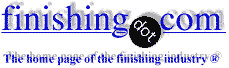
-----
Phosphate bath time
I have a dip system for running parts through a cleaning process and a calcium modified zinc phosphate bath what is the stanard time should parts be in the phosphate bath.
Joe Baird- Morganfield, KY USA
2000
First of two simultaneous responses--
If you have to conform to a weight standard, you will have to experiment with times to conform with the standard. We obtain a 300-400 milligram weight in about 4 minutes. Temperature and bath condition are important of course and checking your weights daily will QC the bath to some degree. Don't forget to clean the scale from your heat source regularly.
Dan Weaver- Toccoa, Georgia
2000
Second of two simultaneous responses--
Joe - There is no defined standard time for a zinc phosphate dip, because it depends on your particular process. The time range can run anywhere from 30 seconds to 15 minutes. Your coating weight requirement will be the final determining factor. Have your chemical vendor do some testing to find out how long it takes to meet your spec.
Dan Brewerchemical process supplier - Gurnee, Illinois
2000
Barrel processed parts take longer than coils in general up to 15 minutes. Excessive time does not offer much advantages. Weight vs. dwell time curves usually peek and then drop off in coating weight slightly with excessive time.
Calcium modified zinc phosphate baths produce a fine crystal and are not going to produce the same coating weights as the unmodified baths they are also known to leave tenacious cement-like deposits on heat exchangers. The loss of heat can slow the generation of nitrite and cause the bath to flip to the iron side. Cleaning/damaging/replacing heating coils is one of the hidden costs of running a calcium modified zinc phosphate bath.
Tony CangelosiFreiborne Industries - Pontiac, Michigan
2001
Q, A, or Comment on THIS thread -or- Start a NEW Thread