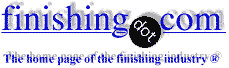
-----
Chrome plated hydraulic cylinder rods have pits, pinholes, and peeling problems
Hard chromium plating: A handbook of modern practice by Greenwood (1981)
avail from eBay or Amazon
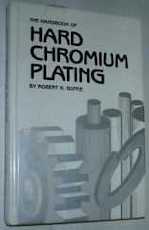
by Robert K. Guffie (1986)
avail from AbeBooks, or Amazon
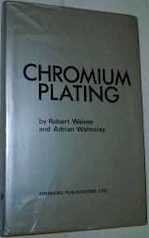
by Weiner & Walmsley (1980)
avail from eBay, AbeBooks, or Amazon
(as an Amazon Associate & eBay Partner, we earn from qualifying purchases)
Q. Hi all, I'm working for a company that machines engine valves.
Recently we have had experienced some issues with a chrome plate bath HEEF 842 HCR, I have never seen these effects in the past and it is not in all the parts, e.g., 10 pieces of 900, those pieces show a nodular and peeling area in the tip.
I'm sharing with you some specs of our bath and specs of the piece waiting for some recommendations to improve this situation.
Bath's composition.
CrO3: 249.7 g/l
Cr+3: 1.8 g/l
SO4: 2.48 g/l
Fe+: .7 g/l
Fl-: 5.13 g/l
Conductivity: 462 Ms/cm
Cl-: 26 mg/l
Bath temperature:
60 °C
Material Spec:
C: .4%
Si: 2.8%
Cr: 8%
Fe: Balance
Current applied
I: 68 Amps
Length of chrome plate area: 270 mm
Area: 1.04 dm2
Espec: 7 microns +/- 2
Anode material: Lead
Piece has a tip hardened.
Note: This effect only occurs on the tip, we use a pvdf cap to cover it.
Mfg. Engineer - Aguascalientes
October 20, 2023
⇩ Related postings, oldest first ⇩
Q. I am a new employee in a hydraulic cylinder repair facility. This facility has just started with new chrome bath. We use HEEF-25 for our chrome bath.
My team is currently testing the chrome quality. After several trials, we occur the same problem. The problem is that there are spikes/pinholes on the chromed rod after we are done with the chroming process.
I am not experienced in chroming, and thus, would like to ask how do you resolve the problem.
Thanks
hydraulics - Jakarta
2007
A. Since you are new, please try to get the vendor to visit and help you troubleshoot, Richard. Hard chrome plating is difficult to start up without experienced help, and may mean a lot of lost time and unnecessary waste. My suspicion would be that the problem is mechanical prep rather than the plating itself -- but it can be a long road if you go by guesses :-)
Good luck.
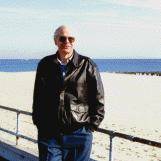
Ted Mooney, P.E.
Striving to live Aloha
(Ted can offer longterm or instant help)
finishing.com - Pine Beach, New Jersey
A. The highest probability is that you have microscopic burrs on the shaft from a machine operation or a blasting step. I doubt if the HEEF 25 is at fault, unless you have a very particulate-contaminated tank. Do not stir up the sludge on the bottom of the tank unless you have several hours to let it settle out.
James Watts- Navarre, Florida
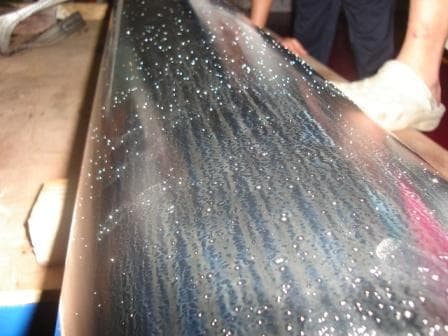
Q. I am currently experiencing pinholes problem in chrome.
The workpiece base material is made of K1045 mild steel, induction hardened (6 mm depth), with HRC 48.
The solution that I am using is ATOTECH HEEF-25.
Before I chrome, I stripped the chrome using NaOH (Sodium Hydroxide) Solution.
For the pretreatment, I used NaOH to clean off any particles or dust on the workpiece.
Before chroming, I etched it for 3 minutes. I chromed the workpiece at 60 °C temperature, at current density 20 A/dcm2. 2 hours later, I stopped the chroming to check the rod. To my surprise, there are pimples (when they are peeled off, they became pinholes) on the chrome. The chrome thickness then was 20 micron
I polished the rod to get rid of the pinholes. The chrome thickness became 10 microns.
Does anyone know what causes that? Why are there pinholes on the chrome?
Please advise. Thank you so much.
Plating Shop - Bangkok
2007
A. When there is problem do not panic; of course there is a problem, but a solution also.
Your problem is roughness.
What is solution? Filter the solution.
Check your anode quality from a reputed lab.
It should be 90% lead and 10% tin
Then comes your solution part.
Analyse for chromic acid, sulphate, iron, copper, zinc.
Chromic acid to sulphate ratio should be properly maintained as per supplier data sheet.
Temperature, C.D, as per supplier data sheet.
Precleaning as recommended.
Normally: soak cleaning hot, anodic cleaning, W.R, W.R, acid dip, W.R, W.R, etching, hard chrome, drag out, drag out, W.R, hot water + chrome neutralizer, dry.
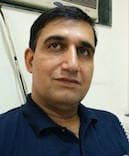
Ajay Raina
Ludhiana, Punjab, India
A. A long time ago, I used HEEF 25 for plating parts much like yours. I used a lead/tin/silver mesh conforming anode with about a 1 inch spacing. We used about 4-5 amps per sq inch and had vigorous outgassing that cleaned gas bubbles off of the part. We also plated vertically. How do you do it. If those white spots in your picture are your pits, those are massive pits and not pinholes.
James Watts- Navarre, Florida
A. I am an experienced hard chrome plater for the last 30 years. I specialised in Hard chrome plating of piston rods, engine valves, strut rods, pneumatic cylinders, etc. Your problem of pin holes can be solved by giving a light wash in 1:3 HCl and then polishing with fine grade sheet, and etching at low amps at the same temp of 60 degrees and start the rectifier by increasing the amps slowly step by step (not sudden downing the etch switch) and stop the bath after one hour and rotate the rod so that the sides facing the anodes will go down and the sides facing up and down will face now the anodes. Reverse etch for a few seconds. Then start the rectifier very very slowly to avoid peel off to the required amperage.
I have faced such problems in pneumatic pistons of earth moving equipments and new piston rods of plastic machines, and we solved all pitting by rotating every hour.
Cheers
Rajaraam
- Chennai, South India
A. Dear Richard Pho,
The problem is probably caused due to hydrogen embrittlement as you have suggested that these rods are Induction hardened and ground. I feel after stripping chrome and prior to grinding, stress relive these jobs @ 180 °C for 1-3 Hours and then grind. After grinding, if you can, super finish these components and follow standard pre treatment procedure for hard chrome.
Best luck
- BELGAUM -Karnataka India
April 27, 2014
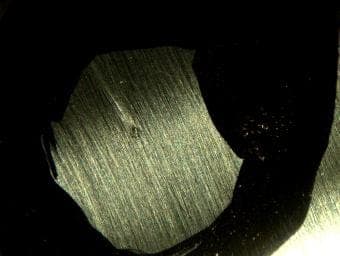
Q. Good day.
We are experiencing some problems with hard Chrome plate on piston rods, This issue is supposed to be the easiest to troubleshot according to all the sources we have found so far, but for us it's been a nightmare to solve this; I will explain in detail:
We chrome plate piston rods of different diameter and length, some of them are hollow rods and some others are solid rods, the steel used on all of them is SAE 1040. Every hollow rod is plated without problems but the bigger solid rods are the ones that had the flaking. In the first time the flaking was completely obvious and because of that we changed the chrome parameters to "fix" the problem but now it appears the flaking is still there in a very small scale (less than 0.5 mm wide on the flaking area).
The parameters to plate the common parts are all the same (including solid rod with less diameter), this is: electrochemical degrease at 10 A/dm2 for 180 secs. then etch at 40 A/dm2 for 90 secs and then finally chrome plate at 80 A/dm2 until we get the target of 25 microns. Of course there are rinses between every step.
Those parameters work just perfect for everything except the thicker solid rods; we do these parameters for those: 12 A/dm2 at 180 seconds on electro-degrease, 30 A/dm2 at 120 seconds on etch and 60 A/dm2 at twice the time of chrome plate compared to other parts.
We tried to reduce the time of etch to only 30 secs at 31 A/dm2 (as seen in some reference books) but the flaking was terrible, almost on all of the surface, we also increased the etch to 50 A/dm2 at 90 secs and got the same results of severe flaking. My next approach will be to increase the time of etch to 150 seconds but I still doubt it will work.
Can anyone give me some advice on what am I missing?
Process Engineer - Chihuahua, México
April 4, 2014
A. It sounds like you may not be allowing the solid rods enough time to heat to the bath temperature whereas the hollow rods will obviously heat more quickly.
Frank Dunleavyaerospace - Dublin, Ireland.
None of us thought of that, as it's said the easiest explanation is the most certain one.
We will try that immediately, thanks for the advice.
Process Engineer - Chihuahua, México
Regular parts accept hard chrome plating okay, but hardened parts suffer microporosity
Q. Hello,
We are facing a similar problem of microporosity in Hard chrome plated parts, but it is more restricted to hardened parts like En 19 H/T for 28 - 32 HRc (in C45/1045 it is not there). Please suggest something for this.
Also share what should be the final surface roughness to Hard chrome plate these hardened parts so we can put these checkpoints directly if it suits our practice.
Thanks,
- Ahmadabad, Gujarat, India
October 9, 2014
Q. My name is John, I work for a paint inspection company.
I have recently inspected a crane and was asked about a defect on the metal plating on the Hydraulic rams, to which I did not know.
There appears to be a breakdown of the plating on the Hydraulic ram, the crane driver on site said it started as a blister and now there are areas where the plating has come off. I a presuming this is due to a loss of adhesion from the substrate due to incorrect surface preparation or a fault in the plating process.
Can anybody shed any light on this, and what may have caused it. I have attached some photos.
Thanks in advance.
Regards
John
Paint Inspector - United Kingdom
December 8, 2015
A. Hi John,
At a guess the plating is probably chrome plating. It looks like corrosion under the plating has caused lifting of the coating. This happens when either there is an inadequate undercoat of nickel or copper or when there is no undercoat the chrome plating is too thin (less than 0.002"), although even relatively thick chrome plating is no guarantee against corrosion as it is micro-cracked and if you are unlucky a route to the base metal will still be present.
Aerospace - Yeovil, Somerset, UK
A. From the photograph the piston rod is working in a marine environment where corrosion can take place very rapidly, more so if the piston rod is heat treated. Please ensure that underneath Electro less Ni with phosphor content of 8-12% is deposited around 20-25 microns and 100 micron of Chrome plating. The pitting problem will be solved. Good luck
mahendra gargatti- BELGAUM.KARNATAKA India
A. Hi,
This is very bad chrome; it's not pinholes, it's chrome plate over rusted steel. There are areas that have FeO2 in the substrate which is not dissolved in a acid. If it would be pinholes it should be more smaller.
I'd say it's bad pretreatment before chrome. They talk about pinholes, but I have never seen it there and I have worked with chrome.
Pinholes, I think, you can see by microscope but not visual checking.
Regards
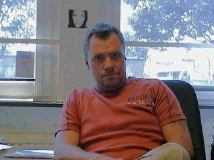
Anders Sundman
4th Generation Surface Engineering
Consultant - Arvika,
Sweden
A. Good day John.
I have been following this post, and I must agree with Terry's and Ander's postings that there is a problem with the pre-treatment/plating of the substrate before chrome. Given the fact that this is a hydraulic ram, one would think that the lubricants involved would offer a measure of corrosion protection.
The appearance of blisters on the chrome clearly indicate adhesion issues and insufficient chrome thickness.
My opinion is that the substrate is not properly cleaned/prepped as various steels contain various metallic compositions. The ram obviously is a hardened steel, possibly heat treated, and requires special treatment measures to deal with these facts.
I think that this ram requires a hard chrome process (without a nickel underlay).
Hope this helps.
Regards,
Aerotek Mfg. Ltd. - Whitby, Ontario, Canada
Chrome plating blisters on one side, pits on the other
Q. Recently we received a part back from a customer that showed some anomalies. The inner part of a flange showed ball like blisters on top of a chrome plate layer whereas the outer part of the flange showed also pits in the chrome layer.
I have not seen that before. Does anyone recognize this effect and perhaps knows what can cause this effect?
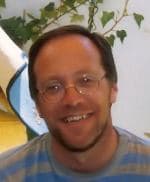
Arnold Langeveld
Fokker Aerostructures B.V. - The Netherlands
February 13, 2019
Small White Spots In Chrome Plating
Q. Hi,
I am working as plant head in New Delhi in one of the plating Company. We manufacture Metal Cylindrical Rollers which are used to print on Aluminium Foils.
Recently while chrome plating we found some strange white spots on the surface. it seemed as if small pits are getting etched in chroming process. While printing, these pits are leaving their impression on the printing material as well.
Also the surface was rough. I tried to add barium to it and the result was not good. There were more of spots on the surface. Seeing this I added sulfuric into the solution to increase the sulphate level and the result was less spots on the surface.
Now I've controlled the major part by maintaining the sulphate level but the spots are not getting over.
What can be the solution to get rid of this problem?
Thanks.
- New Delhi, India
May 7, 2020
A. Hi, NAKUL,
I am not wrong, this is rotogravure industry. And that's supposed to have a copper process prior to the final hard chrome plating.
For the white spot issue, I assume you have already done Hull Cell
⇦ huh?
and never detect anything on hard chrome solution. We did encounter the similar issue before, suggest to look into Copper plating process.
Another possibility is copper layer been over-etched in chrome solution, maybe caused by too long idling time in chrome bath before you turn on current.
If this issue only happened on stripped roller, please look into your de-chrome process as well.
Regards
Raymond
- Singapore
Q. Hi, I am working in a company making equipment for Dredging/Marine applications, recently we have delivered equipment consisting of two hydraulic cylinders, rods made of SS316 with 40-micron hard chrome coating. We have received complaints of pitting on hydraulic cylinder rod after a few months of delivery. Considering climate condition 50 °C with humidity of 60% and working in the harsh environment near shore. Can anyone make out from the pictures, if it's a Coating problem? or Harsh climate?
Moreover, what could be the solution for such an application?
Thank you in advance.
- Dubai, UAE
December 29, 2020
A. That does not look like corrosion, it looks like bad adhesion. Suspect your NiCl strike is not activating the stainless steel, that the metal has climbed, go back check the metal content, get it down, Raise the HCl, then try again.
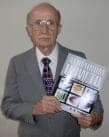
Robert H Probert
Robert H Probert Technical Services

Garner, North Carolina
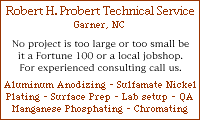
A. Hi. Robert may well be right, but I'm not so sure, based on the numerous tiny spots (which might have been more obvious to me in the original full scale photos that in these reduced & excerpted photos. To me it does looks like corrosion -- but not general environmental corrosion: acid damage ... like someone wiped them with bleach, which may not be unheard of in these Covid-19 days :-(
Were both rods on the same piece of equipment? Do the two problematic rods have anything else in common with each other except being on the same piece of equipment? Were they from a lot of just two or randomly selected for this machine from a larger lot? But I'm just guessing, not claiming expertise in finding cause from photos :-)
Luck & Regards,
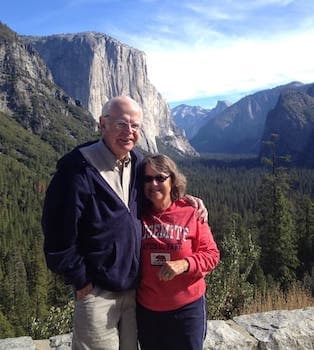
Ted Mooney, P.E. RET
Striving to live Aloha
(Ted can offer longterm or instant help)
finishing.com - Pine Beach, New Jersey
Q. Hi, the base material has been chemically tested and it's proven SS316. Both rods are from the same equipment and problem found in a total of 5 equipment out of 15. It has been installed on-site in January 2019 (no Covid that time in the country) and common between rods is they are made in the same facility (batch vice) and used in the same environment. Equipment is in used in seashore where seawater splashes and salty climate is common.
Ron Ramn [returning]- Dubai, UAE
A. Hi, Ron.
Please refer to the similar problem of John from December 8, 2015 on this post and following answers of Brian and Mahendra. My impression from your photos and the equipment service conditions (50 degree C and "harsh environment near shore") is that your case is more corrosion problem, than adhesion. Indeed, your shaft is "SS316 with 40-micron hard chrome coating", but 40 micron chrome without nickel or EN underlayer is not enough in high salt environment. I shall recommend to add 40-50 micron of high phosphor EN before chrome plating.
Good luck
Alex
- Lod, Israel
A. Yes, it seems to be peeling.
freddy Bren- Buenos aires
January 2, 2023
Q. Hello to all,
We are chrome plating polished rods in horizontal position (static, not rotative) up to 8000 mm (26 ft approximate) length. Diameter 38 mm (1 1/2")
Thickess 0.15mm per side
Solution is filtered constantly and balanced chemically.
Not using any mist suppressants
Current enters from both sides, but enters only from one side while we etch for 30 seconds and then cathodize.
We use air to move the solution that is located in the bottom of the tank.
The ISSUE is that we always get pin holes only on the top side of the bar, about less that a quarter of the diameter. If we spin the bar to other sides, it has practically zero pin holes
Also, we get more pin holes concentrated on the side where the current enters to cathodize.
Would be very grateful to get any help or ideas of what could be the cause
Thanks in advance!
- Santiago, Chile
December 2, 2021
A. Hello Dante.
a) Some information is missing in your post. Assuming you use a classic Chromic/Sulfuric bath and plate Chrome on Steel substrate - it may be a problem with your electrical set-up.
Your long rod has a large surface area ~1500 sq. inches.
It means at current density of 2-3 ASI you push through your rod ends around 3000-4500 Amp. The ends are only 1.5 inch in diameter, they may be overheating.
b) You did not provide a photo of your "pin holes", so it is difficult to advise something. If there is not enough flow in the tank (agitation or liquid circulation), there is a chance to see "gas pits", as Hydrogen bubble sticking to the part will prevent Chrome to deposit.
Just my 2 cents...
- Winnipeg, Canada
A. Instead of using air agitation I prefer two Eductor pumps operating from two opposite sides of the plating tank for circulation of Plating Solution,
Mahendra Gargatti- Belgaum KARNATAKA India
Q. Hello, thanks for your input!
a) We are giving 3000 amps per bar.
Our chrome plating tank has 16000 lts, not classic as we add additive for high speed efficiency and micro cracking.
We chrome 6 bars at a time: 2 jigs of 3 bars each
What you say about over heating the ends, is a reality. We do notice much more temperature on the ends after we take the jigs out of the tank... any idea of how could we correct this?
2) Our agitation is done with compressed air (oil free compressor). A tube with little holes is set up in the bottom in all the length of the tank)
Please see the pictures.
Thanks!
- Santiago, Chile
Q, A, or Comment on THIS thread -or- Start a NEW Thread