direct sun will reach 300 °F inside the cabinet, but powder coat it bright white and the temperature will stay below 120 °F in full sun. The electronics last much longer if you keep it cooler.
Phil MarjasonParalee Company Inc - Orlando, Florida
July 3, 2018
July 2018
Excellent point, Phil. Thanks!
Regards,
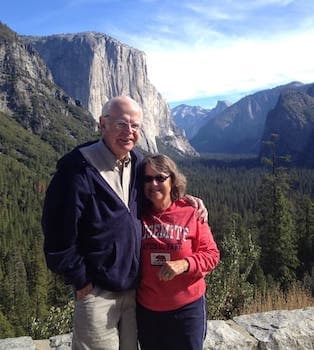
Ted Mooney, P.E. RET
Striving to live Aloha
(Ted can offer longterm or instant help)
finishing.com - Pine Beach, New Jersey
Want Stainless shiny for looks but etched for powder coating adhesion
Q. My situation: I appreciate all of the great knowledge and forum posts that I've had a chance to read through. I'm hoping someone can help me out with a somewhat unique problem. I am powder coating small polished 316ss parts more for decoration then anything. The parts are so small that bead blasting has proven futile. I was trying to find answers towards a chemical etch product that might be available that would help give me more tooth to the polished 316ss but still keep some of the shiny polished look. This is so that I don't have to apply a chrome powder then a topcoat candy powder. My knowledge with all the chemical options is limited.
Thank you for your time
small business/hobbyist - Houston, Texas, USA
July 25, 2018
A. Hi Adam. You already recognize what the actual problem is: that you seek diametric opposites, a very smooth finish for looks and a very toothy finish for adhesion.
We have numerous threads about etching stainless steel, which can be found by using the search term "etch stainless" in the google custom search engine. ferric chloride ⇦ on eBay or Amazon [affil link] is probably the most common and universal etch, but a silver bullet that can both etch and not etch doesn't sound possible. And even if it were, expecting really good adhesion without pretreatments which will obscure the shine, doesn't sound promising.
Your idea of chrome-look paint/powder reasonable to me.
Regards,
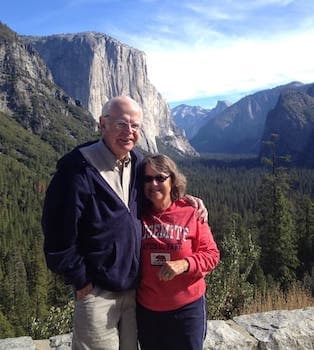
Ted Mooney, P.E. RET
Striving to live Aloha
(Ted can offer longterm or instant help)
finishing.com - Pine Beach, New Jersey
July 2018
Q. We are making surgical instruments using 410 SS. The passivated parts show good corrosion resistance. The passivated parts followed by partial powder coating shows corrosion problems. What may be the possible reason.
M Y Anwar- Lahore, Pakistan
September 14, 2018
A. Hi Anwar. More words please :-)
Do you mean that you first passivate the parts, but then you send them through a pretreatment process? And the area which has now been pretreated, but does not get powder coated, corrodes? If so, what pretreatment sequence must they endure?
Regards,
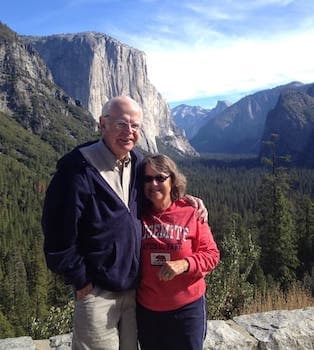
Ted Mooney, P.E. RET
Striving to live Aloha
(Ted can offer longterm or instant help)
finishing.com - Pine Beach, New Jersey
September 2018
Q. I am working on surgical instruments made with stainless steel AISI 410 having small portion powder coated.
After boil test I am having scattered spots of rust on a few pieces at the naked area. What could be the possible reason?
Surgical Industry - Sialkot Pakistan
September 17, 2018
A. Hi,
having read through this thread I think I can lend some important information on stainless steel. I ran a body shop specializing in North American highway coaches for 15 years. These are built of mostly of 3xx series stainless steel and the outside skins were stainless or aluminum into the 90's. Today one manufacturer still skins in stainless steel. Is there a reason to paint or powder stainless? you bet. The stainless gave the rust prevention on the inside of the panels and the paint gave the desired look on the outside. It was routine to leave bare stainless on the bottom luggage doors for durability but the sash panels between those and the windows were always painted with company colours.
Adhesion: You have to understand how stainless resists corrosion. Oxidization. The surface of stainless steel you see is not stainless steel, you are seeing through a semi transparent layer of oxidization a few atoms thick. This keeps the rusting process from starting by sealing the surface (this oxidization is not rust) It is very very hard and smooth and nothing I know of will stick well to it. The oxidization has to be removed or else paint will peel off easily. I will describe the process we used that gave us a 100% success rate and no warrantee returns (and yes we had some before learning this process)
We scuffed the panels with red Scotch-brite pads making sure every rivet was also completely scuffed. You can see a colour change when you have torn that layer of oxidization off, it is less grey and brighter, and yes this is hard work, but for us the only one that was nondestructive and could get all details. (sandblasting warps the 22 ga. panels).
The critical part no one has mentioned here is time. This layer starts to rebuild immediately. We set a 2-1/2 hour time limit from the beginning of prep to the time the painter was starting to apply a vinyl wash etch primer. An etch primer will not - NOT - break down oxidization one day or more old, it is very tough stuff. An etch primer will however check the oxidization in the last 2 or so hours.
Our process was as follows; the coach was moved into the paint booth then completely masked. Then (no later than lunch) 4 staff were pulled off what they were doing and put on to scuffing both sides at the same time. Each starting at a corner and moving to the center, a fifth man was added if the front or rear was to be painted. This seemed to be the right amount of area for everyone. If anyone was done too soon it meant they missed something and went back and did it again (which was rare after awhile). At the two hour mark they all tacked off the dust, by the time I did the final tack check the painter was in the booth, hooked up to his air and loaded. He was pretty much on the trigger as we walked out for a well-deserved coffee break. The race was over and the rest of the job was routine (unless someone sanded through the primer which needs immediate attention.)
For anyone in the business this is not convenient but charge and schedule accordingly, both stainless steel and aluminum are risker to coat than steel, but knowing how to tame the beast reduces your risk to near zero. If two hours seems extreme, it isn't: this self-repairing oxidization process is quick. Scuff in the afternoon and paint the next morning you are toast -- it will fail. To see this, scuff a scrap of stainless wait a few hours and then scuff one half of it. The colour will already be a little different.
I really hope this helps all you painters and powder coaters out there as I think it is the same problem appearing with both processes.
Canadian Intercity Coach - Calgary Alberta Canada
Q, A, or Comment on THIS thread -or- Start a NEW Thread