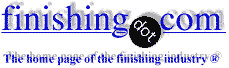
-----
Bright Nickel Plating Problems
Q. Hello,
My company is currently plating small brass parts with bright nickel. We are using brand new 12" x 24" Sterling barrels with large square holes (.22" non-mesh openings). Our rectifiers are capable of pulling 24 volts. Our nickel bath is monitored daily and all reports say that it is operating within the correct ranges. Hull Cell
⇦ huh?
s show no sign of problems.
The main dilemma we are having is that when we exceed 12 volts the parts come out with white rings on them. I say rings because they are bright on the outside and bright in the middle, not a solid white spot. If we lower our voltage to 12 or under then the rings disappear. I have no idea what these rings truly are and why there appears to be a magical voltage number. The rings are random with some parts having more than others, and there does seem to be some correlation between mesh sizes. The larger the mesh size the larger the ring. Oddly, we are able to run at higher voltage (15-16 volts) in smaller barrels with closed mesh (.02" nominal openings) without the white rings. We do not experience white rings on rack plated parts. Does anyone know what these rings are and how to eliminate them?
The obvious answer is do not plate over 12 volts, but that means we have to plate at very low ASF (1-2 ASF!) which causes more headaches. This leads to our second problem. We tried to reduce our voltage by increasing the size of all our copper bussing and center-bars in an effort to lower resistance. Bath analysis shows everything is in-line as far as metal concentrations and nothing on the tank or barrel is getting hot.
Nothing we did seems to help since the voltage remains the same without an increase in amperage. However, when we plate a dummy panel we can max out the rectifier using only 7-8 volts. If we max out the rectifier with a barrel the volts jump to 18-19 which again causes white rings. Is it normal to have to pull so many volts with a barrel?
We have been trying to solve these problems over that last couple of months to no avail. It is starting to really effect production. Any insight and recommendations would be greatly appreciated.
Sincerely,
Plating job shop employee - Erie, Pennsylvania, USA
2007
![]() |
2007 A. Hey Joe, Process Engineer - Syracuse, New York A. It is the sign of burning. your voltage is too high, same to same current density is too high. As it is barrel, it is sure related to the mesh-size. - Singapore 2007 |
Q. Thank you for the responses.
John, we also believe it is probably some kind of burn. However, we normally relate burns to too high of amperage. Burning at such a low asf is new to us. The job is basically a flash of nickel for appearance sake, so we have not done an in-depth thickness study. The readings we have taken seem to be in line with the ASF and time we are plating.
Thanks for the suggestions Mark. We have taken readings of the amperage on the anode and cathode bars and they are right in line. Everything is clean and rated properly. The anode to barrel spacing is around five inches. Everything "appears" to be in order.
We have tried using a slow motor (28 rpm) and a fast motor (57 rpm) with little difference in the results. One thing we have noticed that is a concern is there appears to be foam in the barrel when we unload it. It cannot be an air problem because we have tried turning off all pumps and filters and the foam is still present. Unfortunately I cannot tell if there is foam in the barrel while it is plating or if it is just being picked up in the dragout.
Thanks for the suggestions and any more insight would be appreciated. I guess life would be boring if everything went right.
- Erie, Pennsylvania, USA
2007
A. All of the above advice is good, check it out first. Then realize that in barrel plating you start by assuming that 1/3 of the parts are making contact and facing the anodes at any one time, so you use 1/3 the current density and three times the time; then you adjust up or down from there.
If none of the above comments fix the problem then (1) make sure the anodes are not polarizing and adjust the halogen and pH, (2) then raise the metal content to 14 or 16 oz/gal.
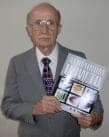
Robert H Probert
Robert H Probert Technical Services

Garner, North Carolina
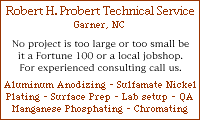
2007
A. Yes, your cathode current Density is not high at normal condition, I think this time it is passivated anode or improper anode bag mesh size to cause the burn.
If the anode is lack of service, it will be gradually passivated, the voltage will go up even though the current density remain the same.
if the mesh size of anode bag is too small, although it is good to contain the slug from the anode to go into solution, it will also make the ions dissolved from anode difficult go into solution in case of lack of service.
Do a fully service of your anode, then if possible, do not use anode bag temporary to do trial run to see whether the voltage would go down while you maintain your current density the same as before.
- Singapore
2007
Q, A, or Comment on THIS thread -or- Start a NEW Thread