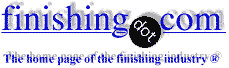
-----
Powder Coating a very detailed piece - no coverage problem
2007
We make detailed large birds and such of steel for outdoor decoration. These contain many cut ends and welds. We thoroughly sand blast clean before sending to powder coaters. 99% of the job is perfect, but, coaters can't seem to get powder into the crevices created by our designs. So after very little time outside small areas of rust appear - not good since we advertise our products as better than painted. Currently we have to spray paint all these areas after powder coating - not good again.
Can anyone suggest what the problem might be and how to over come it?
Thank you in advance,
YardBirds - metal art - River John, Nova Scotia, Canada
The problem is probably a "Faraday Cage" effect, whereby the electrostatics work out to block powder from reaching the recessed area. There would be a cost impact, but ideally you would electropaint these items before the powder coating.
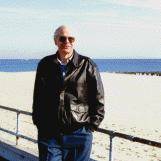
Ted Mooney, P.E.
Striving to live Aloha
(Ted can offer longterm or instant help)
finishing.com - Pine Beach, New Jersey
2007
A couple of other ways that powder coaters deal with this problem is to heat the part before it is painted, that way the paint melts into the corners effectively beating the faraday cage problem, then passed through the oven to fully cure the paint. You'll need to find someone experienced at using this method as it presents other hurdles to jump over that could cause quality issues. Something else would be submerging the part in a fluidized bed, it seems like your parts might be larger than average for a fluidized bed but you never know what you'll find as far as painters capabilities until you look. This method is just a variation of the other one in that the parts will be heated to a predetermined temperature before it is dipped, then the powder basically "melts" to the thickness that you want, covering crevices and corners that would normally be hard to reach using typical application methods, and then passed through an oven to fully cure.
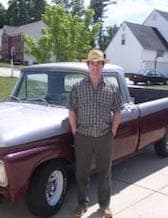
Sheldon Taylor
supply chain electronics
Wake Forest, North Carolina
2007
Q, A, or Comment on THIS thread -or- Start a NEW Thread