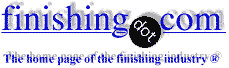
-----
Nickel plating on large/flat brass surfaces trouble
Hello,
I'm having trouble nickel plating on large flat circular surface areas of brass parts. My tank is 1000 gallons, and consists of a nickel sulphate/nickel chloride/boric acid solution. There is no agitation in the tank. Would this be the reason why I am not getting a balanced layer or enough coverage on my parts? I do not have any problems with my smaller tanks (500 gal). Please explain.
- Santa Ana, California, USA
2006
First of two simultaneous responses --
Sounds to me like a combination of poor current density control, poor tank loading and poor solution maintenance. Firstly, a large circular object will have a higher current density on its rim than in the middle, so the amount of nickel deposited in the middle will be significantly less than on the rim. This can be overcome by using robbers or secondary anodes. secondly, the lack of solution agitation will also not help you, so ensure good solution movement. Thirdly, I suspect the reason for the better performance in a smaller tank is because the andoe-cathode distances are less, so the effects of current distribution are not so obvious, especially if the anodes are of similar sizes to the workpiece and the electrodes are close together.
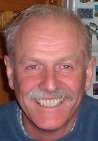
Trevor Crichton
R&D practical scientist
Chesham, Bucks, UK
2006
Second of two simultaneous responses --
Hello David,
There are different types of agitation you can incorporate. Solution spargers in the bottom of the tank that work in conjunction with your filter system. In addition to that, side to side cathodic bar agitation works well for flat parts. Replacing fresh Ni ions at the cathode surface is very important to building thickness, and minimizing hydrogen bubble formation on the part, which of course is why some type of agitation is important. You may be getting by with filtration agitation in the 500 gal tank, but the 1000 gal tank should be modified. Filter suppliers can set you up, or instruct you in all the proper equipment you will need for the tank. Good Luck!
Process Engineer - Syracuse, New York
2006
Q, A, or Comment on THIS thread -or- Start a NEW Thread