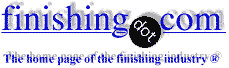
-----
Effect on adhesion from various heat treatments to electrolytic nickel over 400 series stainless
[an error occurred while processing this directive]We regularly receive 400 stainless parts and rack plate them with electrolytic nickel using standard stainless cleaning, activation, and plating practices. Recently we have had some problems with adhesion.We have traced the problem down to the parts as received. It appears that the critical variable is the heat treat process.It turns out that different lots of incoming parts have experienced different heat treat cycles. Does anyone have any experience with the effects of various heat treatments on adhesion? All parts plate ok. The problem is only evident during adhesion testing. Thanks in advance.
Dan Friel, JrEdgecraft Corp - Avondale, Pennsylvania
2007
As you found out, heat treat does make a difference. Both the iron and the chrome oxidize in the furnace. You may have to use an electrolytic etch or very lightly aluminum oxide (fine) abrasive blast to get good adhesion. I liked a woods nickel strike with a higher HCl content and a lower nickel as metal content. It sticks better in my experience.
James Watts- Navarre, Florida
2007
I would definitely go with the Wood's Nickel strike, or possibly a Nickel Chloride Strike. In my experience, taking my standard Nickel Chloride bath, and lowering the pH to about 1 using HCl did the trick for adhesion on SS. Now I have Wood's Nickel Strike that I use for this application, and it has always worked quite well. Good Luck.
Michael Berrier- Addison, Illinois, USA
2007
Q, A, or Comment on THIS thread -or- Start a NEW Thread