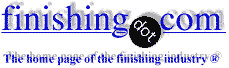
-----
Alkaline non-cyanide zinc lacks corrosion resistance of acid zinc
2007
We are conducting trials of alkaline non cyanide zinc plating on fasteners. We are able to achieve very good finish but we are unable to get S.S.T life for the same. Passivation done are Trivalent blue and yellow but the S.S.T life is only 24 hrs. While on our Acid Zinc line the same passivations give more life i.e Tr.Blue: 72 hrs and Tr.Yellow: 96 hrs without top coat/ sealer. The process we follow is as follows:
Process Sequence
- Soak Cleaning
- Water Rinse (Cascade Rinse)
- Acid Pickling
- Water Rinse
- Electro cleaning
- Water Rinse (Cascade Rinse)
- Acid Dip 5 - 10 %
- Activation Dip (NaoH) 5%
- Non Cyanide Alkaline Zinc Plating Process
NCZ Salt 120 - 150 Grm/Lt
NCZ A 15 - 20 ml/lt
NCZ B 0.5 - 1 ml/lt
NCZ C 1 - 2 ml /lr
NCZ Conditioner 12 - 15 ml/lt
Temperature 22 - 28 ° C - D/o Rinse (D.M. Water)
- Water Rinse (Cascade Rinse)
- Bright Dip HNo3 1/2 to 1 %
- Water Rinse (Cascade Rinse)
- D.M. Water Rinse
- Trivalent Passivation
Tr.Blue Tr. Yellow
Concentration 125 ml/lt 125 ml/lt
Temp. 50° C 50° C
P.H. 1.8 - 2.2 1.8 - 2.2
Time 45 - 60 Sec 45 - 60 Sec - D.M. Water Rinse
- D.M. Water Rinse
- Dry in low speed dryer 35 - 70 RPM
- Hot Oven Backing 80° C
Time 15 - 20 Min.
tools - Kanpur, U.P, India
First of two simultaneous responses -- 2007
Alkaline zinc plating systems are very sensitive to addition agent imbalance. It may be that you are seeing excessive stress in the plate, leading to microcracking of the deposit.
Make some Hull Cell
⇦ huh?
plates, and when they're finished, bend the corner and see if the plating cracks.
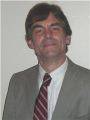
Dave Wichern
Consultant - The Bronx, New York
Second of two simultaneous responses --
I'm not sure if it's related to your salt spray test problem, but one thing that came to my notice was your final bake temperature - it's too hot! Passivated zinc should be heated to a maximum of 60°C for curing. I suggest setting your thermostat below that to allow for the 'hot spots' in your oven.
John Reid- Brisbane, Queensland, Australia
2007
Dear Pal,
Let me appreciate you for detailed posting of your query!
Alkaline non cyanide Zinc plated components with standard spec.;and passivated with either hex. or trivalent chromating will definitely give a 15-20% advantage on White Rust SST life over Acid Chloride Zinc.Adopted process sequence seems to be okay except may be Bright Dip( Nitric conc. You may keep 1%) and as the earlier responder said your oven baking temp seems to be higher.It is said that baking temp should not be "too hot to hold!".And lastly tri-passivations are fragile immediately after plating till 25 hours(curing).Please ensure parts are subjected for salt Spray only after 24 hrs curing.This may possibly the reason for failure. So 'handle with care'.Your operators have to be trained as they were handling Hex. passivations earlier as it can be handled 'rough & Tough'.
Regards,
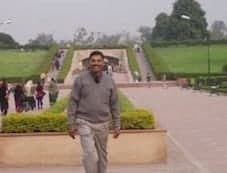
T.K. Mohan
plating process supplier - Mumbai, India
2007
2007
Dear Mr. Pal
Please note that use of better chemistry as indirectly mentioned by Mr.Dave Wichern, and also good trivalent chromate will easily possible to achieve SST life of over 125 plus to WR to Blue chromate and 200 plus WR to iridescent colour.(yellow)
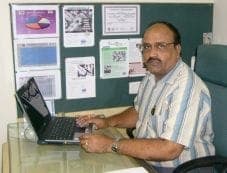
P. Gurumoorthi
electroplating process chemicals - Chennai, Tamilnadu, India
2007
Hi ,
please check the timing in trivalent passivations , set the time as per your required thickness of passivations and followed by a warm water dip and dry at 60 deg c, temp and don't allow your naked hand to come in touch with component when you are putting it for salt spray .
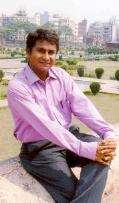
Praveen Kumar
plating process supplier
Mumbai, India
Q, A, or Comment on THIS thread -or- Start a NEW Thread