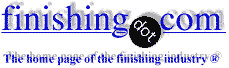
-----
Anodizing/black dye problem on 2000 AL alloy
Q. We are processing 2000 series alloy and when is dyed "white spots" and "pits" come up. this hapen with this specific alloy only and not with others like 6000 series.
Please, can someone tell me what considerations should I have when Cu alloys are being anodized?
anodizing plant - San Jose, Costa Rica
2007
A. Many intermetallic compounds form during initial solidification of 2000-series ingots. These intermetallics such as CuAl2 should be broken up and largely dissolved by proper solutionizing heat treatment and mechanical deformation (rolling, extrusion, etc.). As (most) intermetallics do not anodize, they create defects in the anodize coating, causing a less dense, softer coating. If the intermetallic particles are larger than ~1/2 the anodize thickness, the anodize coating cannot self-heal. 'Pimples' may occur as the anodize is held up by an intermetallic particle whilst anodize growth continues elsewhere. The stressed anodize eventually cracks, acidic electrolyte enters and preferentially corrodes the aluminum surrounding the intermetallic particle, which may fall out. Acid and corrosion products in the defects leach out during dyeing to create the white spots.
This is a material problem. Sometimes, burnishing or shot peening the surface prior to anodizing will break down intermetallics within the outer material to a harmless size. This procedure is used by aerospace.
Anodizing problems can also occur with leaded alloys and alloys overheated (to above the eutectic temperature) during solutionizing.
What is the particular alloy, temper and form?
- Goleta, California

Rest in peace, Ken. Thank you for your hard work which the finishing world, and we at finishing.com, continue to benefit from.
2007
A. I completely solved this problem on the site by taking the parts off the titanium rack and hanging onto aluminum wire for dyeing. The rack was titanium, the tank stainless steel and that equals over one volt of pit causing galvanic voltage especially on 2000's every time.
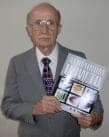
Robert H Probert
Robert H Probert Technical Services

Garner, North Carolina
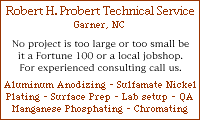
2007
Thank you very much Mr. Probert for your help and support and hope to see you more often in Costa Rica for many years.
- San José, Costa Rica
2007
Q, A, or Comment on THIS thread -or- Start a NEW Thread