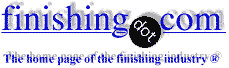
-----
6061-T6 Panels Fail Salt Spray after Treatment with Alodine 600
Q. Hello All,
We are an aerospace processing facility that utilizes Alodine 600 for our chromate conversion coating needs. Recently we have experienced off and on failures (3 out of 6 testing cycles) of 6061-T6 for both class 1A & class 3 per
MIL-DTL-5541
[⇦ this spec on DLA]. We are diligent in the preparation and post treatments of the processed coupons with extensive flow down of requirements of the process to all applicable personnel. These failures are extremely vexing due to the amount of care and attention to detail associated with the processing. We even go to the lengths to map out any suspect indications observed on the coupons prior to treatment. We carefully store the panels in an temperature controlled environment and the panels are laminated with mylar so as to protect the surface integrity. Our solution analysis results are well within parameters, but we cannot explain the recent rash of failures. Please note that the 6061 panels pass successfully through the chromic anodize tests for corrosion resistance. It is just the Conversion coating for 6061 we are having issues with, the submitted 2024 coupons for both classes are fine and exhibit no pitting.
My question is this; is there any objective evidence that the adhesive used on the mylar film can degrade the 6061 panel surface so as to cause failure during the corrosion resistance testing?
If anyone has an answer, please feel free to give your input to me on what may be occurring. Thank you.
Thank
Quality Manager - Lewisville, Texas
2007
![]() |
A. If you search this site, 99% of the recommendations are to throw away your panels and get brand new ones. Something happens to the surface chemistry as aluminum ages. If you keep using the same lot of panels, your fail rate will increase. James Watts- Navarre, Florida 2007 A. I'm fairly sure that the protective film on test panels uses a non-injurious adhesive. - Goleta, California ![]() Rest in peace, Ken. Thank you for your hard work which the finishing world, and we at finishing.com, continue to benefit from. 2007 A. You need to call in your supplier, meanwhile, try another source for the panels and inspect the panels for pits with a 10X loop before chromating. ![]() Robert H Probert Robert H Probert Technical Services ![]() Garner, North Carolina ![]() 2007 |
A. It is unlikely the protective wrapping is causing failure unless you are going straight from unwrapping to the Alodine bath. If you are using a caustic cleaning process followed by an acid deoxidizing process prior to chemical conversion -- a small amount of surface has been removed from the panels. So long as you attain a water break free surface after cleaning and prior to chemical conversion it would be moot if it were degrading the surface as the degraded surface would have been removed.
Test your Alodine 600 for sulphate and chloride contamination - keep it under 400 ppm. Henkel suggested you could potentially see salt spray failures over 15 ppm phosphate contamination. This is good to know as some parameters might have the high limit set to 25 ppm.
The bath should also have a certain level of Fluoride in it to work properly as well. Have your bath tested and call your Henkel rep to see what the target should be.
Lastly, you are not alone in this dilemma. It IS vexing. If we come up with something spectacular and brilliant - I'll let you know. If enough people throughout the country admit they are having SS failures with Alodine 600 - I might focus on the product being the failure mode.
- Seattle, Washington
2007
A. Hi all -
My experience has been that this problem will be most difficult when using an iron based deoxidizer. If you can use a chromated deox it should be easier to pass.
- Auburn, Washington
2007
A. Update!
Although our passes have been nominal, and our failures miserable, we have found what seems to work, and what doesn't at all.
The key is removing the natural oxide coating from the test panel without going too deep into the base metal prior to Alodine. There is no set times, you have to find what the 'sweet spot' of your chemistry is. If you skip alkaline etch altogether, extend your acid deoxidizer times a bit. Try another set with a little etch and shorter deox. Be sure to look at your panels prior to process (10X loop is best) as the panel starting with pits will certainly end with pits.
The key is not to focus on 'why' - you'll go mad. Send several sets into salt spray with a wide variety of process times and parameters, whichever set(s) passes becomes the way you certify your work to.
There are enough people in this area now having troubles with Alodine salt spray that there is a little comfort knowing we are not alone.
- Seattle, Washington
2007
Q. Surtec 650 treated aluminum panels failing Salt Fog test
Q. Hello, I work for a small metal finishing company in Michigan and we are completely stumped on an issue with Surtec 650.
We are running 2024 panels and 6061 panels to the MIL-DTL-81706B spec by the immersion method. Our tanks are well within pH and temp. ranges when panels are being ran. We have constant overflow rinses and are very careful with the times that the panels are in the tanks.
Once the panels have been ran, they are put into our salt fog test cabinet to run for the 7 day test, but the panels often fail within the first couple days. At the end of the 7 days, the panels come out with very large pits and it's very obvious that they have failed.
Is there a common reason why Surtec 650 panels fail and is there any easy things I can try to remedy this?
P.S. I just found this site and think it will be an awesome resource. Thanks for your help.
Plating shop employee - Jackson, Michigan, USA
February 22, 2014
A. Hi Scott. We appended your inquiry to a thread about 6061 panels rather than to one of our dozen threads about 2024 panels because every once in a while the failure of 6061 panels is actually related to the process -- whereas it's essentially unheard of for the failure of 2024 panels to be related in any way to their processing :-)
As Robert suggests and implies, throw away your test panels, get several sets of new test panels from various vendors, and get back to us if you're still having trouble; but there's a good chance you'll be fine. Salt spray testing of chromate conversion coated aluminum test panels is only a joke, and must be accepted as such or you'll go nuts. Good luck.
Regards,
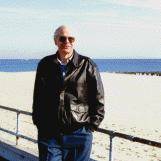
Ted Mooney, P.E.
Striving to live Aloha
(Ted can offer longterm or instant help)
finishing.com - Pine Beach, New Jersey
February 2014
A. Hi Scott, what kind of salt fog tests did you perform? NSS or AASS?
Davey ShawShenzhen, Guangdong, China
February 23, 2014
Salt spray result on 6061 T6-51 with chemical conversion per MIL DTL 5541 Type1 Class3
Q. One of our products was subjected to salt corrosion test as per MIL-STD-810 [⇦ this spec on DLA] F for 96 hours. Raw material is Aluminum Al 6061 T6-51 We have observed decolorisation as per the photo:
(Click graphic for hi-rez version)
Please let us know whether it is corrosion and what type of corrosion? We would be grateful if you could tell us the type of corrosion and what could be the root cause. How to prevent it from occurring.
Employee - Quality Control - Chennai Tamil Nadu, India
March 24, 2016
A. Good day Nandaki.
Google "rainbow" on this site.
There is a lot of good info.
Regards,
Aerotek Mfg. Ltd. - Whitby, Ontario, Canada
April 1, 2016
November 2, 2017
Q. I have been struggling with getting visually passing coupons samples.
I am processing two Alloys 6061-T6 and 2024-T3 .032 x 3" x 10" premium prepared panels to pass the MIL-DTL-5541F Class 3 requirement.
I process four sets of coupons, Qty five (5) of each alloy 6061-T6, 2024-T3 for 168 hour Salt Spray, Contact Resistance testing and process two (2)of each alloy for Paint Adhesion testing.
These coupons are processed using sst film clips and all 14 coupons are processed at the same time.
The 2024-T3 Alloy looks great as it should, no signs of smut and appealing finish.
The 6061-T6 coupons are streaked and have surface smut on them, the finish is not appealing. The streaked surface is lighter in color as well.
The coupons are not processed thru the etch. This step is reserved for extrusions and welded assemblies.
I have mechanically removed the Oxide layer on the 6061-T6 panels with abrasive pad then processed thru the Wash, Rinse, Spray Rinse, 1200S, Rinse and then Spray Rinse with great results.
The Deox is my focus.
Any recommendations of how to proceed to get better results?
Our Line is as follows.
CHEMICAL FILM PER MIL-DTL-5541 CLASS 3
MATERIAL: 6061-T6, 2024-T3 Aluminum
PROCESS CHEMICAL & CONCENTRATION TIME Degrease C-AK 6849 14% per/vol H2O 5 Min. Dip Rinse DI Water 15 Sec. Spray Rinse DI Spray Water 15 Sec. Etch SD-1 Granules 5.3 oz/gal N/A Dip Rinse DI Water N/A Spray Rinse DI Spray Water N/A Nitric Deox C-IC 6MU 10% Nitric & 9% C-IC 6MU 5 Min. Dip Rinse Cascade DI Water 15 Sec. Dip Rinse Cascade DI Water 15 Sec. Spray Rinse DI Spray Water 15 Sec. Chem Film 1200s 90 Sec. Dip Rinse DI Water 15 Sec. Spray Rinse DI Spray Water 15 Sec.Kurt Krueger
- Lexington, Massachusetts
A. Kurt
I would first look at the sst clips. Have you tried an aluminum rack? If you process a panel by hand (no rack) do you get favorable results?
- Green Mountain Falls, Colorado
November 10, 2017
A. Has that abrasive pad been used on any other metal than aluminum? Is the pad abrading other metals into the soft Kleenex-like aluminum? Did you inspect the panels with a 10X loop to look for pits and scratches?
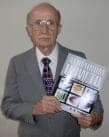
Robert H Probert
Robert H Probert Technical Services

Garner, North Carolina
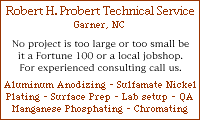
November 11, 2017
November 13, 2017
Good Afternoon Ted Mooney
Thank you for this forum.
Attached are the photos that go with the initial question and process posed last week.
... the coupon made out of the Alloy 6061-T6.
... the coupon made out of the Alloy 2024-T3.
... both sets of coupons side by side.
Thank you,
Kurt
- Lexington, Massachusetts
November 13, 2017
Q. Good Afternoon Willie
Thank you for your input. I have processed one 6061-T6 aluminum coupon by double gloved hand. No Rack. The results were still less than desirable. The process steps were the same as listed previously,except no rack was used.
Last week I a ran a series of additional testing. My variable was the immersion time in the Deox. Still using a 6061-T6 test panel.
Immersion time of 2 minutes,3 minutes and 4 minutes was my variation. All three showed the same washed out streaky look. I do not believe these are of visual passing quality to send out for salt spray analysis.
I then processed two 6061-T6 coupons thru the same 140 °F DI Immersion Wash, DI Immersion Rinse, DI Spray Rinse, then 2 minute immersion in 140 degree Sodium Hydroxide at 40 g/l solution concentration, DI Immersion Rinse, DI Spray Rinse, then one coupon was immersed for 30 seconds C-IC 6MU Deox and one for 60 seconds. Then the same final steps DI Immersion Rinse, DI Immersion Rinse, DI Spray Rinse, 90 second 1200S immersion, then DI Immersion Rinse, DI Spray Rinse.
Both of the coupons processed thru the Sodium Hydroxide looked better than any previous results with the 60 second Deox immersion variation looking the best. The results of this testing look good enough to send out for salt spray, resistivity and paint adhesion testing.
I am still at a loss for why the 2024-T3 coupons were not showing similar visual streaky, washed out look.
Thank You all for your responses.
Kurt
- Lexington, Massachusetts
November 13, 2017
Q. Good Afternoon Robert
Thank you for you interest and input. In response to your inquiry:
"Has that abrasive pad been used on any other metal than aluminum? Is the pad abrading other metals into the soft Kleenex-like aluminum? Did you inspect the panels with a 10X loop to look for pits and scratches?"
The premium test panels were processed with a(new)never used red(Trade Name)abrasive pad.
After the abrasive pad treatment these panels were visually inspected under 10x magnifiers the panel looked uniform and no visual imbedded particulate.
Then the panels were Washed in the C-AK Immersion product, 15 sec DI Immersion Rinse, 15 sec DI Spray Rinse.
Then the 90 second Immersion in the 1200S Chromate, DI Immersion Rinse and finally DI Spray Rinse
These test panels had no issue. The chromate looked great. These part would most likely pass the salt spray, resistivity and paint adhesion if I tested them.
So this tells me the 1st and last chemistries are working as designed.
The Deox chemistry is suspect.
Thank You
Kurt
- Lexington, Massachusetts
November 16, 2017
A. Your pretreatment process sounds okay, but pictures look like a too thin chromate coating.
Clean/etch a bit more aggressively, make certain your deox is up to snuff, and chromate for a bit longer time.
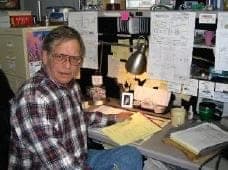
Jeffrey Holmes, CEF
Spartanburg, South Carolina
December 6, 2017
Q. Gentlemen,
Thank you for your past tips and comments regarding the challenges I have faced chromate conversion coating on 2024-T3 and 6061-T6 Aluminum coupons.
I wanted to give you an update.
I have discovered the DI water to be my issue.
Past Finishing.com Forum discussions hinted on this problem.
What's happening on the surface of the coupon:
When the aluminum product is exposed to the Nitric Acid Etch the surface of the aluminum is stripped of the +(positively) charged oxide layer making the surface active or -(negatively) charged.
When the tap water rinses and dilutes the nitric acid surface chemistry, the inert positively charged calcium, silica, manganese and other dissolved minerals(salts)that are present and in higher concentrations in tap water are attracted to the surface. These inert ions allows the surface to remain active.
Then the chromate solution displaces the inert minerals creating the passive surface.
DI Water:
When DI resin initially enters the deionization process, it holds onto positively charged hydrogen ions (H+) and/or negatively charged hydroxide ions (OH-). Then, as water passes through the resin beads, all the other ions (calcium, silica, manganese and other dissolved minerals) stick to the resin, dislodging either the hydrogen or hydroxide ions. This process is known as "Ion Exchange"or "Deionization".
At the end of the process, we're left with water that is absent of almost every charged ion except for "hydrogen hydroxide" or pure H20.
pH ~ 5.0
Lack of ± ions in DI water:
Increased concentration of dissolved carbon dioxide (CO2) as soon as the filtered water is exposed to atmosphere.
Leads to carbonic acid (H2CO3) in DI water
This means: increased concentrations of protons H+
H+ in carbonic acid (H2CO3) in DI water attacks and reacts with the activated deoxidized surface attracted to the newly active or negative surface.
Tap Water:
pH ~ 9.0
Lots of negatively charged hydroxide ions (OH-) and less H+ present
The OH- ions do not attack the deoxidized surface, preserving the surface chemistries for the next step in the process allowing the chromate solution to properly adhere.
Question:
If we are treating our combined cascading rinses (wash rinse, caustic rinse, nitric acid deox and hexavalent chromium 1200S) in a closed loop DI water system, can we post treat with calcium, silica, manganese and or other dissolved mineral salts (Possibly Water Softening Technologies) to create a controlled rinse water similar to tap water?
I understand this will be stripped out again in the DI vessels.This also would be creating the need for additional testing and consumables to be used. I am trying to create a closed loop system that is not discharging to drain like traditional flowing tap water rinses.
- Lexington, Massachusetts.
January 31, 2018
A. Dear Kurt
Looking at your panels it seems to me the following:
The 6061 panels look to pale with a thin coating even some areas do not have coating at all .
The 2024 panels look crimson color (too red-ish iridescent) , which points to the fact that the pH in the conversion coating bath is in the low range or maybe too low.
So we can conclude or can speculate that your coating weight is too low and this is the reason for your NSS failure.
For a first step, do a coating thickness test for the coating; the coating must be more then 0.4 grams per square meter.
Personally I don't like your oxide removal system, it must be fully controlled per etch rate.
YB Plating Engineering and Quality - Haifa ,ISRAEL
A. Hello Kurt,
I agree when you say your deox is suspect. How often do you do a full bath change? Do you have it tested for contaminants along the way?
During one of your posts you mention the conversion coating 'replacing inert materials' like silicon, calcium, etc. and from experience I can say that it's not *quite* like that.
Silicon from a dirty deox is a stubborn beast. Once it gets back onto the otherwise clean substrate, it wreaks havoc with conversion coatings, both hex and non-hex- long reaction times, shading and color variations, salt spray problems, etc. We run a lot of castings through a shared deox and I actually have quite a bit of data where I can correlate silicon levels near undetectable in the deox correlating to zero defects in conversion coating salt spray results, to starting to see the occasional pit on a test coupon around 20ppm, to a point where over 30ppm Si is treated like the first sign of impending apocalypse and we are all jumping into action to do a full dump and scrub the tank well before refilling it.
Also, what is the TDS of your city water coming in vs in the tank while in use? CaCO3 is the most prevalent mineral in a lot of surface waters, and what contributes most substantially to the TDS of the incoming water. You guys out there in Lexington (I'm from Lexington originally) get your water from Wachusett Res, and there are limestone deposits in that watershed... but it really shouldn't be an issue since they keep TDS acceptably low leaving the treatment plant, and calcium is a lesser evil anyway. Your enemy is Silicon, and it hides out in the deox :)
Good luck!
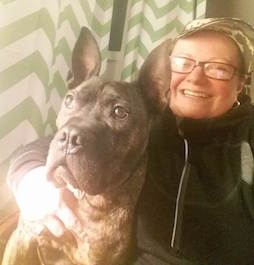
Rachel Mackintosh
lab rat - Greenfield, Vermont
February 12, 2018
February 13, 2018
Q. Good Morning Rachel
I greatly appreciate your input.
I started this project with hopes of certification as an end goal. Still a ways to go...
There are two topics of focus here specifically to Chromate Conversion Coating Process:
1.) The struggles to meet the MIL-DTL-5541F requirements for certain alloys (2024-T3) when attempting to pass Type 1 and Class 3 requirements (168 Hour Salt Spray, < than 5,000 microohms per square inch specifically) Paint adhesion has not been an issue.
2.) Creating a closed loop rinse water system that does not go to drain.
When you look at the specification MIL-DTL-5541F it lays out the requirements for Type 1 and 2. I am focusing on Type 1 Class 1a and Class 3 requirements.
I reviewed the testing required for both classes on two Alloys 6061-T6 and 2024-T3 and the Salt Spray 168 hours, Contact Resistance Testing and Paint Adhesion Testing requirements. I targeted the 2024-T3 alloy, Type 1 and Class 3 requirements as being the target to meet all testing requirements in one fell swoop.
When I first started the long road of testing all the requirements I did not know industry could not consistently and reliably supply 2024-T3 products passing Type 1 and Class 3 requirements. On the alloy 6061-T6 this is possible and I have succeeded. I have come close with the 2024-T3 but to date have not been able to pass both 168 hour salt spray and Contact Resistance Testing on the 2024 Alloy.
New panels, new batches of coupons have been used. With daily solution analysis testing using semi-automated titration system. I have not sent out bath samples for contaminant testing due to the length of service the baths have been in use and the load on them. Very little.
Then I find out that the industry may wave the salt spray requirement when low resistance is required thru work instruction.
The following are two documents I have come to review. Curious but still some mystery surround them.
1. SCOPE:
1.1 Purpose: This specification establishes the engineering requirements for
producing chemical-film coatings on aluminum and aluminum alloys and the
properties of such coatings.
1.2 Application: Primarily for aluminum and aluminum alloys where increased
corrosion resistance, improved paint adhesion, or a low-electrical
resistance coating is required . Also useful for improving the corrosion
resistance and paint adhesion properties of abraded or discontinuous
anodized surfaces of aluminum and aluminum alloy parts.
AMS2477 REV. A. 1. SCOPE
1.1 Purpose
This specification covers the requirements for a low-electrical-resistance chemical conversion coating on aluminum and
aluminum alloy parts.
1.2 Application
This process has been used typically to provide aluminum with a thin inorganic film that improves corrosion resistance
and adhesion of organic coatings and possesses low electrical resistance, but usage Is not limited to such applications.
So if I am producing 2024-T3 products to the Type 1 and Class 3 requirements; I do not need to test for contact resistance unless I am asked by my customer to meet and certify the contact resistance specification of < than 5000 microohms. And if my customer specifies they are waiving the salt spray requirements in favor of the low resistance requirement in written work instruction.
Is this a correct statement?
This information is not easily pulled from the MIL-DTL-5541F document.
Why is this not addressed in the main document if it is so elusive to achieve on this Alloy?
On top of this (to my knowledge) there is not off the shelf standard test equipment that you can buy to test for the Contact Resistance requirement. Every supplier or test house required to measure this requirement has one of their own cobbled together systems that measures resistance. I seems to me that an industry standard does not exist for this test equipment requirement.
In regards to the rinse water:
The system I am using was laid out to be closed loop on the rinses using a DI water system. The earlier post showed the struggles I faced because the DI water was passivating the active aluminum as it was rinsed before chromate.
The previous post was asking the industry has anyone in this day and age attempted to create a closed loop rinsing system. No water to drain. Using the Anion and Ion Exchange DI water system to remove the dilute, rinsed Nitric, HF and Hex6 from the rinse water of the Chromate Conversion Coating Process. Then replace the salts that have been removed with one target salt to raise the pH of the DI water and make it more neutral.(water softening technologies).
With the end goal here closed loop and controllable.
Does anyone have experience doing this?
Thank You
- Lexington, Massachusetts
February 13, 2018
A. Hi Kurt! Wow this is one of the best thought-out and explained questions I've ever seen on this site... And long ;)
Might be easier to work with by addressing the two sections in separate answer posts (but to say I have an answer is a gross overstatement, these are pretty good questions!).
Here goes... Let's talk about closed loop rinsing first, because I like this stuff, and I'm super bored running manual titrations all morning.
I think you will find that your biggest challenge is going to be making enough recycled water to fill your needs. Finding space for equipment, and a budget, are also great fun!
DI resin is certainly a good way to go for the final polishing of your water. Putting a heavy load of fresh, un-pre-treated, rinsings/dragout across a resin bed is going to foul it pretty quick, and then you have to pay for shipping the spent hex-contaminated resin as waste as well. I don't know what other processes you've got going in your facility, but if you have a number of different processes, some options to look at are:
- Making strategic use of sequestered (no flow through) pre-rinses to minimise loading in the flow-through rinses that you will ultimately treat. For example, giving your Hex tank its very own post-hex-tank-pre-rinse, starting with DI, that is just allowed to build up over time and then gets shipped as waste when it reaches a point you have determined to be 'too dirty to use'. The clean second DI rinse will be easier to deal with, having a lower contaminant load, and can just be recirculated through its own DI system.
- If you have other processes that are adding easily-treatable contaminants, such as a Ni-acetate seal and a bunch of anodize tanks, pretreating with traditional methods: pH adjust to flocc (make settleable hydroxides out of anything that will form them), run flocc through a Lamellar settler and filter press, and THEN 'polish' the effluent over DI resin. You're still not going to get out the Hex without reducing it to Tri first, and that's a horse of a different color because of the serious air quality issues arising from the reaction. So that would be the job for your DI resin. But cleaner water in means longer resin life. ***NOTE: I do NOT have experience treating HF contaminated water. You theoretically get Sodium fluoride, and that won't be caught in a Lamellar due to solubility issues. So off to the DI system with that, too...***
- I can highly recommend a resin for what you are trying to do; Lanxess NM-60 IX is a mixed-bed with a good working life and the level of crud removal is fine for our uses in this industry. If your system is scaled right for your flow-through, achieving the <5µS target and holding it over time is no problem. And it creeps before it crashes. I'm not a fan of the canister exchange services, being pricey and coming stuffed with quite often a mixture of virgin and regenerated resins with decreased life remaining, plus their hazmat shipping fees to take them back would make a used car salesman blush. There's a dude in Mahhhhshfield who sells pressure vessels and fittings and such, and another guy in New Britain who I'm quite fond of. IMVHO your own canisters are worth the investment. You just have to figure out how you need to scale the system.
- If you're treating with NaOH to pH adjust and then running through a Lamellar, the water coming out and then going into your DI system actually shouldn't be too acidic; you only really have to take it to about 7.5-8 to begin with, and the supernate will drop back down to the mid-6 range, at drastically reduced ionic strength, as hydroxides form, if you've got your dosing dialled in. So pH adjusting isn't so big an issue. I really don't know what you would do for the 'replacement' step at the very end. This is a question for someone who has a better metallurgical background; I'm just the lab rat. Heck, CaCO3 might be your magic bullet for all I know... But I'm not going to even hazard a guess as to what the ideal compound for addition of alkalinity without supressing conversion will be.
So. That all being said, I don't run closed-loop here. Our city water is super duper, at a consistent 60 ppm TDS, with occasional minor spikes during wet weather events, and we run it through a DI system for rinses that need to be cleaner. I have a Lamellar for waste pretreatment and don't try to reclaim out of it, though it is theoretically possible. The discharge is already nice and clean by State effluent standards, because our Hex process is sequestered and never has a chance to enter the waste stream. Reclamation is something I may well propose for the future, as we outgrow our discharge permit (and if our facility magically gets some more floor space...*sigh). These are just pieces of a puzzle that you can assemble to suit the specific needs of your shop.
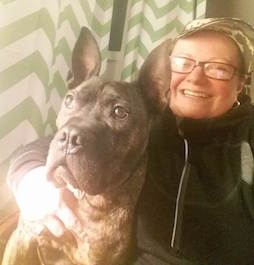
Rachel Mackintosh
lab rat - Greenfield, Vermont
A. Kurt's question, Part Deux!
Super brief because I haven't had a chance to look at those specs referenced in italics...
-The conductivity testing can be waived, and often is, and yeah the apparatus appears to be up to the user to assemble and prove to the auditor that it functions. Pro tip: A Fluke 1507 insulation tester, with some creative attachments, works like a charm.
-I've never heard of waiving the salt spray but that just means... I've never heard of it. They keep me caged up away from other lab rats and I don't get out much to have a good squeak over beers with the competition. Personally, I think salt spray testing is just as important for a shop's own information, since you can monitor your individual tanks, processing, etc. until you're blue in the face, but if something that isn't being tested (proprietary additives in a bath being depleted, for example), or some COMBINATIONS of factors that are all INDIVIDUALLY within limits, pushes your salt spray results into a danger zone, you can see it happening and start troubleshooting.
-The alloy you use for testing should reflect the bulk of the alloy you are processing, so if you barely see 2024, and process a TON of 6061... every auditor (AS9100, GE, Nadcap) we've had is content with that. I don't recall where that clause is buried in, sorry. But if you aren't actually running enough 2024 to require it as a test substrate, you may not have to tear your hair out over this to begin with.
Maybe someone from an Engineering and Compliance side of things can help more.
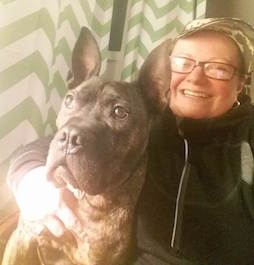
Rachel Mackintosh
lab rat - Greenfield, Vermont
February 13, 2018
February 14, 2018
Good Morning Rachel
I am fortunate to get such great input from you and others who have given guidance.
The system I am currently operating is small, 13 processing tanks with 60 gallon capacity. 4 of these are stainless processing tanks for the Wash, Caustic, Deox and Chromate. This system is a dedicated Chromate line. No other plating processes are required.
The rinses consist of 5 immersion rinses and 4 spray rinses. Each single tank immersion rinse is constantly flowing with eductors at the bottom of the tank keeping things moving and a level drain at the top returning this rinsate to the holding tank where it is recirculated through the DI water system. The Deox has the two counter flow rinse tanks.
I have proved through testing that the caustic etch is not required and parts processed thru the caustic do not pass salt spray tests easily. We have kept this process chemistry for heavy oxidation or stripping. I have not seen any value of keeping it.
Your thoughts on caustic?
So the dragout is primarily wash surfactants and light soils, nitric, HF and chromate. With the HF being in the proprietary mixture supplied by the manufacturer.
I am not processing the levels you are at. And my hat goes off to you and those who do....
So you were spot on with the CaCO3 being my first test of my post DI System addition.
This testing will be done in the 5 gal buckets with samples of pre treatment and post treatment CaCO3 rinse water being sent off to the lab for analysis. This will at least give me an idea of how much saturation of CaCO3 has been put into solution. With hopes the 50/50 Calcite and Corosex filter cartridge will provides the pH correction and some remineralizing. If my rinsing after the Deox shows rinsing results and not passivating the active aluminum I will be well on my way to fulfilling the closed loop system.
Currently my rinse tanks are static tap water. Not practical long-term, but passing salt spray. And the final rinse after the chromate still DI.
This has been an eye opener and I understand why the tap water rinses are used primarily for convenience and costs associated with maintenance and testing.
For now, more coupon testing...
Thank You Rachel.
- Lexington, Massachusetts
A. My thoughts on Caustic before conversion coating are the same as yours; if absolutely necessary, a very quick etch (like, SECONDS) is a good thing to have available for those times you need it. Customers sometimes like to drag stuff out of their warehouse and send it along in less-than-ideal condition! If we got in test coupons that had enough visible oxidation to warrant an etch, I'd send them back! But your deox is the real workhorse for that perfect prep.
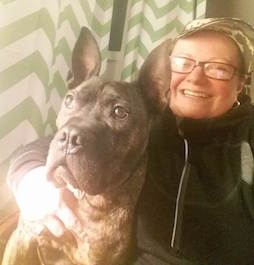
Rachel Mackintosh
lab rat - Greenfield, Vermont
February 19, 2018
March 30, 2018
Q. Thank You All for your past inputs and potential future experienced guidance.
I have successfully passed multiple salt spray, contact resistance and paint adhesion tests on both 6061-T6 and 2024-T3 alloys while using a closed loop DI rinse water in the wash step and following the chromate step.
The rinses following the Acid Etch (Deox) are static tap water. Three total, two immersion and one spray. Nothing is going to drain.
The challenge was to make this a closed loop process.
The DI filter beds are doing a good job with the Wash and Chromate rinses.
My last challenge is the Deox rinses.
Is there anything I can do to filter the rinse water from the Deox step?
If I use a combination of carbon filtration and 5 Micron sediment filtration that may remove the chromic acid in the deox solution. But what can I do to remove or reduce the Nitric Acid and HF Acid in solution of this rinse water?
From what I have read it is a complicated process due to this process chemistry becoming an azeotrope mixture after the initial make-up.
This turns into a combination waste water/ process question.
Because after a certain point the drag-out saturated rinse water becomes less effective at diluting the surface chemistry of the aluminum after removal from the Deox chemistry.
This then requires a titration step to the measure the drag-out concentration of the rinse water. Then set the limit to remove and refresh the rinse baths.
- Lexington, Massachusetts
A. You can pass all those tests with a proprietary deox that does not contain chromic acid. The industry standard ferric sulphate based products containing other mixed (but not chromic) acids daily pass those tests all over the world.
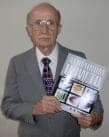
Robert H Probert
Robert H Probert Technical Services

Garner, North Carolina
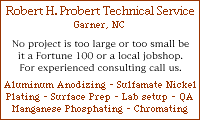
March 30, 2018
April 6, 2018
Q. Thank You Mr. Probert for the reply to my previous inquiry.
If you could elaborate on the proprietary product I would be interested in the possibly of testing this product...
In the last inquiry though I am focused on the rinse waters of this Deox step. Currently three rinse steps are used. The rinses currently being used are, two static Tap water immersion rinses and one Tap water spray rinse.
We have found DI water does not work well for the rinsing at the Deox step. We had cascading counter-flow DI rinses and DI spray rinse. This proved to be countering the active surface created by the Deox.
Now keep in mind we are not using a constant flow Tap water rinse, for the purpose of reducing water consumption. So the rinse water from this step gets saturated with Deox drag-out quickly. We are titrating the rinse water to understand at what point this rinse water becomes ineffective.
Adding the constant cascading counter-flow Tap water rinse would be the easy part. The waste treatment is what we are working on. The two static tanks are approximately 120 gallons solution total.
So back to my original question:
Is there anything I can do to filter the static rinse water from the Deox step?
Removal of Nitric Acid and proprietary constituents from another manufacturer's proprietary product from the static rinse water tanks.
From what I have read it is a complicated process due to this process chemistry becoming an azeotrope mixture after the initial make-up.
Thank you
- Lexington, Massachusetts
----
Ed. note: We try to avoid commercialism without getting in the way of information transfer; we don't object if Mr. Probert names the product he had in mind ... we just discourage both slams and glowing testimonials :-)
A. Hi Kurt,
Not sure if the mods will be okay with this ... one product that fits the bill is MacDermid Isoprep 184.
It contains Nitric and Sulfuric acids plus Ferric sulphate. It is designed for use with conversion coatings, but of course is not limited to that.
I'm sure there are others; it's a pretty simple formulation, but this is the one I have had success with.
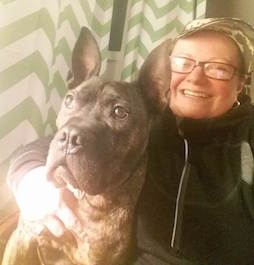
Rachel Mackintosh
lab rat - Greenfield, Vermont
April 9, 2018
----
Ed. note: Thanks Rachel. We don't mind if you offer or Robert Probert offer the name of a typical product ... as long as you don't claim one is better than another :-)
But for the record, other suppliers of aluminum etchants and chromates include Accu-Labs, Inc. [a finishing.com supporting advertiser] and Chemetall.
Q. Kurt,
Thanks for sharing your journey. I'm new to the subject and your discussion has been an eye opener. Question: If you actually switched to a tap water rinse following the nitric deoxidizer, how do you remove chloride ions from the tap water before using it for the rinse?
(https://www.pfonline.com/articles/aluminum-surface-finishing-corrosion-causes-and-troubleshooting)
- MONTVILLE, New Jersey, USA
June 5, 2018
June 5, 2018
A. Good Afternoon Barry
We are not specifically targeting or testing for the chlorinated salts or ions that are in the tap water. We may be indirectly eliminating the threat due to the method we process.
I know from the metal machining industry, that if you leave cutting fluid in a machine tool indefinitely and keep making up the the loss of evaporation with a low percentage make up the chlorinated salts/ ions will get to hazardous levels even oxidizing the machine tools. These levels are extreme.
Your plating processes are sensitive to elevated levels, I am not sure what that elevated level is. But it was my understanding if your shop has counter-flow and discharged to drain, the rinse water should never incur elevated chlorinated water levels.You are relying on your water resource to maintain this parameter.
The way we manage our chromate line is in the morning we decant off DI water used in the other closed loop counter flow DI rinse steps to replenish the heated wash and heated caustic etch.
Then we decant the primary Deox rinse into the holding tank to be processed thru our closed loop DI filtration system. Then we decant the secondary Deox rinse water to the primary and fill the secondary with fresh tap water.
We have pumped off our Deox tap water rinse tanks to waste drums and hauled away as hazardous waste once. This was for testing, but we have been getting passing results for 6 months now. with this replenish technique and daily titration testing.
I am waiting to see a test failure, then I can look at my Excel run charts and look for the indicator. I may not see the smoking gun, but I know what I have been doing to maintain this line for 6 months from its initial makeup. I would then go into detective mode and change one chemistry at a time. I would start with my rinse water and new lot of test coupons of both alloys.
I perform daily titration testing on the Chromate PH and Chromate Concentration, Wash Concentration, Deox Proprietary Concentration and Deox Nitric Concentration. I still test and keep the Caustic Etch as well but this tank is not used.
Note: My goal was zero rinse water discharge.
If you have thoughts on how to make this better I am all ears.
Thank you
- Lexington, Massachusetts
Q. MIL-DTL-5541 [⇦ this spec on DLA] color is white yellow between brown but it can be a color problem. Maybe sometimes it can be blue. Why?
Lewis baker- jamestown, rhode island
June 27, 2019
A. Hi Lewis, you are right that chromate conversion coating on aluminum can be clear, blue, or yellow, maybe even somewhat brownish (among other colors). These choices are often wanted and there is nothing wrong with any of them, although getting a mix of colors could be problematical.
Please introduce yourself and your situation so that we can answer better. Thanks.
Regards,
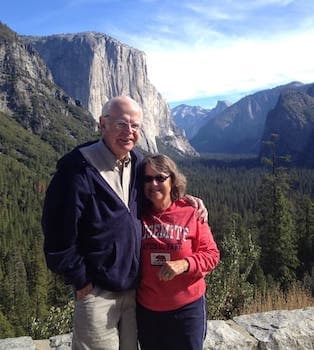
Ted Mooney, P.E. RET
Striving to live Aloha
(Ted can offer longterm or instant help)
finishing.com - Pine Beach, New Jersey
June 2019
Q, A, or Comment on THIS thread -or- Start a NEW Thread