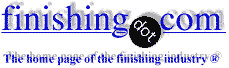
-----
Microhardness differences with 200g and 500g loads
2000
Q. I am checking the decarburization level of a sample of 4150 at 46-48 HRC by taking micro indentions at .002, .003,... .010" from the surface of the sample, and comparing with the core material (at .015-.025" from the surface), and looking for a microhardness at the surface of (core - 20 points knoop) per MIL-H-6875 rev.H.
When I check my samples with a 500g load, I am consistently showing a decarb depth at .004-.005" depth (out of spec).
When I check the samples with a 200g load, I consistantly show a decarb depth of .002 MAX, and in some cases, I show no apparent micro hardness change of more than 10 points Knoop (!)
I am checking the core hardness at six places, at no less than 3X diameters of the indent, and averaging the 6 readings. My .002-.010" indentations are spaced such that no 2 impressions are within 3 diameters of any other impression.
My tests are repeatable on 4 different locations on each of 4 different samples to within a few points knoop, yet the different loads show drastically different results.
My microhardness tester (Buehler) is calibrated weekly to a 500g standard, and I have now calibrated it on a 200g standard.
I have always used a 500 gram load, but a new vendor is using a 200 gram load.
Is there a 'right' or 'wrong' load? The only references I can find give an allowable range of 0-1000 g, but I cannot find a 'preferred' load.
I guess my most pressing question is, Why is there such a difference between the 2 loads?
Greg Hyman- Dayton, Ohio
A. The preferred load will be 500 gm
radhika- Chennai; Tamilnadu; India
2001
A. With these tests at 300 grams, we may see an apparent increase in hardness with the decrease in load. This can/is primarily caused by errors in the determination of the size of the indentation and variations in the elastic recovery of the indentation. As the size of the indentation decreases, our readings can be less accurate due to any of the forementioned factors. Also, the properties of the material, the size of indentation and their relation to the stress-strain curve of such, can lead to inaccuracies in our readings. In addition to the above mentioned, formation of a bulge as well as other characteristics of the indentation itself can cause variations on our readings, depending on the load. In Vickers, load indentations can also be too small to explain load dependence when it comes to elastic recovery of the indentation.
In general, the indentation is made as large as possible to obtain greatest accuracy. As long as we use a single load throughout our tests, we will be fine. Using different loads in any of our tests can alter our readings. The lighter the load, the more significant change. In any comparison, Knoop hardness numbers with loads of less than 500 grams and Vickers hardness numbers less than 100 grams are considered invalid, unless we take into consideration the load dependence.
- El Paso, Texas, USA
March 9, 2016
Q, A, or Comment on THIS thread -or- Start a NEW Thread