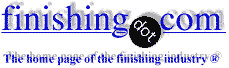
-----
Oxidation on Aluminium Pressure Die Castings

Q. Dear Sir,
We are shipping pressure die castings in machined condition which are getting oxidized in transit . Oxidation is only on non-machined surface and never on machined surface
1 The grade chemical composition of the castings as LM-24 AlSi8Cu3 (Fe)(Zn) with the following chemical composition:
Copper 3 to 4
Mg 0.30 Max
Si 7.50 to 9.50
Fe 1.30 Max
Mn 0.50 Max
Ni 0.50 Max
Zn 3.00 Max
Lead 0.30 Max
Titanium 0.2 Max
Aluminium Balance
2 The mold release agent used is Water Soluble Die Lubricant having
Petroleum Oil 4.5%
High Pressure Additive 7.90%
Synthetic Oil < 1%
Synthetic Polymer Compound 3-4%
Emulsifier 1-2%
Biocide < 1-2%
Water : Balance
pH: 8-10%
Density 0.99 cm3
Evaporation Rate/Vapor Density/Vapor Pressure same as water.
3 Coolant used for machining is Servo Cut 'S' having the following details:
5% Oil mixed with water to form a white liquid used for cutting.
Castings are getting oxidized on un-machined surfaces only.
4 Packing is VCI Sheets/bags which prevents oxidation during sea shipment and then paper ply partitions inside a wooden case.
5.Castings are kept in open without packing at least one week after machining.This oxidation problem does not occur always but at frequent times, not in 100 % quantity but in part quantity.
6.Time that the castings will remain inside box is 30 days and on board of a ship is 21 days.
I request help to let us know why this oxidation and what should be done to prevent
Thanking you,
manufacturer - Bhavnagar, Gujarat, India
2007
"Alodine" is a Henkel trade name for their chemicals for MIL-DTL-5541 [⇦ this spec on DLA] Chromate Conversion Coating of Aluminum
A. If you do Alodine on aluminum die castings after the pretreatment then you can avoid oxidation of aluminum. Another solution of protection of oxidation of aluminum die casting is anodizing.
Vikas Shrama- Gurgaon, Haryana
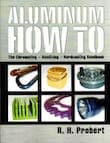
Aluminum How-To
"Chromating - Anodizing - Hardcoating"
by Robert Probert
Also available in Spanish
You'll love this book. Finishing.com has sold almost a thousand copies without a single return request :-)
A. There are many causes of Oxidation of castings:
1. The material storage near rain after casting.
2. Quality of Oil in your Mold release agent.
3. Quality of water diluted with release agent and cutting oil. Use DM water or soft water for both application.
- Gurgaon, India
A. According to my experience the oxidation is caused by cutting coolant. (called bio-corrosion). You have to control bacteria growth.
tommy kurnia- Indonesia
March 13, 2010
Q, A, or Comment on THIS thread -or- Start a NEW Thread