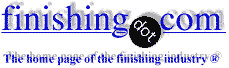
-----
Bead Blasting of Aluminum: Specifications
March 13, 2021
Q. Here is my dilemma. The company I work for runs thousands of parts for bright dip anodize on a daily basis, and we only run into this issue with one customer.
The parts are machined at one facility, bead blasted at another facility and ultimately we finish the parts with a bright dip anodize finish.
In the pics attached it looks like slight pitting that would be caused by the bright dip but when we significantly decreased bright time in half the pitting looked worse.
Could this be caused from the blasting? Maybe the blast media is contaminated? Any idea what it could be from?
Tony Latoya- Chicago, Illinois
A. Come back and tell us (1) on what else (like iron or brass) has the blasting media been used,
(2) alloy,
(3) heat treating.
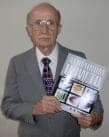
Robert H Probert
Robert H Probert Technical Services

Garner, North Carolina
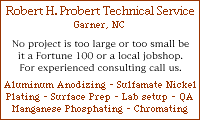
March 15, 2021
A. I am also curious whether incoming inspection is looking for this defect. I'm only looking at pictures, but to me it looks like the profile has been satisfactorily anodized and dyed, but the profile has some small round impression patterns in it from blasting with large beads :-)
Luck & Regards,
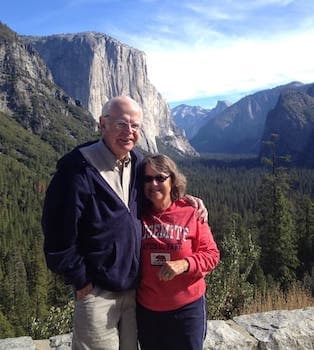
Ted Mooney, P.E. RET
Striving to live Aloha
(Ted is available for instant or longterm help)
finishing.com - Pine Beach, New Jersey
March 2021
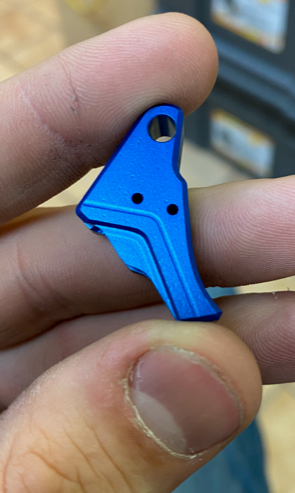
Q. Here is another picture. The alloy is 6061. I am not sure what kind of media is used or how they are heat treated.
Tony Latoya [returning]- Chicago, Illinois
⇩ Related postings, oldest first ⇩
2002
Q. We have been asked to bead blast some thin (1-2 mm) plates, hard anodised and dyed black. Without bead blasting, we achieve the colour no problem.
When bead blasted though, we 'achieve' grey!
I would have thought that a roughened, bead blasted (Al2O3) surface would scatter light more than a smooth surface and so would appear blacker and darker than a non-bead blasted surface. This does not appear to be the case. Any ideas why not?
We have compromised by bead blasting and briefly chemically brightening (Phosbrite 156). This leaves some texture but not as much as the customer would like.
Any suggestions as to how we can achieve a dark, black anodised surface after bead blasting would be much appreciated.
Thanks in advance.
Nick Winstone Cooper- Bridgend, South Wales, UK
![]() |
A. It sounds like your glass beads have been used on steel and you are pounding iron into the surface of the aluminum. Beads used on aluminum must be so designated for aluminum, and the night shift must not slip in and bead blast a steel car part or steel gun or any other steel. The beads must be for aluminum ONLY. Then to remove some silicon that is left behind by the broken glass, be sure to use some ammonium bifluoride in the deox. Take two aspirin and call me in the morning, ![]() Robert H Probert Robert H Probert Technical Services ![]() Garner, North Carolina ![]() 2002 A. With all the "peaks and valleys" you get with a bead-blasted surface, I would expect the opposite...more of an absorption of light. But at the same time ... a nice black coating is achievable. We have anodized a lot of bead blasted parts, although they aren't quite as black as a smooth surface. You didn't mention the alloy you are working with or the process parameters so its hard to give advice. ![]() Marc Green anodizer - Boise, Idaho 2002 |
A. Nick,
I think Robert is right on with the ammonia ⇦ on eBay or Amazon [affil link] bifluoride after blasting. I never had any luck achieving "black" after blasting without following up with a caustic etch and a few minutes in the ammonia bifluoride in a acid deox. If there are no tolerance issues, this would be the way to go. It evens out the appearance of the blasting as well.
MARK DEWITT- ROCHESTER New York
2002
A. Hello Nick,
As simple as it seems, Bead Blasting is a Fine Art! It sounds like you are in effect "burning" the material in the blasting process. The resulting splotches of contrasting color is very apparent after anodizing. Try lowering the pressure, blasting further away from the workpiece and using steady movement to achieve an evenly prepared surface. Remember, preparation of the substrate is 99% of the final product!
Bill Grayson- Santa Cruz, California, USA
2002
Mesh size for glass bead blasting?
Q. Hi!
When glass bead blasting aluminum, how can I get the brightest result, with fine media or with course? Can someone explain the differences?
Leif PensarFinishing - Stockholm, Sweden
2004
A. I won't pose as an expert here, but my experience with this is as follows: After the cleaning which may have been done at high pressure, do a blast polishing. This is done with very low pressure, I have found 1-2 bar optimum. Maybe the most important thing is to use new spherical glass beads, or at the very least use new glass beads, but spherical beads give a brighter surface. Size can be 400 (0.4 mm). I really can't tell whether small or large beads are the best. If you use siphon feed the low pressure required may cause problems with the pick-up tube and media feed .
Eirik Karlsen- Svolvar, Norway
2004
Q. Does anyone know of a specification that outlines finishes (or processes to achieve them) achievable by Glass Bead Blasting techniques?
We are looking for a way to visually quantify the appearance of the blasted surface (aluminum)for cosmetic purposes. Some time ago, we developed a system at Tektronix, that outlined Bead size and pressure, but alas it is gone.
design industry - Balmain, NSW, Australia
2007
Q. I am looking for exactly the same sort of standard or specification for controlling the appearance of bead-blasted, color-anodized aluminum components. Barring the availability of any industry "standards", what type of drawing notations or process specifications have been successfully used to help promote uniform appearance of bead-blasted, color-anodized aluminum components?
Any comments are greatly appreciated.
Best Regards,
digital cinema - Lake Forest, California
January 4, 2010
A. Scott,
Due to the process variables involved, I would suggest establishing reference standards that production parts can be compared to. If you detail the entire process, you may eliminate some competent suppliers if their developed recipe is slightly different from your requirements, even though their results are acceptable. Colored, textured anodize has to be the most difficult process to control because there are so many variables that effect the final finish. Expect to pay a premium for a quality supplier.
- Colorado Springs, Colorado
January 11, 2010
Multiple threads merged: please forgive chronology errors and repetition 🙂
Is Bead Blast finish possible on aluminum
Q. I am reading a specification for a bead blast finish on an aluminum channel. Can this be achieved? Can it be applied to an extrusion or does it need to be applied to a sheet and then formed into a channel after finishing?
Joe Bandyproduct designer - Waynesboro,Virginia
February 3, 2010
A. Answer is yes and no. How much money can you spend on a proper blast system or how uniform of a finish do you want?

AF Kenton
retired business owner - Hatboro, Pennsylvania
February 5, 2010
Aluminum bead blasting and anodizing satin finish
November 15, 2012Q. Hi,
I work for a small company that designs and builds scientific imagers used in auroral and atmospheric research. Traditionally all of our aluminum machined parts were just machined and then black anodized. While this works fine, it really doesn't leave the surface finish that I would associate with a professionally produced product. There are machining marks on the exterior of the devices which in my mind really take away from the product. If I were the customer paying $150k+ for this imager, I would want it to have a very nice appearance.
After a lot of research and talking to people I learned that by bead blasting our parts before anodizing we could remove all of the machining marks. I now specify "BEAD BLAST PER MIL-PRF-9945D - MIL 7" on my part drawings which results in a nice looking surface finish that is very dull (matte). The problem is that after this is anodized black (MIL-A-8625 TYPE II CLASS 2) we end up with parts that are VERY matte in appearance and not as black as I would like. The surface feels very smooth but running a finger nail (or any object) over it results in it leaving a very noticeable mark. To remove this mark requires considerable effort. The best thing we have found so far to clear the surface is to use a microfiber cloth.
Anyways, what I would like your input on is the best way to achieve a satin-like finish on aluminum with no machining marks. Is there an alternative process to bead blasting I should be using that won't make the finish so dull?
We recently received some parts from a Chinese manufacturer that bead blasted as per my spec but then added a bright dip before anodizing. This creates basically the exact finish I want (it's very specular but not overly glossy) but I can't find anywhere remotely close to me (Calgary, Alberta, Canada) that will do bright dipping! Is there an alternative to bright dipping that will produce a similar result? What about electro-polishing?
Thanks in advance,
Devin
Product Designer - Calgary, Alberta, Canada
A. Satin finish can be achieved by sufficient alkaline etching. The process can usually remedy surface marks. However, it is difficult to imagine the extent of machine marks even with high definition photo. Superficial marks which are highly visible could be misinterpreted as deep marks so I can not definitely state etching can mask the imperfections.
Dado Macapagal- Ont., Canada
December 1, 2012
A. Another thing to look at is what grit size you're calling out for the bead blast. MIL7 is roughly equivalent to 50 grit, which is pretty rough. Try some experiments with MIL 13, see if that floats your boat.
You may also want to visit your vendor and find out what pressure he's blasting at and what material he's using. Aluminum is susceptible to having media embedded in it's surface if blasting occurs at high pressure. A good rule I use while powder coating aluminum is don't go over 90 PSI.
- Mt Clemens, Michigan, USA
January 23, 2013
Q. Dear Sir,
Can you please explain me the process of the Glass bead blasting? What is surface finish achievable procedure in same?
- Narmada, India
March 29, 2013
![]() |
A. The surface finish achieved, as in all blast operations, basically depends on the kinetic energy of the particles, which depends on their mass and speed and the hardness of the surface. Compared to other media, glass beads are round and their mass is midway between lighter materials like plastic, CO2 and organics. Aluminum oxide and silicon carbide are angular and heavier. Steel shot is the heaviest and can be rounded or angular. There are other factors like angle of incidence, bounce back effect, contaminants, etc. Guillermo MarrufoMonterrey, NL, Mexico April 6, 2013 A. The way you worded your question makes it kind of simple to answer. First of all you mentioned glass beads; therefore, you know the shape and relative hardness of the media. The only variable left is the size of the bead and the pressure/force you use to operate the system. Skid to bottom line, about the best you can achieve with a small bead is about 25 RMS. ![]() AF Kenton retired business owner - Hatboro, Pennsylvania April 6, 2013 |
Will bead blast degrade the chem film?
Q. On an aluminum part if I bead blast a chem film surface will I degrade the chem film?
Amy Savage- Viera, Florida
August 13, 2013
![]() |
A. Depending on the bead size, impact angle, pressure and duration, bead blasting will remove most to all of the chem film or anodizing. James Watts- Navarre, Florida August 15, 2013 A. Hi Amy, Aerospace - Yeovil, Somerset, UK August 16, 2013 |
Thanks All-
I thought so since it scratches so easily -- just needed that 2nd opinion to what I was hearing from a supplier.
- Viera, Florida
August 18, 2013
Q, A, or Comment on THIS thread -or- Start a NEW Thread