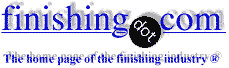
-----
White Patches appearing on Chromate Passivated Zinc
Q. Sir,
We are bright zinc plating from medium cyanide bath mild steel parts which are cylindrical in shape with through bore and having hexagonal faces. While drying the plated parts with chromate yellow passivation (iridescent) in a centrifugal dryer at 60° C the dried parts have white patches on the hexagonal surface. Can the white patches be avoided? Can anyone with similar experience help? Thanks.
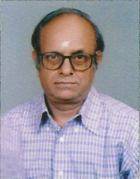
Subramanian Ramajayam
consultant - Bangalore, India
2000
![]() |
A. Dr Mr Ramajayam, The fact that only the hexagonal surfaces seem to have the white patches seems to suggest that this is the classic problem of plating components with only partially machined surfaces. The hexagonal surfaces may be the un-machined portion having surface defects which bleed after plating which causes the white patches. Try stress relieving at 400 °C after degreasing and pickling and before plating. Consider using Acid Zinc plating instead of Cyanide Zinc. Best of luck, ![]() Khozem Vahaanwala Saify Ind ![]() Bengaluru, Karnataka, India ![]() 2000 A. Dear Subramanian, 60 °C is too hot. Recommend 42-44 °C. The yellow (any chromate) will degrade at that temperature. The hexagon ends are where the water will tend to accumulate. Be sure the final rinses following chromating are clean. The ends are probably very smooth metal as well. If the parts are going through a hot water rinse prior to spin dry, if this hot water is contaminated, it is adding to the problem. If the basket is full, reduce the quantity of parts. Hope this helps. Bill Hemptech svc. w/ chemical supplier - Grand Rapids, Michigan 2000 A. I think that your first step should be determining if the white spots are from salt build up in the rinses or corrosion of the zinc layer. Since it appears as though this problem occurs during the drying step, I would think that you should take a look at the final rinses first. I've seen high solids contents in the final rinses cause this type of spotting. If the problem is corrosion of the zinc layer, look at the chromate pre-dip (if you use one) to make sure you are neutralizing any residual plating solution. Check the pH of the rinses also to make sure that your chromating solution is also being neutralized. One final suggestion, check the porosity of your substrate. If your substrate is porous you might be trapping solution that bleeds back over time and causes the white spots. Your rinses should be taking care of the problem. Robert Holderman- Tulsa, Oklahoma 2000 |
Q. Sir,
The above problem was posed by me. I thank all the participants for the suggestions. But one fact which I have not given is that if the plated parts are not dried in a centrifugal drier but just air dried with a hot/cold air blower, the white patches are minimal. So, could it be due to abrasion effects between the parts under centrifugal force in a centrifugal drier? But the parts appear very dull and somewhat of faded color. Thanks.
Can the white patches that normally appear on yellow passivation be avoided by resorting to olive-drab or black passivation after zinc plating?
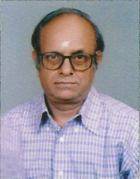
Subramanian Ramajayam
consultant - Bangalore, India
2000
A. You described white patches and the fading of the plating color. That looks like corrosion to me. My guess is that for some reason, the corrosion protection of the chromate is being used up. I am just finishing up salt spray testing on some parts that behaved the same way, but as a result of 300 hours of salt spray.
I am not even going to try and imagine why it is happening or how to fix it.
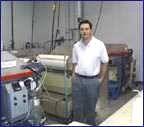
Tim Neveau
Rochester Hills, Michigan
2000
A. Dear Subramanian
Please [determine] the chrome content in the passivation bath with help of AAS
⇦ on
eBay
or
Amazon [affil links] (Apart from the regular concentration analysis). If the chrome content is low, there will be a chance of white patches.
- Bangalore, India
December 1, 2012
Q. We are having problems with passivation after Zinc plating. After we plate the item we rinse it in cold running water and then rinse with deionized water. Finally neutralize it with dilute nitric acid and the golden passivation is done with Chromic acid. Items often exhibit whitish area near the edges like a finger print. Also we noted that the rinsing water we use is turbid and has a slightly whitish appearance. Is that the cause of the problem or is it something else?
Yaseer ZohaElectroplating Shop - Karachi, Pakistan
September 27, 2012
A. Water with distilled water, a paper tape pH meter (indicator Alkaline) and tighten the hexagonal hole. If the measured pH is alkaline, leaching is occurring yellow chromate. If this occurs before chromating leave the part in hot water (90 °C) for 5 minutes and then chromate. Good luck
Rogerio Linares- Limeira SP Brasil
October 3, 2012
A. Dear Sir,
Yellow iridescent Chromate Passivation shows this problem quite often. Zinc deposit from Cyanide zinc bath needs to to thoroughly rinsed and activated /neutralized using well maintained Nitric acid dip, otherwise alkaline residue on surface will adversely affect the adhesion of Passivation film.
Secondly concentrated passivation solution forms thicker passivation film which has poor adhesion to zinc. Using dilute Passivation solution or reducing the dip time may help to some degree. Wet passivation film is fragile in nature and can get damaged during centrifugal drying.
Good luck, Thanks.
- Mumbai, India
January 14, 2013
White residue on gold chromate
Q. Hi,
We have 6061 extruded heat sinks which are machined and then plated with gold chromite.
Everything seems fine locally but when we ship to our customer this white residue shows up.
Any idea what could cause this?
MARCO SUNICO- Long Beach, California
February 11, 2019
A. Hi Marco. From this distance it looks more like corrosion than residue. Does the white color wipe off with water or acetone? Have you looked at it with a loupe or microscope? Are higher rez pics available?
Regards,
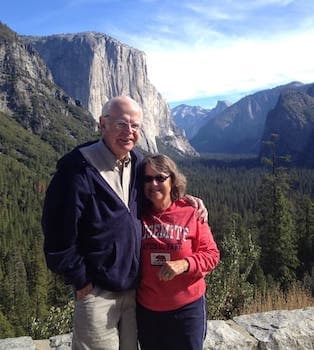
Ted Mooney, P.E. RET
Striving to live Aloha
finishing.com - Pine Beach, New Jersey
February 2019
Q. Hi Ted,
From what I have gathered it's related to the machining / drying process before chromate. I believe it's cutting fluid that is left over before the plating process.
Is there a possible added process prior to the first cleaning bath that can be done to prevent this and streamline the process?
- Long Beach, California USA
February 20, 2019
A. Hi again. If you have determined that the cause of the discoloration is inadequate cleaning of cutting fluid, and that the cutting fluid is solvent based or solvent amenable, you can remove it with a modern perchlorethylene vapor degreaser before the in-line cleaning. Good luck.
Regards,
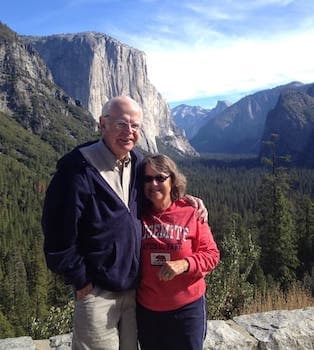
Ted Mooney, P.E. RET
Striving to live Aloha
finishing.com - Pine Beach, New Jersey
February 2019
Q, A, or Comment on THIS thread -or- Start a NEW Thread