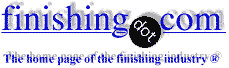
-----
Blast Furnace Ignition Trouble--Keeps Blowing Out!
2000
I am a man of all trades. . . . and still try to master each one. I was a tool & die maker, by trade, till the metric system started taking over (in this country) back in the early to mid 70's, and ended up going to work for the railroad industry as an electrician. I still love to work steel and other metals. I have a small business where I do sharpening and leather-crafting, welding, tool & jig design, etc. and design (usually on the spot) for any-one who needs a tool, jig, lifting rig, etc. for a small price) A couple of years ago I became fascinated with melting and pouring aluminum (using green sand casting methods). Over a period of a couple of years, I have been designing a propane fired blast furnace. A fellow, in the CUMBERLAND CRAFTS something -- another gave me a detailed description of a furnace that he had designed and built, so I drew a sketch of it and e-mailed it back to him and he responded that, yes. . . . in fact, that did look like the one he had built.!
Well; I built the furnace. . . . following his described plans as closely as possible. I have finally gotten it built and ready to fire-off! I lit it and it went out! I was so excited that I was finally going to get things rolling, but, still, there are problems! I have adjusted my air-blast down to a minimum and have adjusted the amount (more and less) of propane that I allow to enter the mixing area. NOW---HERE IS MY QUESTION: When I light the thing; I do so with a rag. I light it and drop it into the blast area. Then
I turn on the propane and it flames up pretty good; then I turn on the slow air blast. I get a rotating flame that blows itself out. I've tried to light it with the cover in about every position from completely open to completely closed (with only the exhaust hole in the center open). Some of you have, no doubt, been thru this mell-of-a-hess! Please. . . . set me straight. I've amassed a huge pile of aluminum cans, small engines, junk aluminum of all sizes and shapes and friends ! are still saving it for me, in h opes I'll figure out how to make my foundry set-up pay off in the near future! I've been investing time (by the boo-koo's) and money getting the furnace to where it is. . . . NOW WOULD SOMEONE TELL ME WHAT THE HECK TO DO NOW!? I'll thank you so much for any help that you can give me. W.A. "General" Lee

William Lee
saw sharpening & etc. - East Ridge, Tennessee
Sounds to me like you have the blast air at a wrong location or a wrong angle. Possibly you do not have a large enough jet for your propane. You can blow out some propane torches by just having too much gas velocity at the orifice. I have a direct pressure plumbers pot (no pressure reducer) and I can blow it out if I open the valve too much. This will melt the bottom out of a cast iron zinc pot after a while, it is so hot.
James Watts- Navarre, Florida
2000
2002
I've no experience in metals, but I have an extensive background in glass work including neon signs which use leaded glass. The burners for leaded glass sound similar to what you're trying to put together, ie, propane and forced air.
I've dissected these burner jets and manufactured my own although I've found it's simpler just to buy the tips and build the plumbing myself. But for what it's worth, the way the tips or burners work is you have a center port where the propane/natural gas exits and that single central tube is surrounded by a set of smaller diameter forced air jets.
When you light it up, you start off by turning on the central propane/natural gas jet first. Next, you turn the air jets on very gently. I used old refrigerator compressors to produce my compressed air, but any source will work as long as you can get decent low pressure control. As the small tubes along the sides shoot the air into the central gas jet, the flame suddenly becomes very tightly defined and hissing. It produces a really pretty pointed blue flame with an almost white cone at the center. By adjusting the gas and the air in increments, you can produce a monster of a flame using just household gas and compressed air from a refrigerator compressor.
As you've found from your problem, it's real easy to get too much air. That's why it can be easier to just buy the tips rather than making them, but it's possible to make them too. I made some using two diameters of copper and a washer with holes drilled in it. The small diameter copper tube was the gas line and the larger one was the air line. Little holes in the washer were the exit points for the compressed air. It didn't give a nice even flame like the commercial models and it tended to blow out too easily, but it did work.
Steve Anderson- Taipei, Taiwan
2003
Dear,
Blast furnace unit in operation you should understand thermodynamics and chemistry. Okay, my answer: first fill the furnace properly
1. bottom sprinkle slag product refractory
2. you put dry wood channel way air can pass
3. over that coke
4. in front of tuyre only wood
5. half of the furnace you put wood and coke alternate layer
6.after that limestone.
7. you ignite with kerosene and cotton soaked with oil
8 low pressure wind. Try this.
Bleeder should kept open. No conection to gasline.
M.Vijayakumar engineer blast furnace- Delhi , India
2003
Dear,
Yesterday I send some tips for your question continuation of that.
1. dot ignite all the tuyre ignite alternate tuyre ok there is reason for that. how to increase productivity.
1.blow maximum wind it will increase combustion jone
2.use high flame temperature it will increase kinetics of gases.better reduction.
3.avoid pressure drop minimize dust,use top pressure you can increase wind blow because top pressure reduces pressure drop
4.make .9 basisity slag helps reduction in pressure drop,high driving rate
5.check up alkali dangerous.to refractory.
6.always study top gas generation it helps to know furnace thermal regime.
7.use agglomerate. 8
.don't allow water leakage.
9.produce low silicon moderate sulfur.
10. always keep people who are sincere rather then brilliant blast furnace require that.
11. obsserve color of the gas.
12.color of the bf gas.
13. most important to absorb top gas smoke at bleeder to know the combustion in side furnace.
14. I enjoy the furnace. metallurgical engineer I love blast furnace any question most welcome, I'm 30 year old.
- Delhi, India
We are facing frequent tuyeres burning at our blast furnace. Almost all the tuyeres burnt were at 6 clock position. We are pretty baffled at this. We are not able to find the reasons for this.We do not have any auxilliary fuel injections. Only 1.5% oxygen injection is available.
Sumeet Kumariron and steel industry - India
February 19, 2008
May 9, 2008
Reasons for Frequent tuyreburning
1] Enlargement of Dead Man Zone
2] Poor hearth Annulus
3] prolonged operation in low blast
4] Insufficient cooling water pressure at tuyre
5] Coke value CRI CSR
6] Manufaturing Defect in tuyre.
7] Viscosity of the slag
8] High Pressure drop in furnace
regards
- New Delhi, India
Q, A, or Comment on THIS thread -or- Start a NEW Thread