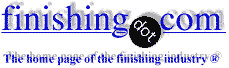
-----
Rust issues using Manganese Phosphate on 4130 cold drawn steel parts
2006
I am having rust issues (after Salt Fog Testing) on tubular parts made up of 4130 cold drawn steel. The process is as follows:
1. CLEANING OF METAL: (I truly believe this is where the PROBLEM is). I've tried several different methods to clean the tubing. First of all, the tubing has NO scale, only a thick oil/grease to prevent rust. The tubing is also quite smooth, not rough at all. I have tried four (4) different means of cleaning: Sand Blast with a fine glass bead, Acid Dip at approx. 150 F at cycles of 10 - 30 minutes, Acetone cleaning and Alkaline cleaning.
2. MANGANESE PHOSPHATE: This is an immersion process. Temperature at
205 F, Titration 9 - 10%, and cycle times between 15 to 45 mins. The parts are rinsed and immediately blown dry.
3. CHROMIC ACID (SEALER): Temperature 160 F, PH approx. 3.5, cycle time 1 min. 15 sec., Parts are NOT rinsed, yet are blown dry.
4. SALT FOG TEST: Parts remain in chamber for 1.5 hrs., NO oil coating.
I have run many parts (not the tubing) through the above procedure, and have had a few issues along the way, but have been able to resolve them....most of the issues I've had HAVE been "CLEANLINESS" issues, I have recently concluded. The parts that I have most recently run through the above processes pass the Salt Fog Test with no sign of rust. However, this darn tubing is testing my patience! :)
The tubing ultimately will be oil coated (NOT painted), so the finish MUST be 100% right.
Are there any ideas, tips, hints, clues or changes to the Cleaning Process? I'm all but convinced that the Phosphate process is correct, due to the other parts passing the identical Salt Fog Testing.
- Estill Springs, Tennessee, USA
First, skip the acid dip, it makes the coating coarse and less protective.
Second, you must use a grain refiner ahead of AISI 4130. If your mag phos vendor does not offer one, then get a new vendor.
Third, adjust the total/free ratio to 7.5/1 at the tank, just before you put the work into the bath. If you adjusted the ratio yesterday, it has changed while boiling away waiting for you to put the work in.
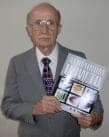
Robert H Probert
Robert H Probert Technical Services

Garner, North Carolina
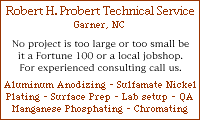
2006
March 7, 2011
Dear Robert H Probert
I enjoyed your reply very much.
I run the same process of Mn Phosphate.
Skipping the acid process as you claim improves the salt spray test.
If I run the process twice and as final test used the chromate sealer, could I skip the second acid dip? will this improve the salt resistance?
Another option is the use a different oil as final step.
What do you think?
I greatly appreciate the time you take to guide me.
Many thanks
Shay
- Israel
I do not understand what you mean by "second acid dip". Any acid pre-treatment will enlarge the grain size of the manganese phosphate crystal (read, "make more coarse")
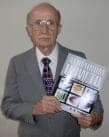
Robert H Probert
Robert H Probert Technical Services

Garner, North Carolina
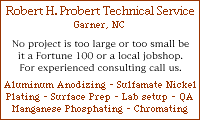
March 10, 2011
March 24, 2011
Having this problem with an arsenal. They use acetone to clean prior to salt spray testing. This is wrong. Remember first that manganese phosphate coating is a nonmetallic organic coating. Per ASTM B117 para 6.3 it states:
6.3 Specimens coated with paints or nonmetallic coatings shall not be cleaned or handled excessively prior to test.
You don't clean them. Also it is documented in other cases of alloy steels that sometimes "surface carbon" is what rusts not the actual base metal item.
BB NSCC - Fort Worth, Texas USA
Q, A, or Comment on THIS thread -or- Start a NEW Thread