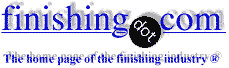
-----
Machining Chrome
Are there any good milling cutters that can cut chrome on a milling machine. I am going to try and take about .10 out with a 4 flute end mill. Any information on cutting chrome would be greatly appreciated.
Wolfgang Marschall- Valencia, California, USA
2007
First of two simultaneous responses --
There are no metal or alloy tools that can cut chrome. Not even tungsten carbide or ceramics tools will. But it can be EDM'ed.
Guillermo MarrufoMonterrey, NL, Mexico
2007
Second of two simultaneous responses --
NO! You grind chrome and you do it with the proper grit and the proper resin wheel. Also, you do not get in a rush. you take about a quarter of a thou per pass. anything else, kiss your chrome plate goodbye.
James Watts- Navarre, Florida
2007
I agree with James but I would not consider anything higher than a tenth of a thou or you will lose the chrome or create other problems such as macrocracking.
Brian TerryAerospace - Yeovil, Somerset, UK
2007
Brian, I agree with you if the chrome is thick or you are doing a large area. for some reason, I thought that this was a tiny area. If you do not need a good finish, using a larger grit and a softer resin wheel with lots and lots of cutting fluid will probably get by on a non critical area. It comes with a cost of higher wheel breakdown. I am in love with diamond and 0.0001 per side. I have not met a manager over the machine shop that would comply with directives, short of having his/her job threatened for non compliance. It was so easy to blame the plater.
James Watts- Navarre, Florida
2007
2007
James,
I must admit that I thought that hardness is the big consideration before working out how much to take off per pass. Obviously the softer chromes (500ish HV) are much more tolerant to heavier cuts than say a very hard chrome (say 1000ish HV). I will admit that a thicker coating is a little more resistant to heavier cuts than a thinner one.
On the point of managers and their need for speed, I have to deal with that sort of ignorance of the finishing process virtually every day. Sometimes it feels like you are banging your head against a brick wall when the immediate response to any problem with the part is "It must be the treatments, it can't have been anything I have done"!
Aerospace - Yeovil, Somerset, UK
I am a plater and always try to achieve chrome thickness as close to the requirement. For long (3m) internal diameters of ±30mm I find it inevitable to get variations from ends to centre of about 100 to 40 µm respectively.
Are there efficient methods for internal grinding or honing chrome?
Precision Engineering - South Africa
2007
Q. What is the proper wheel to use for ID grinding chrome, about a 5" diameter. Also what is the proper speed?
Charles McAvoy- Whitehall, Pennsylvania, USA
November 17, 2012
A. I found that the best source of information is to go to tech services of at least 2 major wheel mfgrs.
Factors in grinding chrome are the type of grit, the size of the grit, the resin that holds it together, the surface speed of the wheel, the surface speed of the part, the speed of the cut moving and the depth of the cut.
All of this will also relate to the final surface finish.
There are numerous tradeoffs to be made. How often you have to true the wheel is frequently forgotten.
The cost of the wheel is nearly insignificant compared to time on the machine.
AVOID heavy cuts. Looks good, feels good saves money -- EXCEPT the plating burns or peels and you get to do it all over again. Bad management.
Choice of wheel is critical. A shop that I worked in would run out of the proper wheel and would use an old type with 50 to 90% recycle rate,
- Navarre, Florida

Q, A, or Comment on THIS thread -or- Start a NEW Thread