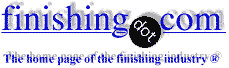
-----
Newbie on electroplating with acid copper
2007
Hi all,
Am in dire need of help. Am trying electroplating for PCB board and this is just the start. I did some reading/research on electrolysis/electroplating with acid copper. I began happily.
NO anode bag, NO phosphorised copper anode. Just pure copper for anode. Though I don't expect perfect result at the beginning, I don't understand some phenomena I observed. When I began with copper bars at the two ends and my cathode PCB board at the middle, I noticed a dark brown spongy substance on the cathode (yes, on the cathode please). It was soft and I was able to clean it with tissue paper. The copper clad board turned dull brown (dark brown). There's some coating on the anode but I feel that's normal (probably copper oxide). The current starts around 10 amps, then steadily falls to less than 1 amp and rise to about 3 amps again and some how stabilized.
Another strange thing I observed was that when I placed a nail as the cathode, the same soft spongy coating was formed. But this happened even if I don't connect the power supply with the nail cathode. The copper board cathode only forms the coating with power applied.
1. Could someone tell me what's this dark brown spongy coating on my cathode
2. What's the essence of phosphorised copper anode.
3. Is it possible to do without anode bag.
I really appreciate the help of the experts and many thanks.
Don
KFUPM (university) - Dhahran, Eastern, Saudi Arabia
First of two simultaneous responses --
Yau,
You did not mention the acid copper solution make-up. What is the copper sulphate, sulfuric acid, and chloride ion concentration? Phosphorized anodes help prevent the imbalance of Cu+ in solution, aid in better Cu grain structure. Poly pro anode bags should be used. What is the plating or exposed area to be plated? If you are starting with 10 amps you must have one half a sq ft total area on the PC board, is that right? Do you have air agitation in the tank? If not, you need it to supply fresh ions at the cathode. It sounds to me you have severe burning and are seeing cupric oxide at it's worst. After you research acid copper plating make sure you operate within all parameters stated in the research. Good Luck!
Process Engineer - Syracuse, New York
2007
Second of two simultaneous responses -- 2007
Don
You don't say why you are plating circuits but to answer your immediate questions.
1/ The spongy deposit is metallic copper. The cause is excess current. Aim for about 1 amp per square decimeter of plated area (not the overall size of the circuit board).
With the nail, not only is the surface area small - and hence the current density is very high - but copper sulphate
⇦ on
eBay or
Amazon [affil link] reacts with the iron to deposit copper without the need for current. In this case there will be very little adhesion. To plate copper on iron, you need copper cyanide or pyrophosphate solution. (You can use the sulphate solution but the current must be on when the nail enters the bath)
Acid copper sulphate is used for plating PCBs but only with the addition of proprietary organic additives. Without them the throwing power of the process is totally inadequate to plate down thru-holes.
2/ Phosphorised copper anodes are used to improve the dissolution. This is probably not needed for a small scale experiment.
3/ Anode bags contain the bits that fall off anodes - grains of detached copper and any non soluble impurities. These then get included in the deposit. For a small scale use you probably don't need them but a cotton bag is easy to make.
There is a lot more to learn if you want to make PCPs.
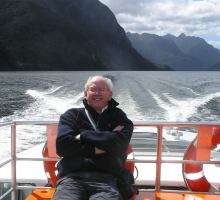
Geoff Smith
Hampshire, England
I agree with Geoff on everything except the cotton anode bags. Cotton does not fare well in acidic solutions. I have had my share of "retired blue jeans" as a testament.
Mark BakerProcess Engineer - Syracuse, New York
2007
2007
Thanks Mark and Geoff. I've been away on some other things after checking a number of times. I appreciate the expert help and it exactly matches my further research. I tested what I called spongy deposit with a multimeter and Alas! It was copper. So I realized the current density was too much. I reduce it. But now I get smooth pink deposit of copper. I sandpaper it and it shines. But I thought I could get shiny deposit by just electroplating.
I am now using phosphorized copper anode, I have a small anode bag. My solution is propriety and the company calls it acid copper 9711 and I've some additive they call ABC 971M copper additive (a brightener of course).
So why can't I get a shiny deposit? I really want to be lucky getting good result while still a newbie :) Hope that's possible.
Many thanks.
- Dhahran, Eastern, Saudi Arabia
Yau,
Watch the temperature, and make sure you have air agitation. Are you plating at the suggested current density? Is the substrate copper bright, and what is your dwell time?
Process Engineer - Syracuse, New York
2007
adv.: Supplier of Copper Anodes, Nickel Anodes, Bismuth Metal, & Other Metal Products for Industry & The Arts
Q, A, or Comment on THIS thread -or- Start a NEW Thread