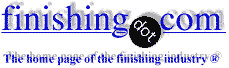
-----
Electroplating Wastewater Treatment Q&A's, Problems & Solutions
Q. I am curious about what is involved in re-programming an automatic/semi-automatic plating line with clean technology in mind, i.e. reducing drag-out and water consumption. It is difficult to convince operators that they can change the line without ruining their product. Also, I would be interested in where I might find information on the capital and operating costs for typical waste water treatment facilities at metal finishing shops.
Alan Gagnet1995
A. Hi Alan. Electronically reprogramming a programmed hoist line is generally relatively easy, say two days work total on average. But installing additional rinse tanks, etc., can be a major (and sometimes an impractical) undertaking. It is very difficult to give a canned answer to what is involved since it depends on how big the tanks are, how old, whether room exists to extend the line, and other factors, but it is often possible to add things like top sprays without major capital investment.
The EPA published their estimated costs several times in the development documents used to support EPA 40CFR413, 40CFR433, etc. The impacts of such changes and the associated costs have been constantly very severely underestimated by the EPA (which is probably only to be expected since they don't have to actually do the implementation with the many things that are usually forgotten, Murphy's Law, and that they have a vested interest in understating the cost impacts of their ideas) -- but their figures are pretty much universally available, and so they are a starting point for your study. They estimated the cost would force 20% of shops out of business, again a ludicrously low number as it turned out.
Some plating shops implemented things like "pollution control surcharge" at various times, and in my experience it was about 10%, but whether that was a realistic estimate or simply chosen as a palatable amount for their customers to accept is hard to say. Good luck.
Regards,
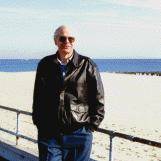
Ted Mooney, P.E.
Striving to live Aloha
(Ted can offer longterm or instant help)
finishing.com - Pine Beach, New Jersey
Q. [We are] a company settled in Turkey-Istanbul in snap fasteners and buckles field is looking for a proper water treatment for nickel salts and cyanide.
Any suggestions?
Thanking you in advance.
- Turkey
1998
A. Nickel and Cyanide must be separated because Nickel-Cyanide complex is very difficult to break down. You can use two stage cyanide oxidation processes for cyanide waste. A conventional heavy metal precipitation using caustic soda ⇦liquid caustic soda in bulk on Amazon [affil link] works fine with Nickel bearing waste.
by Clarence Roy
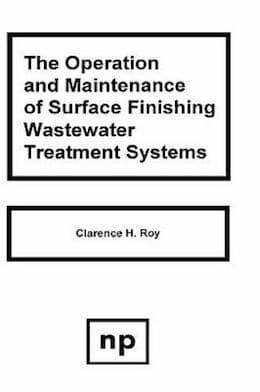
on eBay or Amazon
or AbeBooks
(affil link)
- Hong Kong
A. Hello Rifat. Here in the U.S., such a system would include a treatment step for destruction of cyanide by alkaline chlorination, a pH adjustment system for the nickel precipitation, and then separation of the precipitated solids with a clarifier. The sludges from the clarifier would be treated in a recessed plate filter press. That's certainly not the only way, but it's the most common approach. Good luck.
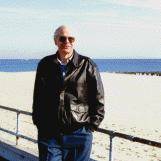
Ted Mooney, P.E.
Striving to live Aloha
(Ted can offer longterm or instant help)
finishing.com - Pine Beach, New Jersey
Q. Killing Cyanide from silver plating baths?
We are using an electroless silver plating bath for our (small volume) production of PCBs containing 1 molar solution of sodium cyanide and 0.1 molar solution of silver nitrate.
Can anybody provide instructions of how to get rid of a few liters of such a used solution (containing also copper). As we produce instruments (pH-meters etc) we can easily control the conditions of the process.
Thanks
scientific instruments
1998
A. 1 Molar NaCN = 49 grams NaCN/liter = 6.5 ounces/ US gallon. Alkaline chlorination is NOT recommended for concentrated solutions because of dangerous side reactions like poisonous gases, and eruption. The reaction in dilute solutions is the following formula (reference, Graham's "Electroplating Engineering Handbook" ⇦ this on
eBay,
AbeBooks, or
Amazon [affil link]
, 3rd Edition, VanNostrand, New York).
2NaCN + 5 NaOCl + 2NaOH = 2Na2CO3 + 5NaCl + N2 + H2O
In electroplating wastewater, where alkaline chlorination has been used for many years, the cyanide concentration may be only a few hundred mg/liter and the rest of the components of the original solution have also been diluted. Bleach
⇦ bleach/sodium hypochlorite in bulk on
eBay
or
Amazon [affil link]
is added, with good mixing, to a permanent blue reaction to Potassium Iodide
starch paper
[affil link] as an endpoint, and/or watch the reaction with an Oxidation-Reduction Potential electrode.
Whether your plating bath is proprietary or not, it may be worthwhile to reclaim the silver, and avoid a waste treatment job. Even if you have an exemption to waste treatment due to laboratory status, it is still not a good idea to dump cyanide down the drain.
Perhaps there is someone in your area who reclaims silver from medical film who could take the solution? I don't know if they still use cyanide in the process.
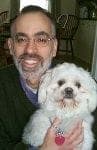

Tom Pullizzi
Falls Township, Pennsylvania
Q. I have read about using hydrogen peroxide to treat cyanide.
Unfortunately not much information was given. If anyone knows of the correct process, please let me know.
Thanks.
Tech-Etch
1998
A. I believe that there may be several patents and/or proprietary processes on the subject. A literature search may give you some leads.


Tom Pullizzi
Falls Township, Pennsylvania
A. Hello David. I believe that you will find this was originally called the "Kastone Process" if you wish to try googling it. This was a DuPont process, but they no longer support cyanide-based plating, so I doubt that they are still marketing it themselves. Still, it should be a good search term for you.
Happy hunting.
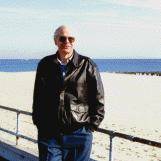
Ted Mooney, P.E.
Striving to live Aloha
(Ted can offer longterm or instant help)
finishing.com - Pine Beach, New Jersey
Q. Hello!
I need material about minimization of water consumption in the finishing industry for my thesis.
Thank you!
Universidade Federal de Santa Maria - Brasil - Santa Maria, RS, Brasil
2002
A. Hi Marta. Back in 1982 I wrote a pamphlet entitled "20 Ways to Reduce Water Usage in Plating Shops", and it's now in our on-line library.
Luck & Regards,
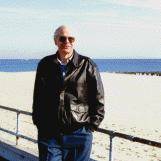
Ted Mooney, P.E.
Striving to live Aloha
(Ted can offer longterm or instant help)
finishing.com - Pine Beach, New Jersey
Multiple threads merged: please forgive chronology errors and repetition 🙂
Q. From history, my WWTP effluent could comply to Malaysia's limit of 1.0 mg/L for nickel. however, recently, the limit could not be met and nickel has been in the region of 1.3 - 1.8 mg/L. We are currently operating at pH 9.5 for to precipitate all heavy metals (Ni, Zn, Cu, Mn, Boron). FYI, my WWTP is servicing electroplating and paint shop wastewater. There were no changes in the process at WWTP and in the plant.
Afifcar assemblies - Kuala Lumpur, Selangor, Malaysia
2007
Tip: This forum was created to help build camaraderie through sharing tips, opinions, pics & personalities.
The operator & those readers who want that might not engage with anonymous posters.
A. A pH of 9.5 is a bit low for Ni.
Your best bet would be to add a bit of sulfide type precipitant, such as sodium sulfide, or dimethyldithiocarbamate. This would be a lot more forgiving than 'plain vanilla' hydroxide precipitation.
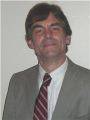
Dave Wichern
Consultant - The Bronx, New York
A. Good afternoon:
You didn't mention whether the nickel present in the wastewater discharge is dissolved nickel or nickel bearing suspended solids which passed through your treatment system. I'll assume that its dissolved nickel that's causing your problems.
As a preventative measure, if you are using cyanide based solutions in your finishing operations, please make sure you are not accidentally mixing cyanide bearing wastewater and nickel bearing wastewater. Nickel-cyanide complex can be tough to waste treat.
If you don't have a problem with nickel-cyanide complex, then the sulfide or carbamate additions mentioned by David Wichern are a great idea. Just remember not to exceed the recommended dosage; use only enough to precipitate out the stubborn metals in solution. Carbamate compounds are toxic to marine wildlife.
- St Louis, Missouri
by Matsuo Tomonori (Editor)
Amazon
on AbeBooks
(affil link)
A. Not only that: if you use too much, it won't work as well. This is of particular concern with DTC, because getting rid of an excess is not so easy. You wind up with this unbreakable tea colored colloid. To break it, you need to add a bunch of ferrous or alum or something. It's a real pain in the neck.
That is why I always liked sodium sulfide. Easy to get rid of excess S2-, just blow air through it, or add some hypochlorite. Unfortunately, NaS2 has some OSHA issues associated with it that make people not want to have it in the plant.
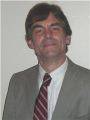
Dave Wichern
Consultant - The Bronx, New York
A. Before deciding that DTC is preferable to sodium sulfide or simple lime precipitation, readers should see:
www.state.in.us/idem/your_environment/wrcac/whiteriver/complaint/complaint.pdf ⇩
![]() |
opinion That paper describes a pollution catastrophe -- 187 tons of fish killed in the White River in Indiana due to a gross, excessive discharge of DTC from an electroplating plant. As far as I can determine, this was by far the worst pollution incident ever caused by an American electroplating plant ... and ironically it was not from an electroplating waste,it was from a treatment chemical no plating shop anywhere ever wanted to have on hand but which was required to meet over-the-top discharge standards. An interpretation which probably resonates with platers is that when you are relentlessly pressured to use incredibly powerful toxins like DTC to remove that meaningless last fraction of a milligram of metal, you open the door for accidents like this. ![]() Ted Mooney, P.E. Striving to live Aloha (Ted can offer longterm or instant help) finishing.com - Pine Beach, New Jersey Ed. update: The above link is broken. Thankfully, the Internet Archive preserved a copy here
|
A. In addition to environmental considerations, a practical problem often occurs in lowering [Ni] using DTC or soluble sulfide: As the DTC lowers [Ni] and other metal concentrations, previously precipitated hydroxides such as Ni(OH)2 dissolve toward maintaining their equilibrium Ni, Cu, Zn, etc. solubilities. One may end up using very large amounts of DTC precipitating all metals. Hence, precipitation with DTC or soluble sulfide should only be used as a 'polishing' treatment on filter press effluent water. In which case, it's easier to do a 2-stage pH precipitation, removing most metals at pH 8.5 and residual Ni, Zn, etc. at pH 10.5.
Possibly, Ni-containing waste waters can be segregated and treated separately.
- Goleta, California

Rest in peace, Ken. Thank you for your hard work which the finishing world, and we at finishing.com, continue to benefit from.
A. Dave: Good point about sulfide, and thanks for it. Sulfide is a much stronger precipitant than hydroxide, but I've done a lot of jar testing and found it not as effective as DTC at approaching zero concentration of metals.
Ken: I totally agree that we shouldn't use DTC in the first stage of a wastewater treatment system, and should reserve its use (if used at all) for segregated polishing of what's left after the precipitants from hydroxide precipitation have been removed. But I don't think much precipitation happens at pH 8.5; about the only thing that comes out in many shops at that pH is iron.
I think the right approach was developed by Dr. Lancy long before the EPA even existed: hold the pH low or make it low; add ferric chloride
⇦ on
eBay or
Amazon [affil link] or aluminum sulphate or other material as a co-precipitant/chelate breaker; then raise the pH to 10.5; filter or clarify; finally, reduce the pH to acceptable discharge point. If this doesn't reduce the contaminants to a low enough level to comply with the law, change the process chemistry or change the law because the treatment regimen was right -- the use of DTC is a very dangerous step in the wrong direction :-)
The above assumes, of course, that we consider end-of-pipe treatment of "mixed metals" satisfactory; and that premise should be continually reexamined as times change -- just because we used to mix them doesn't necessarily mean we should continue to do so.
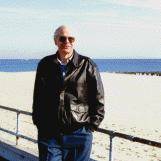
Ted Mooney, P.E.
Striving to live Aloha
(Ted can offer longterm or instant help)
finishing.com - Pine Beach, New Jersey
A. Malaysia in particular has a tough go from a discharge standard, as they are usually put into categorical standards known as Malaysia a or Malaysia b, both of which exist based on WHO water standards. Usually, they do not have the luxury of a secondary or tertiary POTW, so the use of DTC is out - they don't even set limits on it (but there are limits!) Sulfide works, however you also have sulfide standards for discharge, as well as chlorine (for those of you that want to use a little hypo to destroy the sulfide). Lastly, with all this treatment, there is (or at least was) a TDS limit, so adding a raft of chemicals to treat this is probably not the panacea that it may be here.
You didn't mention what type of nickel it was - the originating bath, so the final treatment technique could be hard to find. If its chelated at all - you cannot treat it - even with Doc's method, unless you get rid of the chelator, or tie it up. Iron does that, but there are sulphate and chloride discharge standards to consider as well. Let's not forget, while KL is a BIG city, its treatment works are not what they are here -- and unlike people here that depend on well or tap water to live. There are still many many people that live by the rivers there -- washing, drinking, existing etc. That's why the WHO standards are there. They don't have the benefit of chlorination at every point.
I might suggest ion exchange as an alternate, depending on the origination of the nickel and the form, either on a point of use basis, or end of pipe if necessary, but controlling it POU is a heck of a lot easier and more efficient -- and cost effective. It can usually easily get well below the discharge point before the stream is commingled with the effluent, and once mixed, it could be virtually undetectable in the final outfall.
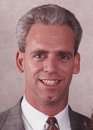
Tom Baker
wastewater treatment specialist - Warminster, Pennsylvania
Thanks, Tom, for reminding us that the question was about a discharge situation in Malaysia, not here, and that others don't necessarily live the same way we do :-)
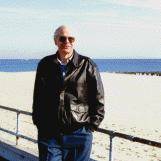
Ted Mooney, P.E.
Striving to live Aloha
(Ted can offer longterm or instant help)
finishing.com - Pine Beach, New Jersey
A. It is true that there are discharge standards for sulfide - I operated under a pretty tough one (0.5 mg/l, Santa Clara, CA) for some years. Either because I used sodium sulfide in conjunction with ferrous sulfate
⇦ on
eBay or
Amazon [affil link] , because I was treating fairly small batches (2,000 - 3,000 gallons) or because the sulfide ion is so easily oxidized, I never had a problem with it. I used to batch treat, and I'd add many pounds of sodium sulfide to batches. I never had to treat for residual sulfide with hypo or peroxide or anything else. Just the O2 diffusing into the treated water through the surface took care of any excess. The treated decant ... well, I wouldn't put it up against Chanel #5 in a Sweet Smelling Derby, but it didn't reek of H2S, either.
Tom is, of course, correct in saying that the best solution to the problem is POU control - don't make the problem in the first place! That is perhaps the wisest word yet.
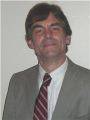
Dave Wichern
Consultant - The Bronx, New York
A. Dear Sirs,
I was browsing the Internet in search for information for a presentation on electroplating effluent treatment when I happened to find your discussion on nickel problems.
I was a little surprised to see that the Degussa trimercapto-s-triazine, marketed as TMT 15, was not mentioned at all. TMT 15 should solve the problem easily and without toxicity.
Best regards,
- Nummela, Uusimaa, Finland
Thanks, Esko, you are right, it should have been mentioned! It's reportedly less toxic & environmentally safer, but I'm no biochemist and don't pretend to actually hold an opinion on that.
Still, a paper, "A Non-toxic Alternative to Metal Precipitation", by its own proponents Norcross & Peldszus of Degussa, states that TMT15 has "difficulty with Zn and chelated Ni", and "For treating strongly complexed metals, DTC is the most effective."
Luck & Regards,
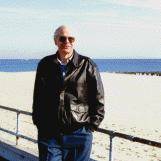
Ted Mooney, P.E.
Striving to live Aloha
(Ted can offer longterm or instant help)
finishing.com - Pine Beach, New Jersey
A. I routinely get under 1 ppm nickel but my method may not be applicable to your waste plant. I precipitate at pH 10.5 or 11 first, allow to settle, correct the pH and then discharge. I can do this because I have reduced the quantity of water used so much that I have days between discharges.
Nick Clatworthy- Whitstable, Kent, UK
2007
Q. Hello everyone. We electroplate Nickel, Zinc (alkaline and acid), copper, and tin. Mostly we plate small parts such as fasteners. We are running barrel line style plating. The stripping operation uses Nitric acid in a cement mixer tumbler to strip the copper off steel fasteners before it is sent to the wastewater treatment.
I'm new to the industry and have come upon a problem that needs some insight from the experienced. After taking charge of a smaller plating shop and wastewater department, I found some things that needed changing. One was reduction of water use in shop. This lead to the reduction of about 6000-8000 gallons of water in a 24 hr period (rinse tanks were putting out 40 gpm). After this change, I am having a tough time getting the copper out of the wastewater. I believe that part of the problem is that we have a stripping/cleaning operation for parts. We strip a lot of copper off parts and this waste goes down into the wastewater treatment. All that extra water just diluted everything before, so the levels were acceptable for the POTW. I think the copper is tied up with some chelating agent ... but need some advice on how to tackle this.
Head of Plating and Wastewater Treatment - Altoona, Pennsylvania, USA
2007
by Clarence Roy
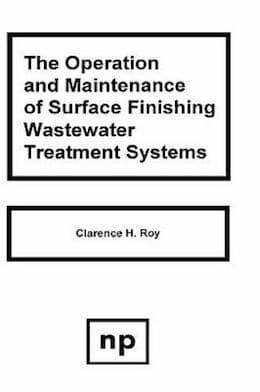
on eBay or Amazon
or AbeBooks
(affil link)
A. Chelate breaking usually involves reducing the pH to about 4.0, maybe lower, and then supplying another ion like aluminum (from aluminum sulphate) or iron (from ferric chloride ⇦ on eBay or Amazon [affil link] ) or perhaps magnesium from epsom salt [affil link] to replace the problem metal, then raising the pH quite high, Clay. Try it in the lab to see how high you can keep the pH when you lower it, how low you can keep it when you raise it, and which co-precipitant works best. People hate the operational mess of lime, but it combines the co-precipitant/chelate breaker with the pH raiser and may be best. Good luck.
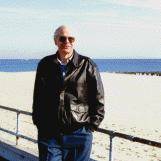
Ted Mooney, P.E.
Striving to live Aloha
(Ted can offer longterm or instant help)
finishing.com - Pine Beach, New Jersey
A. Are you doing acid zinc plating with a bath that contains ammonium ions?
If so, that might be the cause of your problem. At pH 10, there's enough free ammonia to cause complexation problems. If that's your situation, try precipitating at a lower pH, perhaps 9 or so, with a product like DTC or sodium sulfide.
Funny, eh, that the enforcement authorities should not be a little more helpful when you're doing a good thing and conserving water? Once, I got dinged for Zn being about 20% high in a batch of water that I had discharged. This water had been recycled twice and had a TDS of about 15,000 ppm.
Funny, the priorities people have. It's a perverse incentive to leave well enough alone and just leave the water turned up.
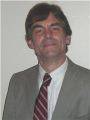
Dave Wichern
Consultant - The Bronx, New York
![]() |
Yet somehow "consistent compliance" as used in the regulating documents morphed into meaning "flawless compliance" -- which produced this upside-down logic that you describe. If your effluent meets the standards 99 to 99.9% of the time, how could anyone argue that your compliance is not amazingly consistent? Yet these days you'll be fined for a single error. ![]() Ted Mooney, P.E. Striving to live Aloha (Ted can offer longterm or instant help) finishing.com - Pine Beach, New Jersey
![]() Dave Wichern Consultant - The Bronx, New York |
A. As metals enter the treatment process, they are in a stable, dissolved aqueous form and are unable to form solids. The goal of metals treatment by hydroxide precipitation is then to adjust the pH (hydroxide ion concentration) of the water so that the metals will form insoluble precipitates. Once the metals precipitate and form solids, they can then easily be removed, and the water, now with low metal concentrations, can be discharged.
Metal precipitation is primarily dependent upon two factors: the concentration of the metal, and the pH of the water. Heavy metals are usually present in wastewaters in dilute quantities (1 - 100 mg/L) and at neutral or acidic pH values (< 7.0). Both of these factors are disadvantageous with regard to metals removal. However, when one adds caustic to water which contains dissolved metals, the metals react with hydroxide ions to form metal hydroxide solids:
During this process I would keep the pH 8.0 to 8.5 SU.
- Dayton, Ohio
January 10, 2008
A. Chris,
You are correct in general with your statements concerning metal hydroxides and pH. If there are chelates present the whole world can change. I would suggest that Clay investigate possible sources of chelates, burnishing compounds, etc.
The whole regulatory issue is/could be a never ending discussion. We have an RO unit to produce water that we can recycle. The nature of this beast is it concentrates our discharge. When we get close to the limits we turn off the unit and stop recycling. The real dichotomy here is that we are sending the same total pounds of metal to drain. The POTW would never know the difference either way because we are such a small part of their total treatment.
I understand that there are discussions by those in the compliance field about possibly changing the regs from concentration to total pounds or some combination of the 2. Let's hope clearer heads prevail.
- Inman, South Carolina
Ed. note: Exactly, Kurt. To a great extent we are regulating the discharge of totally harmless water instead of regulating the discharge of the harmful compounds in it. Same thing with sludge disposal; people sometimes deliberately keep it wet and messy, any pay for the disposal of the harmless water they leave in it, to pass maximum concentration tests 🙂
Multiple threads merged: please forgive chronology errors and repetition 🙂
Q. I am making tests for removal of Nickel (doesn't react with hydroxide and sulfide) using product Bulab (Buckman) that is the base of DTC.
However when we reduced the pH to < 2 it forms a brown precipitate that if it is separated presents better efficiency. Which is the best pH for use of DTC?
Which is dosage of DTC so that the final wastewater treated is not toxic?
- Jundiai, São Paulo, Brazil
February 25, 2010
A. Hi Tatiana
I really don't think those are the proper questions because DTC should NOT be used for primary reduction of nickel in wastewater, only for final polishing.
If hydroxide is doing nothing, you must implement chelate-breaking as described on this page, then follow it with hydroxide precipitation, and get that precipitated sludge separated from the wastewater, so you use DTC only on the nickel left in the clarified water. Ion exchange or other processes might, of course, be more suitable for your specific situation.
Luck & Regards,
Ted Mooney, P.E. RET
Striving to live Aloha
(Ted can offer longterm or instant help)
finishing.com - Pine Beach, New Jersey
Q. I have some questions, currently the chemicals that I have used in WWTP are coagulant, polymer neutralide, and decomplex 200, so what is the way to reduce the nickel value?
wan muhammadtnp - Pahang, Malaysia
July 18, 2018
A. Hi Wan. The first step is jar testing while adhering to the basics. If you can't get proper levels in jar tests with the basic approaches, then you would need to either see how to modify the process which is generating the nickel problem or start applying more complex reductants like TMT-15 or sulphides or DTC.
What is the source of the nickel, what other processes mix with it before WWTP, and what pH do you precipitate at? What is the allowable nickel ppm in the discharge, and what is your current dissolved and filterable nickel in ppm? Thanks.
Regards,
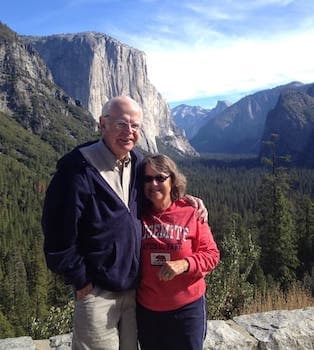
Ted Mooney, P.E. RET
Striving to live Aloha
(Ted can offer longterm or instant help)
finishing.com - Pine Beach, New Jersey
A. Hello Mr. Muhammad,
Check the source chemical for addition of a chelating agent, which will make your treatment method more difficult. For example, the ubiquitous Reliant Nickel acetate seal has a chelator added. To perform a 'destruct' rendering it possible to separate as solids and clean dischargeable wastewater, it must be brought to pH greater than 11 to break the chelation effect. We don't have to use any polymers etc to do this, just solid sodium hydroxide added while mixing (watch your temperature!). If a smut reducing additive has been put in the bath, which contains even more chelator, an additional first step may be necessary, which is to first drop the pH to about 3.5 using ferric chloride (about 1 kilo per 1000L) and then Nitric acid to further reduce the pH. Then proceed bringing the pH way back up again. Not knowing what exactly you are starting with, this is just a simple example of one way to deal with a heavily chelated plating chemical.
As Ted says, you'll want to jar test before trying to full-scale the treatment process. Good luck!
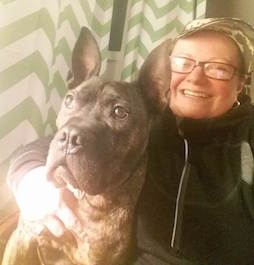
Rachel Mackintosh
lab rat - Greenfield, Vermont
A. Hi All
Excellent advice on the treatment of waste water but I would suggest that there is another approach.
If expensive chemicals do not enter the waste stream they do not have to be removed by even more expensive treatment.
Assuming we are discussing plating wastes, I would look first at the plant and its operation. Much can be achieved by …
Jigging with minimal solution traps (not so easy on a barrel line).
Counter-flow rinses
Adequate draining time over the tank (without drying out); Operators rarely understand the importance of this.
Fine demin spray rinse over the tank; With a little practice you can balance evaporation/dragout losses, you save chemicals ($s) and never have to top up again!
Recirculated rinses with deioniser.
It is possible in some cases to completely eliminate the need for any effluent treatment.
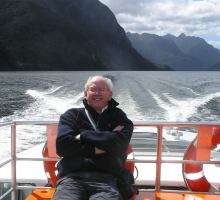
Geoff Smith
Hampshire, England
Q. Good night everybody!
I really need your help.
Actually I am treating a wastewater which contains nickel, cooper and cyanide. First, in order to removal cyanide, we use hydrogen peroxide at pH 10.5 for one hour. Then, we treat those heavy metals by using NaOH and ferric chloride carrying the process until about pH 8.0 - 8.5. We have measured total cyanide after this process with results less than 0,1 ppm, but nickel and copper are still there. No matter how we adjust the pH value to precipitate, they persist. We also have a very high COD about 1400 ppm. I really appreciate some advices here. Thanks a lot!
- Bogota Colombia
September 30, 2020
A. Hi Carolina. We added your inquiry to a long thread on the subject, which should offer food for thought. You might also look at thread 40394, "Cyanide plating waste water treatment", for additional insights. But just for four quick thoughts:
1. You must figure out where the 1400 ppm of COD is coming from, not only to control it, but because it might be interfering with the nickel removal.
2. Filter a sample of the wastewater before testing so you are sure whether the excess nickel is in dissolved or precipitated form so you know whether the chemistry or the solids-liquid separation step must be improved.
3. Just a reminder that you do jar testing to figure out what will work, you don't make adjustments to your treatment regiment based on untested theories.
4. ferric chloride is a chelate breaker/co-precipitant and there may be better ones; but what the word 'co-precipitant' implies is that you add it before things are precipitated, not after. The idea is that there is a limit to the total metal that can stay dissolved at a given pH and if you add iron or another metal it reduces how much nickel can stay dissolved. If you're sure that cyanide is absent, lower the pH in your beaker [beakers on
eBay
or
Amazon [affil link] to 3.5 with acid, then add the co-precipitant, then raise the pH to 11+ and see if there is improvement.
Luck & Regards,
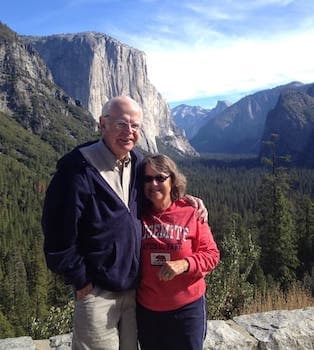
Ted Mooney, P.E. RET
Striving to live Aloha
(Ted can offer longterm or instant help)
finishing.com - Pine Beach, New Jersey
A. You may have chelators or ammonia that are interfering with metals precipitation. I'd recommend that you jar test with a stronger chelate breaker.
Lyle Kirman- Cleveland Heights, Ohio
Thank you both for your answers.
We tried to coagulate the water after the oxidation process and just before the addition of FeCl3 seeing a little improvement related to COD removal. I guess we should try using another breaker culture as you suggested, Do you have any recommendation of the product we could possibly use?
Thanks a lot!
- Bogota Colombia
October 3, 2020
A. Hi Carolina
Keeping the cyanide waste out of the picture, you could easily do jar tests with pH 3.5 and test additions of calcium, aluminum sulphate, ferrous sulfate, or magnesium sulfate, then raise the pH to 11.5, filter it, and test for dissolved nickel content.
Luck & Regards,
Ted Mooney, P.E. RET
Striving to live Aloha
(Ted can offer longterm or instant help)
finishing.com - Pine Beach, New Jersey
Q, A, or Comment on THIS thread -or- Start a NEW Thread