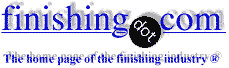
-----
Mil-A-8625 Type 1 vs Type 1B
Q. We are a small aerospace finishing company. We do chromic acid anodizing, chem film, prime and paint. Our main customers are Boeing and Lockheed. One of our approvals is for Boeing for Mil-A-8625 Type 1 Chromic Acid Anodizing. Our rectifier will really only do the 20 ± 2 volts that is called out for the Type 1B. We recently received a write-up from an auditor because our internal planning calls out for Type 1B plating, but some of our customer PO's call-out for Type 1.
There are some here that are convinced that the Type 1 requires 40 volts. After reviewing the Mil-A-8625 specification, I can not find any reference to a higher voltage for Type 1. I can't automatically assume that because Type 1B specifies low voltage, that Type 1 is a higher voltage. Both the Type 1 and Type 1B have the same testing requirements. Can someone please clear this up? Is there a voltage difference between Type 1 and Type 1B?
Kathi BittickQuality Planner - Lewisville, Texas
2007
Q. MIL-A-8625 Rev F specifies that Type IB coatings are produced by a low voltage chromic acid anodizing process run at 22 V, while Type I coatings are conventional coatings produced from a chromic acid bath. Many aerospace primes draw a distinction between 22 V processing and 40 V processing, but Type I coatings do not seem to be limited to any particular voltage level. This being the case, can Type I processing be done to the parameters of Type IB?
Our experience indicates that the 40 V process has much more difficulty passing the salt spray test than the 22 V process does (especially given the added requirement of no patchy grey areas stated in Para. 3.7.1.2c, that most aerospace primes do not require), so is there any need for us to ever process parts that require per MIL-A-8625 using a 40 V process?
On a related note, what is the advantage of 40 V processing over 22 V processing?
Thank you,
Aerospace - West Babylon, New York
May 1, 2013
A. If your 40 volt anodizing is failing salt spray then you are probably high in trivalent chromic acid as a result to too high cathode area. Statistically speaking the 40 volt should pass salt spray more often than the 22 volt.
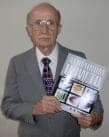
Robert H Probert
Robert H Probert Technical Services

Garner, North Carolina
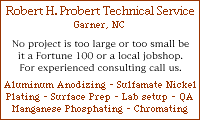
May 3, 2013
Q. Thank you.
Customer specs allow 5.4-7 oz/gal hexavalent chromium and up to 13.4 oz/gal total chromium. Would the high end of that range put us in danger?
Customer specs lock us into using 2024-T3 panels for the salt spray test. MIL-A-8625, Para 3.4.1, prohibits the use of the conventional process for the processing of high copper alloys, but appears to allow the use of the 22 V process on these alloys. Does the latter process handle high-copper alloys better than the former, and would our need to run the salt spray test on 2024-T3 recommend other precautions to be taken?
Thanks,
Aerospace - West Babylon, New York
May 7, 2013
Q, A, or Comment on THIS thread -or- Start a NEW Thread