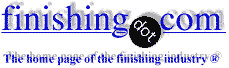
-----
Recommend a Finish for AISI 1095 Carbon Steel
Q. Hello Fellow Tank Jockeys. I rarely deal with heavy Iron but today I have a precision part made from AISI 1095 Spring Steel via WirenEDM process and I am taking recommendations on a surface finish. I would like the part to resist corroding by some passive treatment, not an electrodeposit. Later on maybe I'll deposit some Parylene. But for now, what can you Steel Finishers Commonly do with AISI 1095?
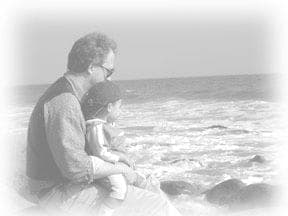
Dave Kinghorn
Chemical Engineer
SUNNYvale, California
2006
A. As far as I know, there's nothing inside a 1095 carbon steel that could render it passive. It will always be reactive and thus subject to corrosion and oxidation. You have to add something on top of it, be it paint, a protective metal or alloy (either sacrificial or isolating), a stable oxide, nitride or intermetallic compound, an imposed galvanic current or a combination of these. Maybe someone else will differ and enlighten us.
Guillermo MarrufoMonterrey, NL, Mexico
A. You might try heating it up and dunking it in vegetable oil or boiled linseed oil ⇦ on eBay or Amazon [affil link] , and reheating to a lower temp.
James Watts- Navarre, Florida
Q. I often hear the Steel people talk about Phosphatizing, Blueing, Blackening, etc. Are any of these finishes applicable?
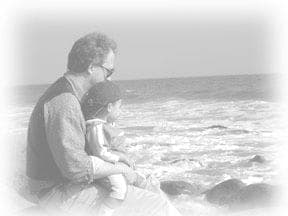
Dave Kinghorn
Chemical Engineer
SUNNYvale, California
A. Hi Dave. Phosphatizing is a conversion coating with zinc or manganese phosphate or similar coatings, usually designed either as a pretreatment for painting or as an oil-holding surface for machined parts. I don't think it's usually used under Parylene coatings, but I think it could be.
Black oxiding and bluing are actually about the same thing, a controlled oxidation of the surface of steel to a depth of only a few millionths of an inch. It's done more for appearance than corrosion resistance and requires waxing or oiling to deter rusting.
I think your situation will be that these processes can be done but will impart little corrosion resistance if oiled and essentially none if not.
One thing that might help is nitriding, whether it be salt bath nitriding, gaseous, or plasma. You might look into the QPQ (quench-polish-quench) process. I am not sure if AISI 1095 is a good candidate steel for QPQ, but I'm sure the vendors of the process could tell you in an instant. Good luck.
Regards,
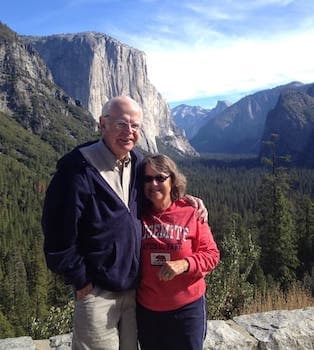
Ted Mooney, P.E. RET
Striving to live Aloha
(Ted can offer longterm or instant help)
finishing.com - Pine Beach, New Jersey
Q, A, or Comment on THIS thread -or- Start a NEW Thread