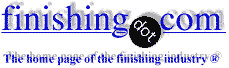
-----
Cleanliness of rinsing water after sulfuric acid cleaning of Nickel?
Hi,
My name is Anders, I am involved in the development of thin-film solar cells on structured steel substrates. As part of the process we use a layer of electroplated nickel to smoothen the surface. The samples are then moved to a subcontractor at another site and thus the Ni is allowed to oxidize. Here the nickel is cleaned in a 10% Sulfuric acid solution followed by a rinse in particle filtered tap water followed by a DI rinse.
I was quite surprised by the use of tap water and asked why - the answer left me in the dark still: Apparently the calcium of the tap water is supposed to neutralize the acid, which they were convinced could not be done with DI-water. Following the water rinses the pieces are blow dried (nitrogen) and mounted in a PVD chamber for aluminum sputtering. On top of this aluminum the solar cell is then made, so the cleanliness of the rinse after sulfuric acid is critical. We have some issues with holes in our coatings and since the rinsing raised my eyebrow I would like to know more.
Can someone help me out here, is it really a recommended rinsing process or can something else be recommended?
Best regards
Anders
R&D Engineer - Taastrup, Denmark
2007
2007
The explanation is almost entirely wrong; a 'plastering over' of the facts. Water is for rinsing, not neutralizing strong acid.
Neutralizing 1 volume of 10 wt% sulfuric acid with tap water containing 200 ppm of Ca(+2) would require about 218 volumes of water
(360 volumes water if 10 vol% sulfuric acid).
Perhaps worse, neutralization produces calcium sulphate dihydrate
(gypsum), which has a very low solubility. In 10 wt% sulfuric acid, scaling may occur at Ca(+2) > 10 ppm. sulphate contamination can remain after the DI rinsing -- dissolution of 1 part by weight of CaSO4.2H2O requires 400 parts DI water and may be slow. Perhaps such rinsing is tolerable when reactivating a nickel surface for further plating from acidic solutions. It cannot be good for your process.
If the rinsing cannot be improved, use hydrochloric acid solution to clean the nickel, as calcium chloride is ~400x more soluble than the sulphate.
- Goleta, California

Rest in peace, Ken. Thank you for your hard work which the finishing world, and we at finishing.com, continue to benefit from.
Q, A, or Comment on THIS thread -or- Start a NEW Thread