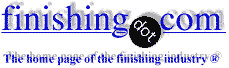
-----
Electropolish AND Bead Blast?
Q. We recently reviewed routing sheets for a maker of 303 stainless steel components which are then electrodeposited with nickel plating per FED-QQN-290 (replaced by AMSQQN290)
specs. Routing sheets indicated a permanganate clean followed by an electropolishing step and then followed by a dry glass bead blast.
These components are seeing a high degree of plating adhesion problems recently even with the above cleaning regime. We reviewed other components which have similar cleaning processing/plating done to them without any plating adhesion problems. Those components are also made of 303 stainless.
We've went to copper strikes recently which has resulted in components where the nickel plating adheres but it is believed at this time that the root cause of the plating adhesion problems still not been identified?
Removal of Nickel plating from stainless steel surface is not an option. The engine manufacture wants the plating.
Aerospace - Buffalo, New York, USA
2007
A. I may have misunderstood your question, Daniel, but it sounds like you don't yet have any observations upon which to make a conjecture towards root cause except that a copper strike helps. If I understood, the parts are processed identically and the plating adheres to some and fails to adhere to others?
QQ-N-290 says it applies to steel (and copper materials) but it does not claim to apply to stainless steel, and I don't think it does. I think you need to do a Wood's Nickel Strike before the copper plating. Of course, the usual caveat applies that you can't process real parts except per the specifications.
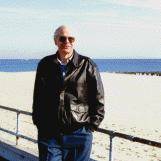
Ted Mooney, P.E.
Striving to live Aloha
(Ted can offer longterm or instant help)
finishing.com - Pine Beach, New Jersey
2007
A. My favorite subject, 303.
From several years in jobshop work, we rarely saw just plain 303. It almost always had a suffix something like S or Se or ? These make a world of difference as it is an additive to 303 to make it "free cutting" as in leaded brass.
That said, I have never seen such an aggressive preplate cycle.
The electropolish makes it difficult to plate because the surface is now very passive and has oxide films. The glass bead helps to reduce the passivation by roughing up the surface.
The solution to adhesion problems is a stronger acid activation step, one for whatever suffix SS you are working with. You have NOT mentioned what you are using. Without delay, go to a Woods Nickel strike. This is not a good place for a sulfamate nickel strike which is great in a few other places. Next is to not let the parts repassivate between the strike and the nickel plate (it only takes seconds). Keep the parts wet and proceed as rapidly as the line will go.
I do not remember any Aerospace OEM spec that allowed a copper strike on 300 series alloy under a nickel plate.
- Navarre, Florida
2007
![]() |
2007 Q. Hi; - Buffalo, New York, USA A. I'd agree with the previous two submissions adding that the permanganate followed by electropolish pretreatment is what I would expect for heat treated or welded stainless that has an intense blue heat treat scale. Using an alkaline permanganate renders the blue, acid-resistant scale removable by acid (i.e. electropolish)treating. My firm does a ton of nickel plating on stainless, Invar, and other nickel bearing aerospace materials such that the parts can be brazed - we rarely encountered such adhesion woes - especially on something as basic as 303 (S or Se) stainless! Another possibility could be the cleaning - anodic cleaning of nickel bearing alloys can also render the surface more passive that it would be otherwise. ![]() Milt Stevenson, Jr. Plating shop technical manager - Syracuse, New York 2007 |
A. Dear,
With all that cleaning and electropolishing, your are realising a perfectly clean and smooth surface. Why are you destroying/contaminating this smooth surface with the glassblasting?
In my experience, an electropolished surface is a perfect base for an electroplating.
On the other hand, the sequence and type of layers you have to apply are very important and are the problem/answer in your situation.
- Brugge, Belgium
2007
Q. Disclaimer: I am a control systems engineer, so I am way out of my field. Pardon any ignorance I show and please use small words.
We had a 316SST tank return from electropolishing without a consistent finish. For cosmetic reasons, we subsequently glass bead blasted the exterior of the tank. What effects could the bead blasting have on the EP surface properties? Also, what may have caused the inconsistent finish?
Thanks ahead of time for any help.
- Flagstaff, Arizona, USA
April 19, 2013
A. Hi John,
One of a million things could have caused what looks like an inconsistent finish, from how the parts looked before they were electropolished to the solution chemistry not being quite right to current distribution not being what it should.
Glass bead peening the surface will dull it as the electropolish is designed to remove the high points on the surface of the part, improve corrosion resistance and often as a consequence brighten the surface (although that doesn't always happen). Using glass bead will more than likely not affect the corrosion resistance as you are not introducing free iron, so your only real effect is cosmetic.
Aerospace - Yeovil, Somerset, UK
April 25, 2013
If you don't join the fight, our days are numbered.
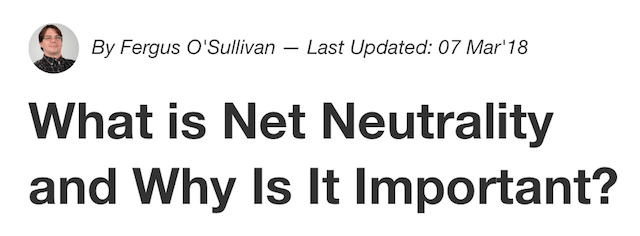
It's good to know it's mostly cosmetic. Thanks for the reply.
- Flagstaff, Arizona, USA
April 26, 2013
A. Bead blasting may improve corrosion resistance to intergranular corrosion by altering the grain boundaries at the surface.
Lyle Kirmanconsultant - Cleveland Heights, Ohio
April 30, 2013
Q. I recently had a vendor ask me why we EP after ceramic bead blast. The full process is: heat treat or laser weld (referring to two diff parts) , fine ceramic bead blast, EP, and passivate. I there a concern with EP after fine ceramic, as their suggestion was to do the bead blast after EP?
Abisha VaratharajDevelopment Engineer Sports Medicine - warsaw, Indiana, USA
October 15, 2014
A. If you do the bead blast after EP, you might as well not EP at all. EP is effective in brightening and passivation only when it is the final surface process.
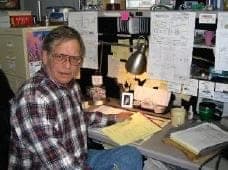
Jeffrey Holmes, CEF
Spartanburg, South Carolina
November 3, 2014
A. The only reason I could see for the treatments after the bead blasting is to perform a double passivation step. The EP is an excellent passivation method. The process would remove any iron particles that might have been imbedded onto the surface of the product, as well as improve product appearance
The second passivation step is probably redundant unless there are intermediate manufacturing operations between the two processes. Most times it on the print and is hard to remove.
- Detroit, Michigan, USA
November 24, 2014
Thank you for the responses.
- Warsaw, Indiana, USA
November 24, 2014
A. Just to clarify, electropolishing and passivation for stainless are two entirely different processes.
Any polished surface (EP or mechanical polishing) is more corrosion resistant than a rough surface. However, polishing does not promote a low iron, high chromium surface like acid passivation does. These are two completely separate routes to increased corrosion resistance. As such, the effects can even be stacked by passivating after polishing.
I could maybe see passivating prior to bead blast if there was some surface iron contamination that would cause problems if not removed at that point. EP prior to bead blast just seems like a waste. Whereas bead blast as surface prep for EP may or may not be worthwhile, depending on the original surface condition and the desired final appearance.
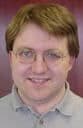
Ray Kremer
Stellar Solutions, Inc.

McHenry, Illinois
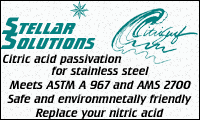
December 1, 2014
Q, A, or Comment on THIS thread -or- Start a NEW Thread