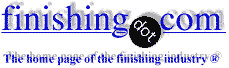
-----
Black Hardcoat Knurled Handle
Q. Recently we were asked to black hardcoat a small knurled knob (1" x 0.5"). Post coating the knurled section exhibited raw faces which appear as flashing aluminum spots. I am concerned about etching the parts for longer than 1-2 minutes as the knobs have a small threaded hole which I am racking from. First, why did it happen and second what can I do differently in the next run as the customer did not like the voids. Thank you for your assistance.
Jeff NathanAnodizing Job Shop - Providence, Rhode Island, USA
2006
A. Note that hard coating goes half into the surface and half on top of the surface, so when you hard coat a thin edge (as with a knurl), then the whole edge is converted to hard coat which is very brittle aluminum oxide, and these sharp edges break off exposing bare aluminum. There is nothing you can do at hard coat thickness. Reducing the thickness will help, but never completely cure. The thicker you go, then the more of the sharp edge quits being soft ductile aluminum metal and becomes very brittle aluminum oxide - which breaks off.
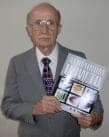
Robert H Probert
Robert H Probert Technical Services

Garner, North Carolina
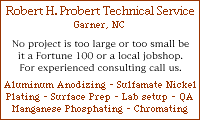
2006
A. Jeff,
Knurling is not a 'clean' operation. Flakes are created in the knurling process and can adhere to the part. If not removed prior to anodize, they too will anodize, and then if removed, leave the bare 'contact' point.
If done properly, knurling will leave little flakes, but nonetheless, a mechanical brushing of the knurl can be done to remove the stubborn flakes prior to anodize.
- Colorado Springs, Colorado
2006
A. The better way to go with knurled knobs of 1.25 or larger is a diamond cut of .032 dp and a larger top surface material of .093. This will leave enough of a knurled surface to grip the fingers adequately for turning.
John Huet- Chicago, Illinois. USA
October 5, 2012
Q, A, or Comment on THIS thread -or- Start a NEW Thread