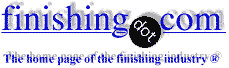
-----
Etching aluminum for NDT penetrant inspection
Q. I AM IN CHARGE OF A PLATING SHOP. WE ETCHED 2024 T-8 ALUMINUM BELIEVING IT TO BE 2024 T-3. WE FIRST ETCHED A 2024 T-3 COUPON TO DETERMINE THE ETCH RATE IN ALUMINUX 1000, 6 OZ./GAL. FOR 5 1/2 MINUTES AT 160 F. WE THEN RAN THE 2024 ALUMINUM PARTS UNDER THESE SAME PARAMETERS AND THE PARTS PITTED BADLY. CAN ANYONE EXPLAIN WHY 2024 T-8 ALUMINUM PITS UNDER THE ABOVE CONDITIONS?
Jerry Wahlinplating shop - Compton, California
2000
A. No. Did a coupon of T-8 material also pit? I think your processing solution is past its useful life.
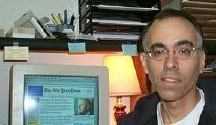

Tom Pullizzi
Falls Township, Pennsylvania
2000
A. I know this comes a bit late and perhaps you might already know why your 2024 parts pitted and the coupon didn't. But why in the heck would you be etching 2024 at all under those conditions? You ween't prepping to plate for sure. And the amount of aluminum you removed would be significant. The heat treat designation from you coupon to your part is different. I have coupons also but they are not heat treated as the parts are. I also use them to set up a etch rate . I use 1 minute and determine from there. I think it has a lot to do with the difference in heat treat designation. But also, WOW, thats a long etch time
Todd Huehn- Minneapolis, Minnesota
2001
Q. Hi,
I am a small processing plant for Aerospace Parts and Use Sodium Hydroxide Mixed with water in a 80/20 mixture (20% NaOH, some parts go to penetrant inspection while others will go to Chemical conversion. I have always been taught that you should never pre-etch if the par(s) are just going to chem. conversion but our supplier desires this step!
My question is that the NaOH mixture has been said to be to harsh and the Alodine test panels fail (big surprise here) when subjected to the 168 hour salt spray test in ASTM B117.
So what else is out there besides using the mixture that I am. By the way tank temp is 150 degrees F.
Aerospace Plating & finishing - New York
2007
![]() |
Why wouldn't you etch before chemical conversion coating? We do chem-film here every day and etching is a standard part of the process for us. And we haven't failed a salt spray test. Compton, California, USA 2007 A. I've got a couple of concerns - NaOH etching prior to chromating, particularly on high copper alloys such as 2024 which is mandated to use for mil spec chromating will indeed concentrate copper on the surface following etching resulting in gross salt spray failure. This is what NOT to use; ask a reputable supplier of chromating material which pre-etch works best - while you're at it, let your local sewer authority know so they can sample your discharge. If you use the right material, it's likely you won't be meeting your discharge limits. Also, most NDT penetrant requirements for etching, I believe, require the use of acidic etches. Either way, if you're using alkaline etching, you need a strong acidic material to de-smut prior to NDT. Chromic/sulfuric and/or nitric/hydrofluoric combinations work well for this - if they sound dangerous, they should! Leave chemical processing up to those who know chemical processing. ![]() Milt Stevenson, Jr. Plating shop technical manager - Syracuse, New York 2007 A. There is very much controversy on whether to alkali etch ahead of aluminum chromate. I feel that the decision is based on the condition of the raw panels. ![]() Robert H Probert Robert H Probert Technical Services ![]() Garner, North Carolina ![]() 2007 |
But does your client buy the aluminum for their actual components exclusively from this fourth coupon supplier, Robert? :-)
I've never understood this madness of having to search high and low for a supplier of test coupons which will pass a salt spray test when the actual component material is not similarly selected :-)
Some day, somehow we must all get together and fix this ludicrous corrosion test which tells us nothing about the metal the actual components are made of, and very little about the process sequence, but instead indicates how old and how good the test coupons (which will be thrown into the scrap bin) were :-)
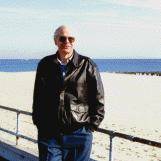
Ted Mooney, P.E.
Striving to live Aloha
(Ted can offer longterm or instant help)
finishing.com - Pine Beach, New Jersey
2007
Micro-etching of aluminum
Q. We are thinking of installing a micro-etching line for Pre-treatment of FPI process - does anyone have a procedure for running the line?
Bob BramsonB&M Finishers / Prismatic Stainless Steel

Kenilworth, New Jersey
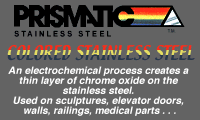
January 24, 2019
Aluminum finish and Liquid Penetrant (NDT) Testing
Q. Hello, I am working on a project that involves machined aluminum that needs a protective coating, but still needs to be inspected via Liquid Penetrant (NDT) Testing. I have used anodizing in the past, but this new project does not allow anodizing due to material fatigue concerns. Is there a coating that will not affect the mechanical properties of the aluminum and still allow Liquid Penetrant (NDT) Testing inspection during service life?
Dan Keenan- Denver, North Carolina, USA
December 2, 2019
A. Hi Dan,
Chromic acid anodizing is considered fatigue neutral, so may be a way to go. The coating is only approximately 2-5 microns thick, so will not affect your dimensions, unless you are operating to very tight limits. You can NDT after this type of anodizing.
Another couple of possibilities for what are considered fatigue neutral anodizing, which are less hazardous to do are sulfuric-boric acid anodizing and sulfuric-tartaric acid
⇦ on
eBay
or
Amazon [affil link] anodizing. I've not played with these, so don't know if you can NDT afterwards, although I can think of no reason why you couldn't.
Aerospace - Yeovil, Somerset, UK
December 5, 2019
Brian, Thank you for the input. The customer has specified no anodizing, so regardless of type of anodizing, it is not acceptable.
Dan
- denver, North Carolina, usa
December 8, 2019
A. Hi Dan,
You could consider a conversion coating. This will not give you as much corrosion protection as anodizing, but you might be able to live with that, dependent on end-use. Look at coatings to MIL-DTL-81706
[⇦ this spec on DLA]
, Type 2 (non-hexavalent chromium conversion coatings), applied in accordance with MIL-DTL-5541
[⇦ this spec on DLA], Type 2. This is a very thin coating, which will not mask defects from liquid penetrant.
Aerospace - Yeovil, Somerset, UK
December 10, 2019

Q, A, or Comment on THIS thread -or- Start a NEW Thread