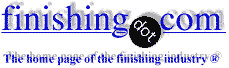
-----
Post-Nickel Plating Cleaning/Rinsing (critical cleanliness!)
Q. I have a small mild steel part (ring) with a glass to metal seal in the center that is ground flat then the assembly is nickel plated IAW FED-QQN-290 (replaced by AMSQQN290) . The next level assembly it is used in is very sensitive to any post plating residue (due to corrosion risk). The fused glass is quite porous so we are currently using a secondary rinse in acetone ⇦ on eBay or Amazon [affil link] Warning! Flammable! and ultrasonic vibration after the plating vendor's plating and rinse processes. Is there a better cleaning solution and method to keep the residue from the plating process to an absolute minimum? Are there any industry specifications that cover post-plating cleanliness or residue removal for residue sensitive parts?
Layne PetersonManufacturing Engineer - Salt Lake City, Ut, USA
2007
A. That would depend on what the offending material is. If it is organic, then your process should work fairly well. If it is inorganic, then a good grade of distilled or better yet DI water, warm, with ultrasonics would be far better.
James Watts- Navarre, Florida
2007
A. I don't understand how can a seal be porous? As I see it, if the plating liquid gets trapped in the glass, it means the fluid it is intended to confine may also escape through those pores. But anyway, perhaps masking the seal may solve that residue problem.
Guillermo MarrufoMonterrey, NL, Mexico
2007
Q. Thanks for the responses so far. One side of my part is ground flush after the glass sealing process, the metal ring and glass meniscus are both ground flat. After grinding, the exposed ground glass surface appears smooth but with a matte finish which actually contains very small channels and air pockets that are a natural characteristic of the frit fusing process (below the original surface meniscus). This is where the contaminants mostly reside after the plating and rinse processes. I would assume the contaminants from the plating process are mostly nickel salts and/or acids with whatever organics are present from drag out and handling. If I assume that I had both organic and inorganic contamination, would it be best to perform a rinse and ultrasonic vibration in acetone ⇦ on eBay or Amazon [affil link] Warning! Flammable! followed by a DI rinse and ultrasonic vibration? I also need a way to quantify the cleanliness. I am familiar with typical ionic contamination requirements called out for Printed Circuit Boards and I am considering calling out a similar requirement for my parts. Do any plating vendors currently perform this extensive of a rinse process followed by ionic contamination testing? Would this be feasible to expect this level of cleanliness from a Nickel plating vendor? Thanks in advance for follow on answers!
Layne PetersonMechanical Engineer - Salt Lake City, Utah, USA
2007
A. On metal parts, the best way to get solution out of the crevices is to limit the amount that got in. Have your plater do a 10 minute ultrasonic soak in very good DI water, say about 120 °F. Bring the parts out and cool in a rinse of room temperature high purity DI water. This will fill the pores with DI water and lacking the ultrasonics, I think that the water will not be replaced by any significant quantity of chemical solutions.
Your rinsing, ultrasonically, after plating would be best done by the plater, before the chemicals dry out and harden.
- Navarre, Florida
2007
Managing rinses between semi-bright & bright nickel tank and after bright nickel plating
Q. We have an automated electroplating line where we are plating motor cycle silencers and Rims etc.
We have Nickel Dragout after bright nickel plating. We are maintaining its temperature at 55 °C, pH 4.4 And running filter pump to keep it clean. However as the degree of dragout increase above 1 baumé. We immediately face problem in chrome passivation(grey smoke burnt silencer). The immediate solution is to drain nickel dragout and use fresh water.Due to heavy carry over in silencers , this is a major loss. Is there any way that we keep the nickel dragout at higher baumés and nickel does not become passive after dipping in nickel dragout? Is this due to some brighteners in the bright solution?
Secondly Should we use a dragout between semi and bright nickel. At the moment we are running it empty . Allowing time for it to drain in empty tank with no water.What is the general industry practice in this regard for using in between dragout for semi solution.
Best regards,
- Lahore, Pakistan
July 1, 2013
Q, A, or Comment on THIS thread -or- Start a NEW Thread