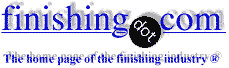
-----
Inconsistent black color tone and gloss level with type 2 class 2
We specify black anodize Type 2, Class 2 on either 6011-T6 or 2011 Alum. We are anodizing very thin ( 0.18 mm) aluminum. Rarely do we mix the two alum alloys in one batch of anodize. We use black anodize for cosmetic reasons more than for corrosion resistance. We do not add coatings after anodize. We do expect Epo-Tek 301 epoxy to adhere our glass inserts to the anodized aluminum. I have read the MIL-A-8625 / MIL-PRF-8625
[⇦ this spec on DLA]F spec and do not believe there are any statements discussing my concerns. We had a great supplier for years; management deemed it necessary to find a cheaper source. Now we have 2 sources; neither of them the trusted, consistent vendor we used for years. Now we are getting such variation in the depth of black and gloss level. We are also having failures to our final product in that it is gaining moisture over time. Here are my questions:
1. How does the anodizer control the depth or intensity of the black?
2. What guidelines can be used to specify and certify the black?
3. How does the anodizer control the gloss level? I actually need a medium glass to almost flat glass to avoid unwanted reflected light.
4. What guidelines can be used to specify and certify the gloss level?
5. What information is there on the porous outer surface of the anodize hydroscoping?
optical filters - Brattleboro, Vermont, USA
2006
2006
I think there's something to be learned here that is only tangentially related to your five questions, Natalia, but which our readers have already heard me say many times: cost reduction programs never work :-)
1. Decorative anodized coatings can range from about .0002" thick, even less, to about .001" thick. The thickness is directly proportional to the time that electricity is applied to the parts while immersed in the anodizing tank. Thus .0008 inches will take twice as long and twice as much electricity as .0004". The black dye is absorbed into pores in the anodized coating, and good saturation and consistency require that the anodizing be thick enough. Some quality anodizers (perhaps including your original one) insist on anodizing in the .0006"+ range for black parts. Other shops will naturally say that half of that is "good enough". The first thing I would do is have the thickness checked on parts from all three shops.
2, 3. After you've agreed on a thickness spec, then you need to agree on a black dye. An anodizer who insists on buying only quality dyes will get more consistent color than an anodizer who buys a sale brand. Of course, there's more to consistent color and gloss than just anodizing thickness and dye quality -- there's prep, cleaning, etching, desmutting, dye temperature, rinsing, and sealing. A matte appearance usually comes from consistent etching, but sometimes from acid treatment or scratch brushing.
4. Sorry, I can't personally answer this one.
5. I don't quite follow your thinking on this question, as the word 'hydroscoping' isn't familiar to me. There are plenty of good books on anodizing, but I don't think you'll find the word there either. But after anodizing, the parts are immersed in water based tanks which deliberately cause the aluminum oxide coating to absorb water and swell into a mix of oxide and hydroxide, which I think is called boehmite. This operation is called sealing, but it's not a topcoat, it's that conversion process. The parts should be well sealed, so any 'hydroscoping' pertains to something that happens only before the parts leave the anodizing line. Good luck.
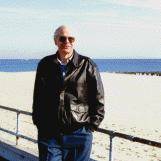
Ted Mooney, P.E.
Striving to live Aloha
(Ted can offer longterm or instant help)
finishing.com - Pine Beach, New Jersey
Q, A, or Comment on THIS thread -or- Start a NEW Thread