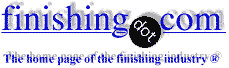
-----
Type-I Chromic for High Copper Aluminum Alloys
2007
Hello,
Does anyone know why the MIL-A-8625 / MIL-PRF-8625
[⇦ this spec on DLA] spec (para. 3.4.1) states that "Type-I coatings shall not be applied to aluminum alloys with copper content in excess of 5%".
Thank you,
- Irvine, California
My guess is that it's related to the known poor corrosion resistance of high copper bearing aluminum alloys. After all that is why the mil spec specifies 2024 (typically 3.8 to 4.9% by weight copper)for qualifying the process - if one can get 336 hours of protection on this alloy, they must have a good process! With copper contents over the amounts in 2024, that is in excess of 5%, the stated process control tests based on 2024 wouldn't test for this higher content.

Milt Stevenson, Jr.
Plating shop technical manager - Syracuse, New York
2007
2007
For a guess as to why the limitation is only on Type I rather than II and III as well - I'm betting on the thickness. As the anodic coat forms, any foreign bodies will eventually get covered over and included in the aluminum oxide itself - but it takes sufficient thickness to achieve it. With a Type I coating the thickness is much lower than a Type II or III, the foreign bodies (the copper) wouldn't get covered and your already poor corrosion resistance would fall even further.
But, that is only a guess. For an official answer you'd have to go to the body that controls the spec.
Compton, California, USA
It is because copper is more soluble in chromic acid than in sulfuric or phosphoric. As it dissolves away it leaves behind corrosion sites worse than the slightly less solubility in sufuric acid. The same is true with the zinc in some 7000's series alloys. Boeing and Lockheed both spell out which 2000's and which 7000's are acceptable for chromic acid anodizing, Types I and IB (20 volts). Those alloys are listed in Aluminum How-To along with the specification number..
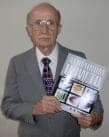
Robert H Probert
Robert H Probert Technical Services

Garner, North Carolina
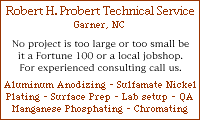
2007
Q, A, or Comment on THIS thread -or- Start a NEW Thread